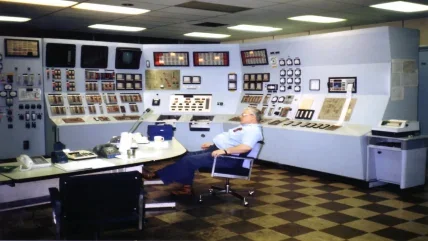
Digital Automation is the key technology that is transforming industrial society. Big Data, Industry 4.0, the Internet of Things – these are all part of it, and as agents of change are as profound as the steam engine was to the First Industrial Revolution. The advent of mass production, and then of electrical power, are said to have been the second and third revolutions; the Fourth Industrial Revolution, the digital one, is now squarely and fully upon us. We are in the middle of it – not at the start – and it is affecting the hoist industry as much as any other.
So, are all manufacturers in the sector embracing it, or are they planning to? And what of their customers? Are they demanding the latest in digital automation from their overhead lifting, to render their own production plants part of the revolution?
And, of course, it may be that artificial intelligence, AI, will complete that revolution and take it to places that as yet we cannot foresee. Here we stand on the brink of the truly unknown.
We asked three different manufacturers, from different parts of the sector, for their views. Ace World Companies supplies the industry with overhead cranes, electric wire rope hoists, and end trucks both standard and custom, developed using the most sophisticated technologies available today. Its products range from 5.0 to 500 tons capacity. Aaron Kureck, the company’s VP Tronics, answered our questions. Caldwell, of course, is a major specialists in below-the-hook attachments and vacuum lifters, and Dan Mongan, its senior sales engineer, answered on behalf of the company. Conductix- Wampfler, a leading supplier of intelligent energy supply and data management systems for moving machinery, is represented by Brian Cook, the company’s senior product manager. Here are the answers they gave to our questions…
Overhead Crane and Hoist [OCH]: How much has digital automation penetrated your industry? Is it limited to higher-capacity hoists or is it throughout all overhead lifting in manufacturing processes?
Aaron Kureck (Ace World Companies): It’s penetrated our market quite a bit, actually. There is definitely a trend for more feature-rich ‘smart’ products that help end-users and owners save time and money. I would not say it’s limited by capacity of the hoist, but more by duty cycle and up-time necessity of the equipment.
Brian Cook (Conductix-Wamplfer): Within the crane sector, digital automation is mainly focused on the high-capacity cranes. The reason for this is that these types of cranes are manufactured to complete the same lift over and over again, so it’s easier to automate equipment for consistent processes.
Facility managers are still looking to add digital automation into smaller or less frequent-use crane operations, but it’s more difficult to automate equipment that is used to perform different types of crane lifts while also training your personnel to operate cranes for these different lifts.
Dan Mongan (Caldwell): It seems to be more and more prevalent as technology advances; we’re doing more now than we did 20 years ago. Of course, we’re in a sector that, despite technology, deals with the ever-presence of gravity and loads that ‘want’ to fall to ground. That hasn’t changed, and never will.
OCH: Do some clients still ask for manually controlled, non-automatic overhead hoists? Do you still manufacture and supply them?
AK: Yes: customers ask, and we supply. We provide digital and solid-state control systems for manually operated cranes and hoists that can easily be retrofitted and interfaced with automation technology down the road.
BC: At Conductix-Wampfler, we do not manufacture overhead cranes. However, we are seeing that the majority of our customers in this market are still asking for manually controlled cranes and hoists.
OCH: What proportion of customers ask for anti-sway, vertical lift, no-go lifting regions and so on – these being some of the benefits of automation?
AK: I would say approximately 10% of inquiries are asking for those type of features.
BC: The proportion of customers asking for various features of digital automation for crane operations depends on where they draw the line for automation. Automation in the form of collision avoidance – limiting the likelihood of two cranes running into each other – has very high market penetration. Roughly 50-75% of customers are asking for this type of automation because it is an easy feature to add, which ensures safety for the equipment and operators. We offer our customers collision avoidance in the form of our BridgeGuard system.
Overload condition is another automation feature that has highly penetrated the market. This feature includes a load cell that will prevent an operator from trying to lift something that is unsafe.
When it comes to anti-sway and no-go lifting, these types of automation features are not as common. Only roughly 10% of customers are asking for them. Digital automation is a large spectrum, but currently, most customers are looking to add the most basic features to modernise their crane operations.
DM: Generally, Caldwell does often provide lifting equipment that integrates with automated crane systems – sensors, encoders, lights, etc. – that tell the crane what’s going on. We don’t necessarily automate ourselves per se.
OCH: What control systems are most common: pedant, remote, fully automated (as in a process gantry overhead crane that can, for instance, feed waste into an incinerator at a waste-toenergy plant without human intervention)?
AK: Radio remote controls are the most common, with pendant back-ups. For semi- and fully automatic cranes, radio remote systems are generally supplied as a back-up/manual operation.
BC: In general, pendant and radio remotes are the most common crane control systems in the space. Traditionally, overhead cranes came with pendant controls, but in the past 20 years, radio remote systems have grown exponentially.
Until the past couple of years, it was common for facilities to use radios to control the cranes while also having a pendant solution as a back-up. Now, as a cost-saving measure, our customers are moving away from the back-up pendant option. We’re seeing this trend… because modern radios, like our Airmark or Jay Advanced lines, are very reliable, and the receivers rarely fail. Especially with products like our Airmark radio that can be paired to any crane in under one minute, it doesn’t make much sense to buy a pendant as a back-up anymore.
