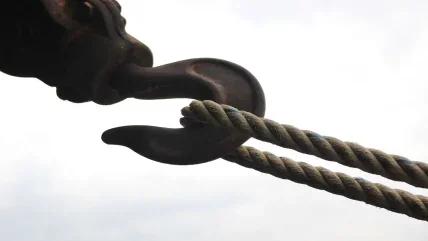
Designed to raise and lower large vinyl-type sheets in a purpose-built ‘wet area’, the system comprises four floor-mounted Yale RPE 400V three-phase winches offering 150kg safe working load (SWL) and 20 Pfaff roof-mounted diverter pulleys coupled to four 12m-long tubular spreader beams.
Each winch raises and lowers one of the 12m-long spreader beams, which attach to the vinyl sheet via load-bearing karabiner clips. Each vinyl sheet weighs approximately 60kg. The winch system raises the vinyl sheets in a level position – this capability permits easy drying of the vinyl sheets after pressure washing, a process that removes any unwanted residual substances from the most recent hire job.
The customer can operate all four winches individually via its own wall-mounted, low-voltage pendant controls, allowing the lifting of a single vinyl sheet as required at any time. Each winch sits in purpose-manufactured mounting frames secured to the floor using four Hilti expansion anchors.
The system facilitates a quicker and less labour-intensive turnaround of the vinyl sheets during busy periods of hire.
The scope of supply for Hoist & Winch included all pre-installation survey work to ensure correct the alignment and positioning of each winch, diverter pulley and all associated equipment, including top and bottom hook geared limit switches. The company also provided installation over a seven-day period and subsequent commissioning. Further responsibilities included all wiring and load testing of the whole system. Once complete, Hoist & Winch issued a Lifting Operations and Lifting Equipment Regulations (Loler) Thorough Examination report.
The room in which the washing, lifting, drying and lowering of vinyl sheets takes place is a purpose-built and enclosed ‘wet area’ with a cambered floor and drainage around the perimeter to support the removal of excess water during cleaning. Hoist & Winch provided PVC weather covers for the winch control panels to ensure safety at all times.
To ensure smooth handover, Hoist & Winch undertook operator training covering overview of the winch units and main components; operating controls and features; periodic checks and lubrication; annual inspection, service and certification requirements; and practical operation by each operator.
Hoist & Winch director Andy Allen says: “This project set out a number of important stipulations to which we had to respond comprehensively and efficiently. A successful outcome that meets with the project’s ambitions, delivered on-time and on-budget, is our primary aim. Once again our professional and experienced team of engineers here at Hoist & Winch came up with a safe, reliable, high-performance solution to the satisfaction of our valued customer.”
Sign up for FREE weekly newsletter
Sign up for FREE digital edition of the magazine
RELATED STORIES
• Hoist & Winch supplies tandem lifting hoist for UK flood defence system