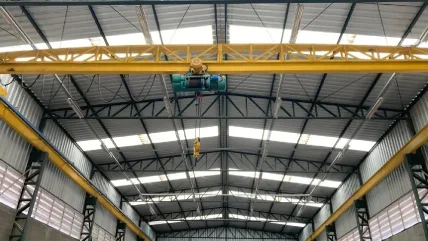
China-based crane manufacturer Yuantai Crane has installed a 3-ton LH Bridge Crane in a Maldivian workshop, providing a crucial lifting solution for the marine engineering sector.
With low-headroom design and corrosion-resistant features, the crane addresses the need for effective and safe material handling in confined spaces.
Yuantai designed the 3-ton LH Bridge Crane with a double-girder overhead structure, ensuring stability and efficiency in workshops with height restrictions.
It includes a compact electric hoist mounted between the girders and features anti-corrosion coatings on all exposed surfaces.
The crane features a rated load capacity of 3,000 kg, a span of up to 20 metres, and a configurable lifting height.
Yuantai, in its statement, said: “The customer operates within the marine engineering and boatbuilding sector, a critical industry in the Maldives. Due to its dispersed island geography, the country relies heavily on marine vessels for transportation, tourism, and logistics.
“The company specialises in ship repair, hull fabrication, engine fitting, and vessel customisation. These operations involve moving heavy components such as boat engines, structural steel frames, and prefabricated ship sections within confined workshop areas.”
The Chinese crane maker built the 3-ton LH Bridge Crane from marine-grade steel with a hot-dip galvanised finish.
It includes sealed bearings and electrical components to withstand moisture, and the hoist is equipped with an overload protection system, emergency stop, and limit switches for safety.
The control system offers wireless remote and pendant control, with a VFD-controlled travel speed and an IP55 motor enclosure for water and dust resistance.
Before adopting the LH Bridge Crane, the customer faced challenges with manual hoists and forklifts, which increased the risk of workplace injuries and operational inefficiencies.
The humid, salty environment also corroded conventional steel equipment rapidly, making it difficult to meet safety standards.
Yuantai completed the installation of the crane within four days, with local technicians trained in advance and supported remotely by its crane engineers.
Currently, the crane is effectively handling tasks such as lifting marine diesel engines, positioning steel beams, and transporting parts within the workshop.