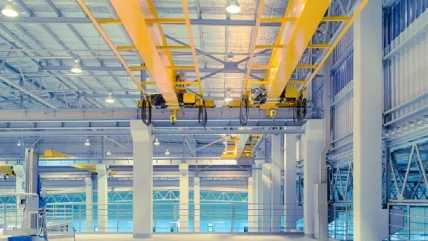
Yuantai has delivered two types of bridge cranes to a Jordanian industrial repair shop, significantly enhancing local infrastructure and supporting various industrial applications.
The installation of the overhead cranes has improved productivity and safety, addressing the customer’s need for efficient heavy machinery handling.
Specialising in large equipment maintenance, the repair shop previously relied on forklifts and manual jacks to handle heavy machinery, which was both time-consuming and risky.
The introduction of overhead crane systems has optimised productivity and safety, allowing the Jordanian facility to boost output and reduce injuries.
The shop required robust industrial overhead cranes with a mid-range lifting capacity of 10 tons, a span to cover the workspace, and a moderate lifting height of 9m.
Dual-speed hoists were essential for both rapid lifts and precise positioning.
The solution needed to fit within the existing building height and utilise the factory’s 380V three-phase power, with controls for both handheld pendants and wireless remotes.
Yuantai proposed a dual-crane system, with an LD-model single-girder overhead crane for the main workshop area and an LX-model ceiling-mounted crane for a secondary bay.
The LD crane, built to Chinese JB/T 1306 standards, features a welded U-shaped box-beam main girder and is rated for 1-32 tons capacity, which spans 7.5-31.5m and was customised.
The LX ceiling-mounted suspension crane, designed per JB/T 2603 standards, is an underslung single-girder system hung from the building structure.
It maximises floor space and accommodates up to 10 tons, with spans of 3–15m. This crane provides excellent clearance above loads and is ideal for workshops with moderate heights.
Each crane was equipped with a Yuantai dual-speed MD-model electric wire rope hoist, offering two lifting speeds for quick travel and precise positioning.
The MD hoists, known for their compact structure and durability, were configured to meet the specified capacities, ensuring efficient and safe operation.
Yuantai said the overseas project faced challenges in language and logistics.
Its engineers collaborated with bilingual staff to ensure clear communication, exchanging detailed drawings and holding video conferences to review the crane layout and lifting plans.
A local logistics partner was engaged to manage shipping and customs, and a Yuantai team handled installation works.
The Yuantai team checked the existing steel runway for alignment before mounting the LD crane’s end trucks and bridge girder.
The LX suspension girder was secured to the ceiling supports. Each MD hoist was tested, and no-load trials were conducted to calibrate limit switches and overload devices.
Heavy components that previously required multiple lifts could now be moved in a single cycle, making tasks like positioning large engine blocks faster and more precise.