DM: More frequently, we’re providing radio remote control systems for our lifting devices. We’ve even had customers provide them that we’ve wired into systems. More typically, we work with a thirdparty supplier.
OCH: Are variable frequency drives now standard, as part of digital control? Are they now the default drive on electric machines?
AK: Yes, we have standardised on variable frequency drive/digital control.
BC: Almost all customers get variable frequency drives by default when purchasing a new crane. We’re even seeing variable frequency drives added to older cranes for modernisation.
DM: They’re not standard for us, but in many cases, we are utilising them.
OCH: Digital automation technology progresses far more quickly than the steel components of track and trolley, which resist obsolescence for far longer. Is retrofitting therefore an economical option for many? Is retrofitting still a major activity, and in demand?
AK: Yes, modernisation of control systems is still a major activity in the market.
BC: Retrofitting existing cranes is not the most seamless process, given that the life of a crane is so long. A crane might last 25 years, and think of how much technology has changed and can change in that time frame. Within the crane space, customers do routinely retrofit their cranes to add a few key digital automation safety features, such as collision avoidance or no-fly zones, but when it comes to full automation retrofitting, that process is much harder and a larger investment.
Taking the time to invest in digital automation up front when purchasing a new crane is best. But, if a customer is looking to retrofit their existing cranes, data communication is key. Once customers begin adding sensors as a part of the retrofit process, the next step is to figure out how to get that data from one point to the next. Conductix’s Nexus BB data-over-power solution allows facilities to utilise their existing infrastructure to create the critical data pathway for automation.
OCH: What benefits does automation bring? Safety? Efficiency? Speed? Improved positional accuracy in placing loads? Reduction in labour costs? Profitability? Warehouse accounting/management?
AK: All of the above. In addition, it provides data, logs, diagnostics, maintenance reminders, etc.
BC: The benefits of automation, particularly in radio remote control systems, are hard to deny. When looking at our radio remote offerings, our Airmark solution helps solve existing pain points such as the obsolescence of older equipment, workplace turnover and training, downtime, and inefficiency while increasing safety and improving ergonomics. Safety is the most important benefit of automation features like a radio remote control because it affects both personnel and equipment.
Radio remote controls provide operators with greater freedom of movement, enabling them to control cranes from a safe distance. This improves visibility and accuracy, reducing the risk of collisions or accidents during complex lifting operations. Some modern solutions, like Airmark, also have tandem crane control, which makes it possible to control two cranes from one device.
DM: All of these things, yes.
OCH: How many use it as part of full Industry 4.0? In other words, how many integrate their hoist automation into the automation of the plant as a whole, gathering data, using it for predictive maintenance and to optimise performance, efficiency, and so on. Is this limited to only the largest and most forwardlooking companies? Do you anticipate a use for artificial intelligence in future here?
AK: A growing number of users are asking for Industry 4.0 compatibility and integrating cranes and hoists into the plant systems. It does appear as though companies that are more on the cutting edge of technology are the ones asking for these types of ‘connected’ features. I do believe some forms of AI [artificial intelligence] is already in use in material handling – it just hasn’t previously been defined as such.
BC: We’ve not seen a lot of cust omers integrating crane automation into their full Industry 4.0 processes quite yet. In terms of AI, we’ve also not seen as much penetration in the mark et as facilities would need a hard dataset to train the technology, but it is most likely coming soon.
OCH: Is automation now so cheap, compared to the overall cost of a hoist, that it is almost a default decision to include it?
AK: No, not in all cases. It does increase the cost substantially, especially for custom systems that can require large amounts of engineering and coordination with other systems.
BC: At the base level, automation is cheap and easy to implement, and we’re seeing customers increasingly embrace these features, like collision avoidance and load cell. Additionally, future-proofing your crane operations is an affordable way to modernise your system. An example of this would be adding a data communication link like Nexus BB to your crane operations to ensure that you have a way to communicate between these base-level automation sensors once they’re added.
DM: Really this is a decision for the end user, or our channel partner would decide and inform us.
OCH: It has been said that the challenge in digital automation is not so much the technology, it is getting companies to make the adoption leap, to have management curiosity and try it in their factories, and that this is particularly a hurdle for SMEs. Do you agree? Are more or most managers now understanding the need to invest in this?
AK: I would say it’s around 50/50.
BC: Managers are more understanding of the need to invest in automation if they operate within a manufacturing facility that utilises higher-capacity cranes on a daily basis for the same processes. For a manufacturing process or facility that only uses an overhead crane for certain tasks, managers might not know how much value a crane can add, making them less likely to invest in these automation features.
It's important for facilities to partner with a vendor who understands what their cranes are being used for and how they are integrated into the facility’s processes in order to guide them toward the right equipment or automation upgrades. At Conductix, we provide controls, data and power, which are the three things you need to keep your business moving. We pride ourselves on being a vendor that takes the time to understand our customers’ needs to lead them to the right solution for their facility.
OCH: Are Insurance companies mandating it (as giving increased worker safety)? Is that a driver for installing automation? And is labour scarcity a factor? Did the Covid pandemic concentrate minds towards introducing such changes?
BC: We’ve currently not seen a lot of insurance companies mandating automation yet.
Labour scarcity is the number one thing we see as a driver for automation in this space. There is such high turnover within the crane operations sector, which makes it more important than ever to ensure that operators who are currently working in a facility are confident users. Automation is a strategic way to increase operator confidence, safety and efficiency.