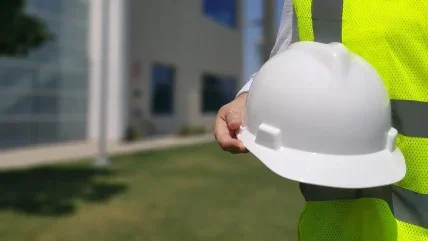
The question was posted in the chat forum of the UK’s Institute of Occupational Safety & Health’s website in February: Should a factory with overhead cranes be a hard hat area? The questioner’s workplace has cranes but is not a hard hat area, a point picked up on by a visiting safety assessor.
The three respondents all agreed that hard hats were a good idea for working within lifting zones. But to what extent does the industrial world follow this advice?
I have visited construction sites and factories around the world. Except in certain countries such as China, Peru or India, I have generally been required to wear a hard hat when visiting any construction site. Often, I have been required to put on steel cap boots, high visibility vests and even protective glasses. Occasionally, in certain countries, I have been significantly more protected than the workers on site facing daily hazards.
When visiting factories, however, the picture has been much more mixed. I have visited mobile crane manufacturing factories in Germany and been free to walk the floor with no personal protective equipment (PPE) whatsoever and, except for the obvious such as welders’ masks and gloves, little has been in evidence among the workers. I have visited similar factories in the USA and generally found a greater level of concern about PPE. Glasses, hard hats and high visibility jackets have been required, by workers and visitors alike.
The legislation in European countries is not significantly different from that in the USA. In the USA, section 1926.100 of the Occupational Safety and Health Act states: “Employees working in areas where there is a possible danger of head injury from impact, or from falling or flying objects, or from electrical shock and burns, shall be protected by protective helmets.”
The UK’s Safety and Health at Work Act 1974 makes no specific mention of helmets or hard hats, but says: “It shall be the duty of every self-employed person to conduct his undertaking in such a way as to ensure, so far as is reasonably practicable, that he and other persons (not being his employees) who may be affected thereby are not thereby exposed to risks to their health or safety.” This underpins all other health and safety regulations.
The Construction (Head Protection) Regulations 1989 made hard hats mandatory on UK construction sites. Sikhs who wear turbans are exempt and there is regular discussion about exempting Rastafarians with large dreadlocks. However, there is no specific requirement in the UK for hard hats to be worn in factories.
The 1961 Factories Act stipulates that measures should be taken to reduce the risk of workers being crushed by bridge structures and to prevent falls from height. Here again, there is no mention of hard hats to be worn.
In 1992 the Personal Protective Equipment at Work Regulations (PPEW Regulations) were introduced in the UK. These state that PPE should always be considered as the ‘last resort’ to protect against risks to health and safety. Engineering controls and safe systems of work to remove risks should always be considered first. But where a risk remains, PPE (including hard hats where appropriate) must be worn.
What this all amounts to is that it is up to safety managers to assess the risks and make the call. On this basis, it is safe to say that if heavy (or even any) loads are being lifted overhead, then anyone below should where a hard hat.
In Japan, the Industrial Safety and Health Regulation (Ministry of Labour Ordinance No. 32, 1972) specifies certain industries in which all workers must wear hard hats. These include construction, shipbuilding, forestry, quarrying and loading/unloading in harbours. There is no specific mention of factories or of cranes but there is a general requirement for employers to protect employees from the risks of falling or flying objects.
Yet the interpretation of these laws varies, not just from country to country but from industry to industry and from town to town.
Three good reasons
There are three strong reasons for employers to ensure their workers wear hard hats and other PPE. First and foremost is to reduce the risk of injury, or minimise the injury in the event of an accident. The second is to foster a culture of safety and demonstrate that a lax approach will not be tolerated. The third reason is to minimise the liability risk and keep the insurance companies on side.
This third reason plays particularly strongly in the USA where employers have learned to fear the liability issue. This issue is growing quickly in Europe but has yet to reach the level that the USA experiences. But is PPE in a factory environment just a gesture that enables the owner can demonstrate that he takes safety seriously, or is it really a valid and necessary precaution?
