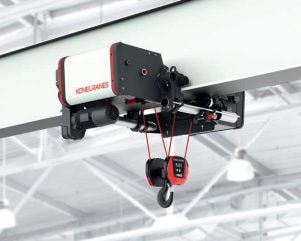
Konecranes has launched its flagship X-series industrial crane, the successor to its CXT model with a new compact design and wireless upgrade capabilities that can adapt to customer needs now and in the future, with the first deliveries expected in Q4 2024 in EMEA, with other regions to follow later this year.
“The flagship crane builds on a quartercentury of success for the CXT, which was launched in 2000 and to date has sold well over 100,000 units globally,” said Jussi Luokomaa, product manager, ISE (Industrial Service & Equipment) EMEA, Konecranes.
“We expect to see good demand for the Konecranes X-series across multiple industries including general manufacturing, making it a core product for the company for years to come.”
By applying sustainable design and material choices, the X-series shows how Konecranes is shaping next generation material handling for a smarter, safer and better world.
Its new design and component improvements include, for example, a more compact and efficient motor and synthetic rope, leading to efficiency improvements. The Design for Environment (DfE) approach was applied in the X-series product development, aiming to reduce the overall environmental impact of the product.
The X-series will come equipped with the latest radio and software technology and Konecranes’ TRUCONNECT remote monitoring capabilities, enabling safe and secure wireless updates and upgrades.
In the future customers will be able to buy the crane and then upgrade to Smart Features such as Follow Me, Sway Control or Snag Prevention, opening up the possibility for eventual on-demand business model opportunities for Konecranes.
According to Siemens, whether it’s rising electricity prices or efficiency guidelines from the energy transition and the global climate protection agreement: Industrial operations and building and infrastructure operators are under growing pressure to reduce electricity consumption. It believes a transparent consumption data provided by a power monitoring system lays the groundwork for the appropriate optimization measures.
The energy efficiency of buildings and plants is subject to increasingly stringent legal and standards-based requirements, from the Energy Efficiency Directive (2012/27/EU) to the European Green Deal, which aims to make Europe the first climate-neutral continent by 2050.
To achieve that goal, EU Member States are establishing national requirements, measures, and subsidies like the energy certificate for buildings in Germany.
In a recent webinar with hosts Andreas Hierl, business developer, Siemens and Vijay Pote, consultant support, Totally Integrated Power, Siemens, they explain how electricity prices have multiplied in recent years.
A sharp increase was already noticeable in 2021. Since then, the situation – against the backdrop of the current geopolitical situation and the resulting shortage of raw materials – has worsened.
One way to manage this challenging situation is with systematic power monitoring, which makes all electrical energy flows highly transparent.
This lays the groundwork for operational power management based on the ISO 50001 and 50003 global standards and for regular energy audits.
It’s also an important way to reduce energy costs, optimize plant operation, and improve fault tolerance. The technological foundation is power monitoring systems.
A power monitoring system consists of measuring devices that acquire energy data and analysis software that visualizes and assesses this data. Digitalization makes it possible to monitor the electrical infrastructure in previously unknown ways and to make energy data visible.
One example of this analysis software is Sentron Powermanager from Siemens.
This tool has comprehensive basic features that process and export data for energy reports. Sentron Powermanager can be used both as standalone software and as an integral part of the Desigo CC building management system.
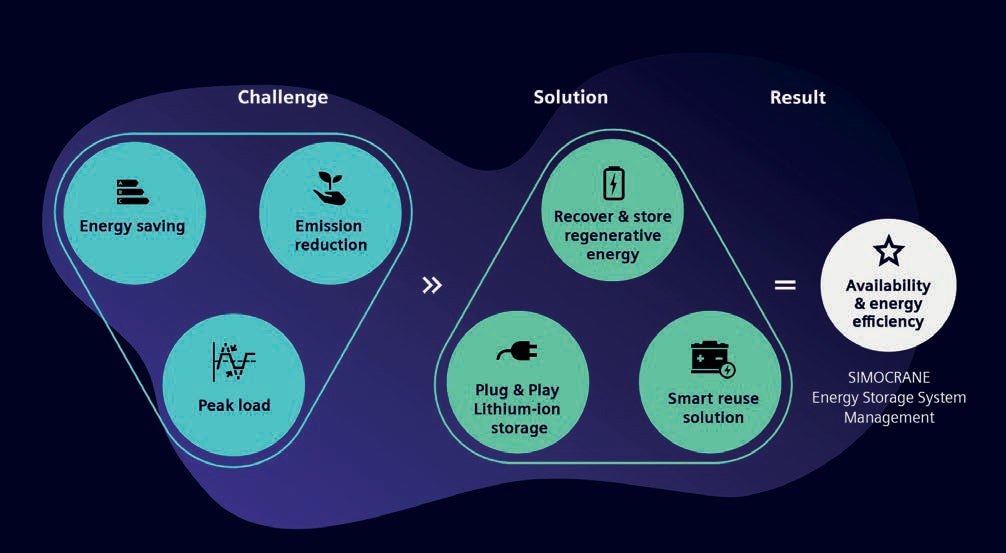
It also permits the straightforward analysis of energy consumption by displaying important characteristics on a dashboard. The evaluation of load peaks and the load profile quickly results in energy savings.
