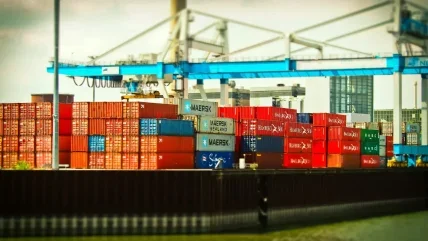
CM Labs, developer of Vortex Studio simulator training, builds technology that help clients design advanced equipment and prepare for skilled operations in both ports and construction markets globally.
DLM: WHAT ARE THE TOP DANGERS OF WORKING DOCKSIDE IN THE PORTS INDUSTRY?
Devon van de Kletersteeg: A port terminal, dock or ship presents many possible dangerous scenarios. Anytime there is a chance for interaction between humans and heavy machinery – including trucks, cranes and other cargo handling equipment, there is risk of trip hazards, materials falling, personal injury, and even death. Dock workers have been killed by suspended loads from cranes accidentally dropping, as well as loads of heavy materials unexpectedly releasing while being transported, moved and placed around the dock and quayside. Also, exposure to the outside elements and extreme weather, both heat and cold, can cause many critical health conditions, like heat stroke and hypothermia. There is also a chance of exposure to hazardous materials, including toxic compounds and chemicals.
Beyond the physical and material conditions, port workers’ lives are put at risk and they become exposed to hazardous conditions due to the shortage of skilled labour. Inexperienced workers getting placed on the job too early in their training because of the lack of staff can cause the wrong use of machinery and misunderstanding of safety rules and guidelines. New trainees wouldn’t be trained safely on out-of-procedure operations, or manage exceptional situations involving heavy or outsized loads and toxic materials. Promoting workers before they are truly ready to work safely, or are able to mentor and train their coworkers, happens when organisations cut corners in an effort to get the work done.
HOW CAN SIMULATION TRAINING MITIGATE THOSE DANGERS?
Simulation training allows port operators to identify potential hazards and risks in a safe and controlled environment first and then practice proper safety protocols and procedures before they encounter issues on the job. Workers become familiar with the specific controls, equipment and systems used in the port terminal, as well as the layout and environment of the dock. This can help identify and address potential problems or inefficiencies, and ensure that all staff are properly trained and prepared to handle different types of situations. Simulation training programmes can accelerate the learning curve for new hires, while increasing workers’ confidence and knowledge. This helps reduce the risk of accidents and injuries. Additionally, simulations can test new equipment or procedures without risking disruption or damage to the actual port machinery and operations.
WHAT ARE THE MOST POPULAR DOCKSIDE TRAINING PROGRAMMES CM LABS OFFERS?
CM Labs develops both quayside crane training and yard-side equipment training. Popular modules include Ship-to-Shore (STS) and Empty Container Handler. Customers also incorporate the Reach Stacker into their training to help manage the yard operations.
WHY IS SIMULATION TRAINING IMPORTANT TO DOCKSIDE MANAGERS?
Simulator training is an excellent tool for preliminary selection of potential operators. It involves minimal time and cost, and it is often possible to determine candidate potential within hours, as opposed to longer assessment periods through traditional approaches.
The traditional method of in-class and in-cab operator assessment and initial training can be both costly and tedious. The success rate is limited, with candidate qualification rates ranging from around 10% for complex cranes to 40% for equipment such as straddle carriers.
In a comparison of simulator training versus traditional training, the simulator approach is up to three times more effective. This is because trainees can spend more time on the simulator than on live equipment. Using the traditional method, if 25 to 30 candidates pass the live crane training, only 10 to 12 will eventually reach an acceptable productivity level, or 10% to 12% of all entry candidates. Using simulators, that number jumps to 25% to 30% of all entry candidates because evaluators can more efficiently assess operator capabilities on the simulator.