Even where there are regulations that say anyone working within a lifting zone has to wear a hard hat, there is still plenty of room for interpretation. Is it enough just to step aside as the crane approaches overhead?
One [UK] correspondent on the IOSH website explains how things work in real life says: “I have experience of factory work where overhead cranes are employed for moving steel bogies and other equipment when maintenance operations are being undertaken. It was not previously the practice to wear any headgear in these locations, on a production line, but when operating the equipment employees on the production line were under and directly in the danger area of the lifting operations. The [UK] regulations state that all persons should be cleared from the lifting zone unless directly involved in the lifting operation – not possible in this case as they had to man the production line.
“Quite obviously, in any operation no one wants anything to fall, but it could happen and in most instances, where it contacts a person there will be injury or fatality. The wearing of hard hats during operations is mandatory if you are within the lifting operation zone. If the process is continuous then it is likely that wearing of hard hats in such an area (as on a production line) should be a mandatory requirement.”
Ideally, of course, a factory should be designed so that loads are not moved over the heads of production line workers.
So if people working in crane zones should wear hard hats, what about crane maintenance technicians and crane operators?
Yukinori Ouchi, director of the Japan Crane Association, says that in Japan a crane operator working in a cabin might not be required to wear a hard hat, but – depending on worksite conditions – an operator on the floor using cable or radio control will have to wear one. Workers in the vicinity the lifting operation are also required to wear hard hats, although this again depends upon the worksite conditions.
Ouchi says: “Generally in Japan, workers engaged in the heavy material handling operation wear hard hats for ensuring safety, although a strict interpretation of the safety regulation may not force employers to have workers wear hard hats.”
Michael Mitchell is a California-based district manager with KCI Konecranes’s US maintenance subsidiary Crane Pro Services. He says: “Crane Pro Services technicians are not required, at this time, to wear a hard had when working on EOT cranes. We must, however, adhere to the rules and regulations of the facility we are working in and often this does require the use of a hard hat. The company provides our employees with all necessary personal protective equipment.”
Does he think EOT crane operators should wear hard hats? “In my opinion, yes,” he says. “With a moving, structural/mechanical piece of equipment running overhead, the potential exists for anything from a nut and bolt to forgotten tools to a larger component to become loose and fall off the crane or runway. The load on the crane itself is really not the issue.”
Other workers should stay out of the lifting zone, he says. “You should not work or operate under a load and a hard hat will not help you much if the load falls on you,” Mitchell says. “We have a few customers who require the operator to wear a hard hat, but not those other factory workers who are exposed below the crane. In my opinion, they too should be wearing hats for the same reasons as the operator.
“Based on my experience in the western US, I would say there is a greater number of manufacturing facilities with EOT cranes that do not require hard hats against those that do. Specific industries make it mandatory. In our area, for example, hard hats are required (although not always by law) at any power plant, steel mill, steel service centre, paper mill and mining operation.”
It seems obvious that a steel mill will be more alert to safety risks than, say, an electronics assembly plant. Chris Rijbroek is a health and safety manager with Anglo-Dutch steel producer Corus in the Netherlands. “Corus policy is that everyone will be provided with sufficiently adequate PPE. This means that employees have to wear hard hats in most of the plants and their surroundings. This is according to Dutch law, which states that appropriate measures have to be taken to avoid injury.”
Rijbroek explains that employers have to undertake risk assessments that will determine whether hard hats must be worn.
He says that operators of remote controlled cranes at Corus have to wear hard hats. Operators working from cabins do not have to wear them in the cabins but must wear them while going to and coming out of their cabins.
Rijbroek supports Mitchell’s point about dropped loads not being a significant risk. “The risk of loads dropping can hardly be an issue because no hard hat will protect you against the effects of a 10t coil dropping from the crane. But when things are moving above your head, some parts can drop off (like the screwdriver of the mechanic who was there the previous week).
This is the basis to oblige employees to wear hard hats.”
He adds: “Cleaning and checking and good maintenance is an even a better way to avoid injuries because it reduces the risk instead of protecting against risk.”