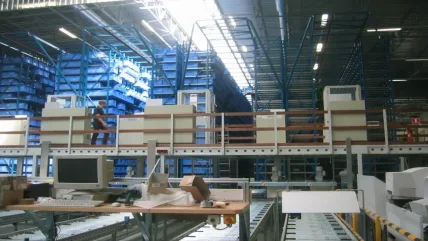
Warehouse space is at a premium. From growing businesses to those looking to keep stock closer to home, everyone wants logistics and industrial property. And it’s not just the demand for such property that has increased its value, but the way we use it.
The past few years have brought supply chain risk to the forefront of many business strategies, and keeping more stock closer to hand is a compelling proposition, which is just one of the factors increasing demand for warehousing space.
Warehouses are often affectionately referred to as sheds, and while storing stuff until you need it remains a key function, they are now more appropriately described as distribution centres or even intralogistics hubs. The trend for near-shoring operations from pick and pack to value-add services closer to consumers speeds fulfilment and minimises risk. This increases demand for space but it also requires that space to do more than just storage.
Steve Purvis, managing director at consultancy Bis Henderson Space, says that “businesses are seeking improved speed to market, to offer consumers ever-shorter lead times and higher levels of availability across increasingly customised and individualised product ranges, both flexibly – because consumer demand is now so rapidly changeable – and sustainably”.
He describes this as a trend for ‘postponement’ – carrying out final assembly and finishing in the warehouse in response to firm orders rather than at the factory for stock. “The demand for warehouse space that can efficiently support quasi-manufacturing operations and workforce will therefore increase at the expense of ‘basic sheds’,” says Purvis.
So if the days of basic sheds are numbered, optimising storage into denser configurations is an obvious but vital way of creating space that can be used to increase volumes or indeed to support more complex warehousing operations.
“Dense stock holdings can optimise storage space, potentially reducing warehousing costs,” says Ed LaBruna, partner at Janus Automation .
He points out that dense storage also addresses the growing demand for extra intralogistics services: “Additionally, efficient stock density can streamline order picking and packing processes, enhancing overall operational efficiency.”
Reconfiguring storage is an easier way to increase capacity than expanding your footprint by moving or extending your warehouse or distribution centre. So dense storage and using less of the footprint obviously saves real estate costs but it also feeds through to wider benefits.
“This smaller footprint has a positive impact on various aspects, including lowered construction expenses and a decreased carbon footprint due to reduced energy consumption (shorter distances, less need for A/C and heating, and lighting). Simultaneously, denser storage leads to quicker delivery of parts/goods to the next process step, thereby enhancing the overall performance of warehouse operations,” says LaBruna.
Finding the optimal way to condense storage will depend on many factors such as the nature of the site itself, the product range, the tasks and speeds required and the equipment to be used.
For example, LaBruna explains how product profile will affect the design of the system. “Homogeneous products lend themselves to simpler rack designs, while extensive product ranges necessitate careful analysis to optimise storage for the product mix. This analysis aims to balance the efficient storage of various items while ensuring the flexibility to accommodate smaller products within the area designated for larger items when required,” says LaBruna.
Such in-depth appraisal must be applied to every business process and it cannot be a unilateral top-down assessment. Edward Hutchison, managing director of Bito Storage Systems, elaborates on the details that must be borne in mind: “Factors include stock profile, [and] investment costs of the racking installation; handling/ transport costs per item, which includes the cost of internal transportation and labour; handling capacity measured in picks, i.e. the quantity of items retrieved per unit of time; optimum utilisation of the available headroom and footprint of a warehouse or storage area.”
Headroom is a pertinent issue. Mezzanine floors are one way to make use of overhead space, but modern high bay racking goes much higher, and narrower aisles can squeeze more into existing space.
Martin McVicar, CEO and co-founder of Combilift, points out that the dimensions of the premises will dictate, for example, the height of racking: “You can’t go above the roof in any case!”
And height is what he recommends: “The first and easiest way to increase storage density in any warehouse small or large is to maximise height utilisation, and to consider the warehouse in cubic storage capacity. Warehouses are a revenue stream, but underutilised space is either a cost or waste. When aisle widths are reduced and racking is added to fill vacant spaces, warehouse storage capacity can be increased by up to 50%,” reckons McVicar.
The capability of materials handling equipment has a significant influence on any intralogistics strategy. Broadly, the options will be stacker cranes, forklift trucks, perhaps a fully automated storage and retrieval system (ASRS) or something in between such as automated guided vehicles (AGVs). There are many permutations of these, each with its benefits, limitations, and costs which need to be weighed.
“Mainstream counterbalance or reach trucks for example, can only move forward or backwards, so require wide aisle widths as well as large areas to be put aside for manoeuvring,” says McVicar
“Using more manoeuvrable forklifts such as multidirectional or articulated models enables aisle widths to be narrowed down, increasing the number of aisles and consequently storage bays and or pallet spaces.
“As the name implies, very narrow aisle (VNA) truck are designed to work in extremely narrow aisles and high bay racking and can lift to heights of around 18m. Combilift’s Aisle Master range of articulated trucks can lift to 15m and have the added advantage over traditional VNA trucks of being much more versatile for indoor and outdoor operation,” says McVicar.
Stacker cranes are another option for taking height even further, in similarly compact layouts. For example, Lidia Fitsova, business development and marketing manager of Hubmaster North America, explains that its typical solutions can operate in very narrow aisles, just 22in (56cm) more than the depth of the pallet: “We are able to go as high as 80ft (24m) in a high-density warehouse working in single aisles as a push-back system.”
She also points out that in a single aisle its system can store seven pallets deep: “That is a great way to utilise your vertical storage, which is not something that typical AGVs, for example, would be able to do as they have height and weight limitations.
