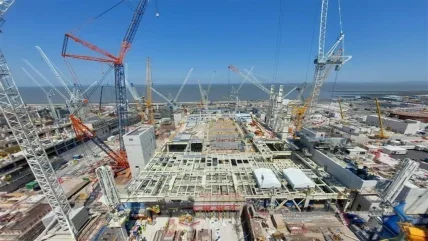
The APCO Technologies beams measure up to 44.77m long, with the larger of the two weighing 138,000kg. Both are pivotal to the function and safety of the reactor for its entire 60-year operating life.
During construction, the beams play a crucial role in installing the reactor pressure vessel and other parts of the nuclear steam supply system.
Osprey said components this large cannot travel overland, so it coordinated suppliers and suggested using a combination of, for example, barges, cranes and self-propelled modular transporters (SPMTs).
The first beam came to the Hinkley Point C site via Avonmouth. Osprey factored in all kinds of environmental factors such as weather, tidal conditions in the Bristol Channel and conditions in the River Parrett. It also needed to bear in mind planning constraints for the barges, and to be mindful of local residents’ needs too.
To move the beam across the site, Osprey loaded it onto a specialist, four-file ten-axle SPMT. To ensure integrity and safety, the SPMT moved at less than 3mph during transit, and under fine control during final positioning for unload onto storage supports using the SPMT hydraulics at the construction platform.
“Every millimetre of each move needs careful planning, and is signed off by a team of engineering, transport and safety specialists,” said Osprey.
“Universally, lifting is a high-risk activity, but our solution used a combination of transport options to mitigate some of that risk. The direct delivery by SPMT also meant there was at least one less critical lift to perform, which means we’re improving safety, the delivery programme, and overall costs.”
Meanwhile, at the back end of last year, a polar crane with a carrying capacity of 390 tons was installed at unit 2 of the Russian Kursk-II nuclear power plant, as reported by Nuclear Engineering International.
Specialists at JSC Energy Special Installation lifted and installed the polar crane bridge on rail tracks at around 38.18m using a heavy tracked Liebherr crane with a lifting capacity of 1,350 tons.
“During the construction of the nuclear power plant, the polar crane is involved in numerous operations for the installation of elements of the construction part and equipment of the sealed zone of the reactor building: reactor vessel, steam generators, pressure compensator.
“And after the start of industrial operation of the power unit, it will carry out transport and technological operations during scheduled preventive repairs of the power unit,” explained the first deputy director for the construction of new blocks at the Kursk site, Andrei Osharin.
By optimising the installation process of the polar crane bridge assembly along with balancers, as well as applying a number of improvement proposals aimed at reducing the process time, the installation of the polar crane was carried out ahead of schedule over six days, said Mikhail Pinchuk, director general of JSC Energy Special Installation.
The polar crane was manufactured at the plant of JSC Tyazhmash in the Russian city of Syzran.