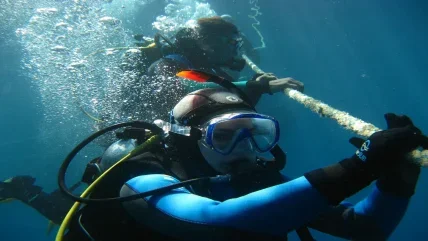
Braaten.technology, a start-up company from Norway, has developed an underwater load cell designed to handle lifting operations at sea.
The company argues that accurate weight control underwater has been a constant challenge, mainly due to variable hydrostatic pressure, but that with its SLM (Subsea Load Monitor) it is possible to monitor loads independent of depth and pressure.
It goes on to add that the product could be the key to a more sustainable future for this sector.
How? The company says that traditional underwater lifting operations rely on surface vessels, and that these vessels account for a significant proportion of CO2 emissions in the offshore sector. With SLM, the need for such vessels providing lift wire from the surface can be reduced by using air lift bags, or buoyancy balloons, with the SLM installed between the load and the buoyancy balloons.
The product came into being when Martin Johansen, Braaten.technology’s chief technology officer, and Torbjørn Espeland, engineering manager, were looking for a solution aimed at enhancing aquaculture mooring systems. However, a conversation with Trygve Aleksander Aardal, CEO, and an expert in North Sea lifting operations, unveiled an industry gap: the lack of precise weight monitoring in subsea lifting. Aardal and Johansen, talking about a harrowing experience with buoyancy balloons and remote operated vehicles (ROVs) operating on guesswork, highlighted the need for a solution, which sparked the development of the SLM.
That journey began in 2016, with the idea taking shape over years of development. Officially, Braaten. technology was established in 2021.
Since then, several customers have come onboard, with, says Aardal, the likes of IKM Subsea – an ROV and subsea operator – energy company Equinor, oil and gas firm ConocoPhillips, subea services provider DeepOcean, and OceanInstaller, which delivers subsea projects, standing out. “They’ve integrated the SLM for safer, more controlled lifting, significantly enhancing operational safety and efficiency,” he says.
According to Aardal, the product provides real-time, precise weight monitoring. “Equipped with state-ofthe- art acoustic communication, it can receive signals from up to 100 weight cells… enabling complex remote subsea operations, such as lifting with buoyancy [aids] when the weather at the ocean surface won’t allow you to.”
The company says the product can work at any depth – one version for the Norwegian continental shelf has a working depth of 500m, while another currently being developed will be able to operate at 6,000m; it has a working load limit (depending on the lifting lugs) that is also variable – Braaten.technology is in the midst of producing 32t model; plus, it is able to operate for up to 500 hours.
Rival products include alternatives such as subsea load shackles. “However,” says Aardal, “they lack the comprehensive capabilities of the SLM.
“The SLM shines with its unparalleled acoustic communication technology, simultaneous monitoring capacity, extended battery life, and robust data storage. These features elevate it beyond the current industry offerings.”
Looking forward, Braaten.technology has set out its sales targets, with Aardal saying it aims to achieve a milestone of $10m in sales in the North Sea. “Beyond that, our eyes are set on the Gulf of Mexico, a strategic and promising market for our technology,” he says.