“The first step toward satisfying the law is to determine the current status of your energy efficiency at all levels, including in low-voltage power distribution systems.
To do this, power monitoring systems use software to record, analyze, and visualize a company’s power flows,” said Hierl.
“The database this generates enables energy consumption to be analyzed and potential energy savings to be identified, and then improvements can be calculated and implemented.
“The data that’s collected and the analyses based on power monitoring also lay the foundation for an operational energy management system based on ISO 50001, as extended by ISO 50003 and ISO 50006.
“To obtain certification in accordance with these standards, companies need to prove that they’re constantly improving their energy efficiency. In return, they benefit from ongoing savings, funding, and competitive advantages.”
Continuously monitoring power distribution allows operators to identify critical plant states early on, which in turn ensures high plant availability.
Energy data can be acquired by measuring devices as well as communication-capable protection and switching devices.
The latest Sentron air circuit breakers 3WA are a practical example. They combine protection and measurement functions in a single device.
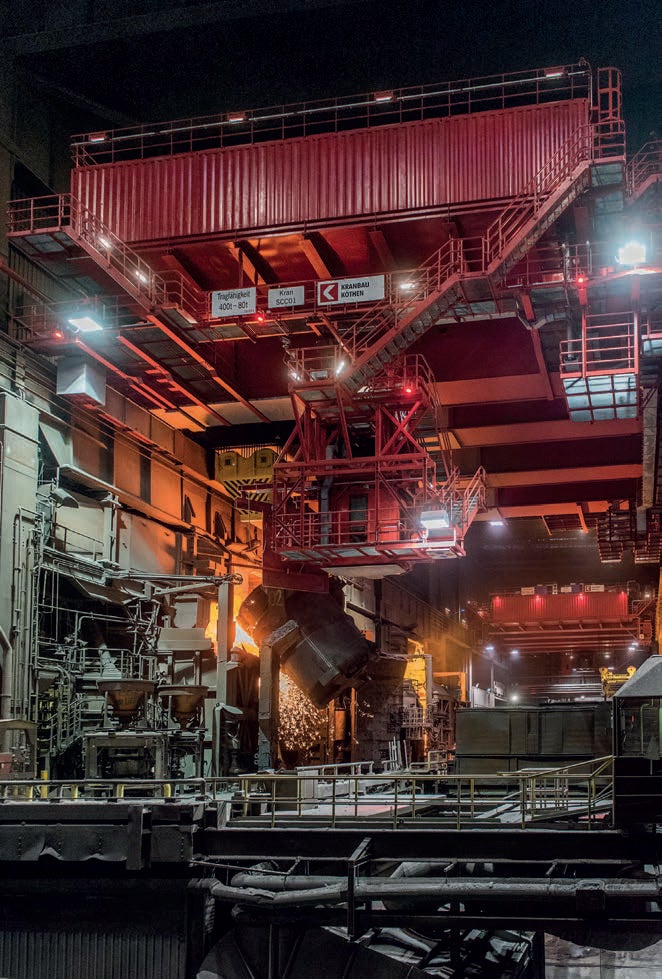
The electronic trip unit (ETU) is designed to acquire a variety of data on energy, power quality, and circuit breaker states in normal operation.
The data acquired is usually transferred to higher-level systems via standard protocols. Multiple communication protocols can also be used simultaneously for fast and powerful data transfers.
“No planner can manage without strategies for improved energy efficiency and transparency in low-voltage power distribution. You need measurement strategies for permanent power monitoring that can be flexibly adapted to changing requirements – and that can be expanded to include energy management once companies reach a certain size.
