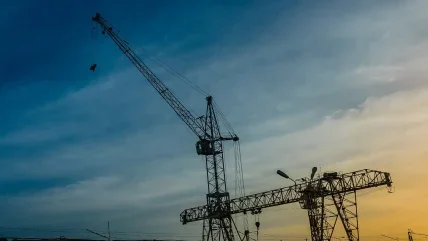
WHAT IS INDUSTRY 4.0?
Oscar Fillol: Industry 4.0 refers to the latest wave of technological advancements in the manufacturing sector. It involves the integration of digital technologies like the Internet of Things (IoT), artificial intelligence, and automation into the manufacturing processes.
Roland Najbar: In general terms, Industry 4.0 is a term coined to describe the next Industrial Revolution. In practicality, Industry 4.0 refers to datadriven, networked industrial technologies that aim to deliver advancements in industrial processes. Technologies that promote preventative maintenance, cybersecurity, cloud computing and digital twins [digital representations of a physical product, system or process] can be considered Industry 4.0.
WHAT DOES IT MEAN TO BE INDUSTRY 4.0-READY?
OF: Being Industry 4.0-ready means a company has embraced these technologies and is leveraging them to optimise their operations and improve efficiency.
RN: Being Industry 4.0-ready can depend on a number of variables, but in general to be Industry 4.0-ready one must have the correct hardware in place for automation, data collection and connectivity – for example, VFDs [variable frequency drives] and PLCs [programmable logic controllers], industrial PCs [IPCs] and a network for all of your devices to communicate. With the convergence of IT [information technology] and OT [operational technology] and interconnectivity of equipment, users must carefully consider cybersecurity. Having IT cybersecurity protection does not mean that you have OT cybersecurity protection – additional measures are required. Finally, one of the most important aspects of being Industry 4.0-ready is having the support structure in place for success, which means investing in the people that will use and maintain these new technologies.
THE TERM ‘INDUSTRY 4.0’ HAS BEEN AROUND A WHILE – DO YOU SEE MUCH EVIDENCE OF IT BEING USED WIDELY TODAY?
RN: Industry 4.0 has been one of the buzzwords in the industry that has been around for a while now, and we are finally seeing evidence of it being used today. In the field we’re seeing more and more users adapting Industry 4.0 technologies in their existing equipment. For example, adding networking to connect all of their equipment, which enables them to collect and analyse data for preventative maintenance. For greenfield developments we’re seeing an increased number of inquiries for equipment that will enable them to be Industry 4.0-ready, such as centralised servers, which will allow for less hardware on their cranes, or edge computing devices, which allow data to be processed right where it’s generated. The key is to be able to absorb the data-rich environment and derive efficiency gains in process improvements or business information to support decisions.
OF: Our eLink system is a prime example of how we assist our customers in adapting to Industry 4.0. Through the eLink system, we provide our customers with a tool that aligns with the principles of Industry 4.0. It enables them to connect their lifting equipment to the digital infrastructure, improve operational efficiency, and benefit from the advantages offered by automation and data-driven decisionmaking. The eLink system is a central data acquisition and control system, that enables our customers to control lifting hooks individually or in groups through a web application. It integrates seamlessly with existing infrastructure, allowing for efficient crane automation and enhanced safety and productivity.
WHY SHOULD CUSTOMERS EMBRACE INDUSTRY 4.0 AND BUY PRODUCTS THAT ARE INDUSTRY 4.0-READY?
OF: Customers should embrace Industry 4.0 because it offers a wide range of benefits. By adopting Industry 4.0 technologies customers can enhance productivity, improve safety and provide better service. The eLink system allows for centralised control and monitoring of lifting hooks, either individually or in groups, through a user-friendly web application. This technology enables real-time data acquisition, automation, and seamless integration with other systems, making operations more efficient and flexible.
RN: Industry 4.0 implemented correctly increases safety, improves productivity and becomes a powerful tool for operators, maintenance and management. Industry 4.0 starts with hardware, so ensuring that your equipment is specified with the latest technology is the right first step; newer hardware tends to be more flexible. For example, if a crane is specified with the latest VFDs and PLCs, IPCs and WiFi connectivity, you’re a majority of the way to being Industry 4.0-ready. Additional discrete sensors can always be added later to enhance the available data. At that point your crane is equipped with hardware and software to make it function as intended. A crane management system (CMS) capable of preventative maintenance is now available.
SO, IS IT A ‘MUST-HAVE’ TECHNOLOGY?
OF: While Industry 4.0 is not mandatory, it is highly advantageous for companies looking to stay competitive in the modern manufacturing landscape. Embracing Industry 4.0 technologies allows businesses to unlock new levels of efficiency, agility, and innovation. By adopting these technologies, companies can optimise their processes, respond swiftly to market changes, and gain a significant advantage over competitors.
RN: It depends on the criticality of the crane. The more critical to daily operation, the more it becomes a ‘must have’. Over time the crane market has seen major improvements in technology, going from contractors to VFDs, adding PLCs and Scada [supervisory control and data acquisition] systems, automating cranes – all of those advancements have been made to improve industrial processes and to improve the lives of those responsible for using and maintaining them.