“We also provide multiple-aisle stacker crane solutions that create high-density solutions with a height of 45ft (14m) tall. Because we are able to switch to multiple aisles and access pallets on all sides with the single Hubmaster stacker crane, this is a great alternative for a lot of warehouses,” says Fitsova.
Bito’s Hutchison says there are even higher options: “High bay automated warehouses served by stacker cranes can theoretically attain heights in excess of 40m, though just over 30m is more common.
“A high-rise narrow aisle structure will make good use of vertical capacity and efficient use of floor space. As a rule, narrow aisle facilities are serviced with man-operated stacker cranes or order picking trucks. This allows picking of smaller unit loads from all racking levels. Guide rails and inductive steering ensure that service vehicles always keep the ideal distance to the installation.”
Of course, ASRS and similar automated systems can also go high and can offer much denser storage for small items than pallet racking allows. There are other benefits to automated storage too aside from exploiting space. By reducing human errors automated systems also minimise risks and offer operational efficiencies.
In fact, LaBruna reckons that automated material handling is likely to become a crucial component of intralogistics: “Automation offers a range of advantages to companies… and businesses that postpone the implementation of automated warehouses could potentially face significant challenges in establishing a competitive presence in the future marketplace.”
Automation is sometimes viewed as being expensive, but with e-commerce driven demand for just-in-time fulfilment the business case is stacking up for more distribution centres. Bito’s Hutchison says “automation is stepping closer into the economic justification zone for more operators who are juggling higher volumes, a growing demand for faster order fulfilment and greater value on the one hand, with rising staff costs on the other”.
However, McVicar warns that buy-in cost can be prohibitive for smaller operators.
“Initial investment is considerable, and break-even return on this investment is likely to be in the region of many years. In addition, specialist ASRS storage systems when installed are not easily reversed to regular warehouse layout. Optimisation before automation is key to providing flexibility within the warehouse while still achieving maximum return on investment,” says McVicar.
LaBruna argues that with a thorough and holistic assessment of potential investment in automation the efficiencies will speak for themselves, but he also agrees as to the value of optimising existing resources and suggests that phased improvements can work well for hesitant investors.
“Modular racks are a versatile storage solution that allows small businesses to start with a basic set-up and then expand gradually as their needs grow… Existing manual cranes could be upgraded in phases to become semi-automatic or fully automatic systems… This approach is cost-effective and scalable, making it well-suited for businesses with limited resources that want to accommodate future growth without investing heavily upfront,” says LaBruna.
So there seems little doubt that maximising storage through higher and denser options is a smart way to unlock the potential of your warehouse. There are a range of materials handling options and configurations that will suit different operations, and although a considered approach will be required, squeezing denser storage in could release huge value.
Shell takes stacker crane on rack clad extension
Shell Lubricants, a global leader in the production and distribution of lubricants and greases, took on Hubmaster for a 6,500ft2 rack-clad extension to a warehouse in Spain.
Shell needed a warehouse solution that could handle a large volume of products directly from the production line, including more than 3,000 pallets of different sizes and weights. It also wanted an energy-efficient and eco-friendly improvement, that would increase efficiency, accuracy and productivity while reducing costs and errors associated with manual inventory management.
In order to maximise the available footprint Shell opted for a rack-clad building, in which the racks constitute the walls and support the exterior cladding. The solution featured a single-aisle Hubmaster stacker crane to access the racks that form the walls. These go up to 22m in height and are managed on a Lifo basis (last in, first out). These are push-back racks and the system is fully automatic.
The system includes the management of existing automated guided vehicles (AGVs), which transport finished products from production lines to the conveyors at the infeed positions of the automatic warehouse.
The HMWare WCS software by Hubmaster is a customised solution for warehouse management to integrate with the existing production and transport systems, including AGVs and conveyors. The HMWare system was adapted to manage storage in an old legacy warehouse as well.
Hubmaster provided a complete turnkey solution for warehouse automation, including the design and construction. The entire system was designed with a focus on safety, including the use of advanced sensors to prevent collisions and ensure worker safety. The system also improved overall efficiency and productivity by increasing storage capacity and streamlining inventory management.
Automated storage speeds throughput
Terberg Benschop is a Dutch manufacturer of vehicles and tractors that are used in shipyards, airports and construction, for example. It is a family-run company with an annual revenue of €825m.
Terberg took on Knapp for a new centralised production warehouse including an automated small parts storage facility. The system included an OSR Shuttle with two rack line systems, 25 levels and 50 shuttles for containers of up to 50kg. The new system also has four decanting workstations, two Pick-it-Easy Flex picking stations, two dispatch stations, and Knapp’s KiSoft One IT system with Webservices interfacing to the incumbent Dynamics AX.
“The choice for an automated solution was a big step for Terberg. We felt the need to work together with a supplier that has already proven systems in action worldwide, that also offers the possibility for local support and maintenance,” says Alexander Kühne, supply manager at Terberg.
The OSR-Shuttle’s dynamic quadruple-deep storage provides 14,250 load unit locations for containers measuring 600x400mm or 28,500 load unit locations for containers measuring 400x300mm. The system contains a shuttle for every level and rack line system, which handles all storage and retrieval movements.
“Of course, the goods-to-person system has a higher capacity by eliminating the time a person would need to navigate through the warehouse,” says Kühne.
“Other advantages are that the pick-to-light system supports the picker and helps avoid mistakes in item and/or quantity picked and that working according Fifo [first in, first out] can be forced due to the fact that every new goods receipt is stored in a new empty container,” Kühne adds.
The new system has put Terberg on course to achieve throughput of 500 containers/hour by 2027.