The foundations should be laid when the power distribution system is still in the planning stage to avoid extra costs and effort in the implementation stage.
“The law requires planners to take national requirements into account when designing an efficient power distribution system: for example, DIN VDE 0100- 801 in Germany and IEC 60364-8-1 internationally,” says Melina Hagelauer, business development, G2M Energy Distribution Systems.
Another example is the Sentron 5ST3 COM auxiliary switch/fault signal contact. It supplements standard circuit breakers with additional monitoring features like operating hours, operating cycles, and trip counters.
Direct data transfer to the cloud is also made possible by the Sentron Powercenter 3000 IoT data platform and the Sentron Powermind cloud-based app.
The Sentron Powercenter 3000 fits inside any control panel where it serves as a central interface. The IoT data platform and software offers a number of options for visualizing and analyzing data and lays the groundwork for operational power management.
All data from communication-capable field devices, including measuring, switching, and protection devices, is transferred to the Sentron Powercenter 3000 and displayed in the Web interface in a customizable format.
The Sentron Powermind cloud application enables location- independent, real-time analysis of energy and plant data in the Insights Hub cloud solution.
It provides an overview of current power consumption – by individual electrical consumers or entire plants – and a comparison of different time periods. It also allows operators to identify powerguzzlers, balance load peaks, and reduce overall energy costs.
Sentron Powermind and Sentron Powercenter 3000 IoT data platform work together, making it easy to transition to cloud-based power monitoring.
The systematic use of IoT platforms has additional advantages for electrical engineering and building technology, even beyond cloud- based power monitoring. It greatly reduces expenditures for a separate IT infrastructure for technical building management.
In addition, huge amounts of data can be stored and processed in the cloud and then made available for comprehensive analyses regardless of location.
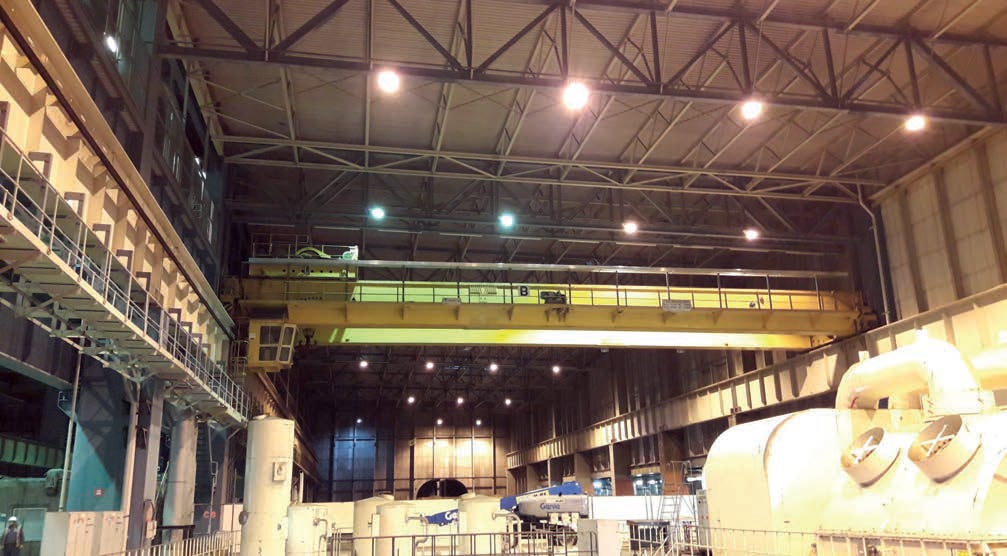
For example, Siemens’ open IoT platform Insights Hub makes it possible to process, evaluate, and compare large volumes of data from different devices and systems in buildings and infrastructures. The potential is enormous.
Much shorter downtime and even higher energy efficiency are just two examples.
According to predictive maintenance provider, Senseye, large plants lose an average of 27 hours a month to machine failures. Digital, dynamic control of industrial cranes on the factory floor is a largely unknown, but pivotal, source of uptime.
“When using a magnetised crane to lift heavy or bulky metal materials, operators must manage the crane’s motion with the utmost control. By retrofitting a magnet controller, operators can manipulate the crane magnet’s performance, preventing harm to staff, nearby equipment and the crane itself,” says Andy Swann, business development manager, cranes & power transmission, CP Automation.