HOW CAN SMALLER BUSINESSES IN PARTICULAR BENEFIT FROM INDUSTRY 4.0?
RN: Not every Industry 4.0 technology has to be a big step. Smaller business with less resources can implement Industry 4.0 in small steps. We take all of our software and hardware and modularise it, so you can pick-and-play your solution instead of buying a huge, expensive system. It’s important to look for solutions that are open, meaning you can take a Siemens solution and one from another vendor and plug them together. Flexibility is extremely important for smaller businesses. Smaller businesses with fewer employees can leverage technology to ease the workload of their employees. If employees are overworked, safety and productivity standards can begin to slip.
Utilising technologies that not only collects data, but also takes action from that data, is where you begin to see benefits. For example, with mechanical condition monitoring, which produces high-frequency data such as vibration or temperature readings, this data can quickly add up to massive quantities of digital data. Without the tools and strategies in place to analyse it, it’s useless. But because we have the smart analytics in place you will know when to replace your gearbox, motor, bearing etc. long before it fails. That’s the difference between data collection and actionable data.
OF: Smaller businesses can reap significant benefits from Industry 4.0. These technologies level the playing field by offering cost-effective solutions and enhanced operational capabilities. Industry 4.0 enables streamlined automation, efficient resource management, and improved decisionmaking based on real-time data insights. Smaller businesses can optimise their production processes, reduce downtime, improve product quality, and quickly adapt to changing market demands.
WHAT ARE THE ALTERNATIVES/ PROSPECTS FOR A COMPANY THAT CHOOSES NOT TO MOVE TO INDUSTRY 4.0?
RN: For companies not wanting to move to Industry 4.0, the best alternative is to buy extremely reliable equipment, and try to avoid single points of failure that could jeopardise your operation. Building in redundancy to critical areas such as sensors, VFDs, power supplies would be a good precaution. Maintain the equipment frequently and train as well as audit your operators and/or maintenance crew regularly.
OF: Companies that choose not to embrace Industry 4.0 technologies may face challenges in the long run. They might struggle to keep up with competitors who have embraced automation, leading to decreased efficiency and higher production costs. Additionally, without leveraging real-time data and advanced analytics, decision-making processes may become less informed, hindering the company’s ability to innovate and adapt to market changes.
CAN YOU GIVE AN EXAMPLE OF A CLIENT THAT IS USING INDUSTRY 4.0 AND DESCRIBE THE IMPACT IT HAS HAD ON THEIR BUSINESS?
RN: One of our customers, who was an early adopter of Industry 4.0, has maximised all of the available technologies to provide state-of-the-art automation solutions. This is a customer who constantly researches industryleading standards and technologies, performs R&D and successfully implements these solutions into the field. Currently, they utilise our hardware and software to provide complete crane automation, preventative maintenance Scada systems, centralised maintenance and remote control crane operations. Their business has grown substantially, and they remain the top choice in the industry. Their customers benefit from increased production, improved safety and equipment that is easier to maintain. Another benefit is that this equipment is future-proof because it is based on modular and open hardware and software.
WHAT IS YOUR COMPANY DOING TO DELIVER INDUSTRY 4.0?
RN: Siemens is providing end-to-end Industry 4.0 technologies, everything from hardware to software and everything in between. From a hardware side we provide a full range of reliable and flexible automation components, power components, WiFi components and industry-specific components such as crane management systems, mechanical condition monitoring, sway control solutions and many more. We then complement our hardware with our software such as predictive analysis tools, digital twinning, fully integrated automation suites, and are now even beginning to implement AI. With powerful tools such as digital twins, customers can simulate their drive and PLC software, meaning it can be tested without having the actual hardware. You can develop your code, test it, and even begin training your maintenance team long before production begins. You can even integrate your software simulation with 3D physics-based models, which model your equipment or even entire plant. Industry 4.0 has been around for a long time, but we are now finally seeing widespread use of its advantages.
OF: We leverage the Internet of Things and advanced sensor technologies in our products. The eLink system utilises hook sensors to provide real-time data insights, enabling our customers to make informed decisions, improve operational efficiency, and enhance safety measures.
We emphasise connectivity and data exchange capabilities in our solutions. By enabling our customers to connect their lifting equipment to the digital ecosystem, we facilitate the exchange of data between different systems, optimising processes and enabling datadriven decision-making.
We prioritise user-friendly interfaces in our products, ensuring that our customers can easily navigate and control the eLink system. This simplifies the adoption of Industry 4.0 technologies, allowing businesses of all sizes to benefit from automation and digitalisation.
We actively collaborate with industry partners, technology providers, and customers to stay at the forefront of Industry 4.0. By working together, we exchange knowledge, leverage expertise, and collectively drive innovation in the manufacturing sector.
Through these initiatives, Elebia is actively delivering Industry 4.0 solutions to our customers. We aim to empower businesses with the tools and technologies necessary to optimise their operations, enhance productivity, improve safety, and embrace the transformative potential of Industry 4.0.