Operators traditionally control crane magnets by adjusting the input electromagnetic current with an on/off switch. Although having an on/off switch allows the user to pick up and release loads when they choose, it can also deteriorate the magnet over time.
Because the operator can only turn the magnet on or off, the maximum current is fed in and then withdrawn when the load is released. After a series of lifts, the magnet can start to overheat, and the asset will sweat because of the current flow. Consequently, operators and plant managers must regularly swap out the magnets to prevent potential of failure, long-term damage, increasing costs and extending crane downtime.
While contactor-based controls can be harsh on the magnet, operators can soften the impact by retrofitting a digital controller that can step-up the input current. Rather than slamming in the maximum current all at once, users can gradually increase the input according to the load or have this pre-programmed into the software. By digitally controlling the demagnetisation current, operators can maintain a full load while reducing the lifting charge in the circuit.
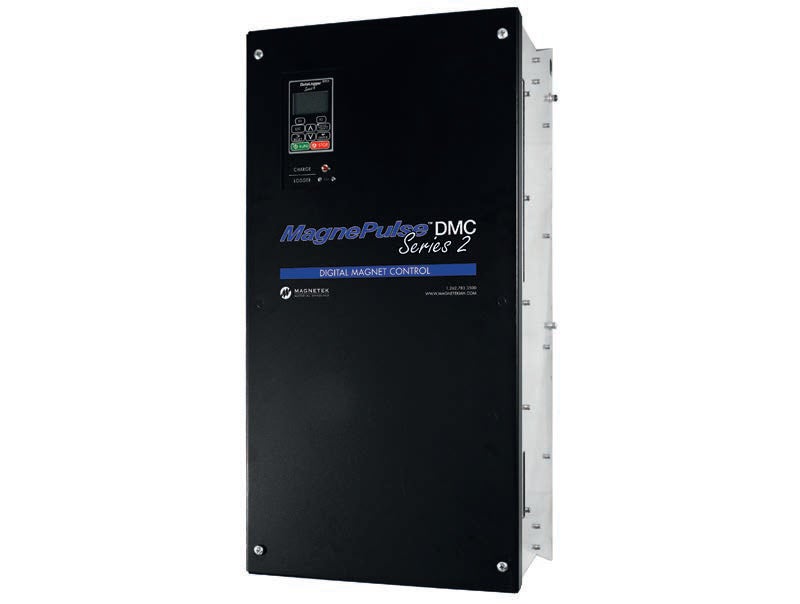
Building on the topic of digital transformation in manufacturing, Nina Gryf, senior policy manager at Make UK explained: “Manufacturers are undergoing a profound digital transformation with the potential to transform productivity, resilience and sustainability.
“The investments companies are making will play a key role in the future of manufacturing, powering them through the challenges that lie ahead with greater productivity, better skill levels and reduced emissions,” continued Gryf.
Another source of crane downtime in production facilities is a mains power failure. Nonlinear loads and voltage distortion are both significant issues because they can disrupt magnet performance and damage the crane’s electrical components. Even the slightest trip can make a big difference.
Power failures can also have a detrimental safety impact. If the crane uses a traditional contactor-based control, then in the event of an outage of power trip, the load will simply drop — posing a risk to anyone in the vicinity.
To maintain uptime, some digital magnet controllers, like the MagnePulse DMC Series 2, include power ride-through features and systems, which operators can program to maintain resilience. This ensures the magnet remains energised during interruptions and the lift continues.
“Being able to access highly accurate analytics from monitoring devices can improve predictive maintenance no end,” added John Mitchell, global sales and marketing director, CP Automation.
“Sometimes, routine maintenance activities are not needed, and adopting a more targeted approach based on need can free-up machine operators to focus on more pressing tasks.”
Some digital controllers feature data loggers and can provide performance information, such as alarm, fault and run details — giving operators real time insights into magnet performance.
Meanwhile, when running a contactor based controller, operators would need to use a digital multimeter to measure voltage, current, resistance and other electrical values to identify any disturbances.
By retrofitting a digital controller, operators can focus on predictive maintenance rather than routinely scheduling the same preventative maintenance tasks. This can improve uptime by improving asset performance and ensuring maintenance is only carried out when needed, based on the controller’s condition-monitoring analytics.
Machine failure and downtime is a significant challenge for production facilities — large plants are losing over a day’s worth of time each month because of it. Digital magnet controllers can play a subtle, but critical, role in improving uptime by preventing the need for frequent crane magnet changes, afeguarding against power outages and enabling predictive maintenance.