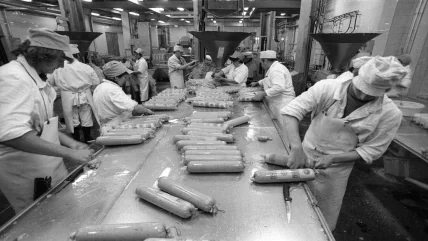
High levels of vapor; coatings of grease, oil and food residue; and the need for frequent caustic wash-downs were corroding the monorail and eating away at the powder coat on the aluminium castings of the 1 USt hoist.
Shupper-Brickle Equipment Company, Dayton, New Jersey, replaced the monorail with a stainless steel monorail and replaced the hoist, and a 2 USt hoist over the soup line, with something unique. They took apart two standard Columbus McKinnon Lodestar hoists and separately treated each part with electroless nickel plating, “so we got beautiful equipment with all stainless steel hardware,” says Shupper-Brickle president Andrew Litecky.

Gorbel’s Pivot Pro articulating jib crane.
“Electroless nickel plating enhances the wear capability and corrosion resistance with a nickel-phosphorus bi-metal coating,” he says. “It gives a more uniform surface coating than electroplating, and also the phosphorus improves the crystalline structure over plain nickel plating. The results are improved wearability, ductility, strength compression and lubricity of one part against another. And flaking is not an issue.
“About a year after they were put in, I went back and they were perfect. They see steam and hot grease all day and were just like brand new.”
A lot of food processing equipment, from conveyors and cutters to blanchers and bean snippers, is designed specifically for that industry. Hoists and monorails and jib cranes and overhead cranes are applied in countless industries, however, and the food handling industry is for most manufacturers and distributors a small fraction of their total business.
Still, custom tailoring cranes and hoists for the food processing industry—where the working conditions are tough on equipment, there is decreasing tolerance for the possibility of contamination by peeling flaking or flaking coatings, and ergonomics are getting a lot more attention—is becoming more common. And, beyond custom-built equipment, crane and hoist suppliers are introducing more new products and product lines specifically for that industry.
In October, for example, The David Round Company, Solon, Ohio, introduced such a product line with stainless steel jib cranes, floor cranes, chain hoists, wire rope hoists and strap hoists completely unpainted.
“From the engineering firms I work with, when pharmaceutical industry specs come in, it‘s often a 100% requirement that it be all stainless steel,” says Matt Downing, sales manager for David Round & Son, Inc. “In food, it’s more hybrid, where the hook, chain and trolley wheels might be stainless but the rest of the hoist doesn’t have to be. However, the who’s who I sell to in food, the big boys in the food product industry who are asking for bids on stainless, they are telling me that’s the way the industry is going, to all stainless.”
David Round had been building stainless steel products for the past seven to eight years and “we’ve made a commitment to the food and pharmaceutical market to offer all of our products in stainless steel,” Downing says.
Right now might be a good time to make such a commitment because food handling is among the few industries that have remained healthy while others have sagged along with the overall economy.
“Food and beverages purchased for off-premises consumption,” basically the stuff we buy at the grocery store rather than paying for in restaurants, made up a respectable USD786.3 billion portion of the nation’s gross domestic product in the second quarter of 2009, according to the US Department of Commerce. That was exactly the same as the USD786.3 billion produced in the second quarter of 2008, while the nation’s total gross domestic product declined by USD346.6 billion, or 2.4%, over the same period.

Ingersoll Rand ergonomic handling system in a Pennsylvania cheese processing plant uses handlebar controls to clamp a block of cheese, lift it and transport it. The rail system is a ceiling-mounted, ZRA2 profile workstation crane. The balancer is a tandem reeved “BW” series balancer, and the stainless steel clamp on the cheese is the custom handling device.
“It doesn’t tend to have the same cyclical nature that general industry does,” says Brad Jarnagin, director of global market development for Columbus McKinnon Corporation.
“People out here gotta eat,” says Paul Otto, owner of Otto Systems, a Santa Fe, California, distributor of material handling systems such as hoists, cranes and monorails, and Columbus McKinnon master parts depot and distributor for the western region. “Anything having to do with the food industry is still producing work.”
That would also include non-food products tied to the food industry by being sold in supermarkets, things such as hair care products and vitamins, where Otto Systems lifting products are used in mixing processes, he says.
“Right now, locally, the breweries—Bud, Coors, Miller—they all have projects going and we are selling into those facilities,” where cranes may be used to handle tanks or pick lids off vats, says Otto. “The other area is the bakeries; these facilities operate 24/7 and need to handle tons of dough,” Otto says.
A regional bakery used to have a guy with a shovel moving dough into the mixing vats. Otto Systems, in a joint project with fabricators Trademark Hoist & Crane, Pomona, California, put in a system to pick up the big totes containing some 3,000 pounds of dough each and dump them directly into the mixers.
David Round’s line of stainless steel material handling equipment for the food processing industry, announced in October, includes jib cranes, floor cranes, chain hoists, wire rope hoists and strap hoists.
“We designed a twin hook dough handling system which has proven to be very efficient when it comes to handling cookie dough,” Otto says. “This twin hook system allows one operation to lift, move and tilt totes filled with dough. We have two bakeries which now have 10 or 12 of these systems working around the clock with little or no down time.
“Chain hoists are also widely used in clean room applications which require non-plated load chain and hooks, gaskets in between all the covers and centre cases, plus, paint must be removed wherever you have metal-on-metal contact.”
The typical food processing application is for lower capacity electric chain hoists in a fixed position or hook mounted to a push trolley on a jib crane, according to Jarnagin. They tend to be short lifts where speed is not critical. Since there is no specific FDA standard governing food grade hoists, the requirements tend to vary from application to application. The most common options for food grade use are stainless steel chain, stainless steel lower block and hook, food grade lubrication, FDA white powder coat paint and special enclosures to handle washdown environments.
Most food handling applications, unlike typical industrial operations that have multiple hoist requirements, are smaller orders, says Jarnagin. “It’s typically a production process where conveyor systems are doing most of the work and in a single location you need a hoist to lift a hopper or bag. You don’t typically get inquiries on food grade hoists for 30 to 40 hoists at a time.”
Pharmaceutical plants are more of an industrial production situation and have more lifting applications than food processing, and pharmaceuticals have more hoists larger than the two-ton-on-down range of capacities used in food. However, the two industries are similar in their need for cleanliness in overhead lifting. “People generally use the terms ‘food grade’ and ‘clean room’ almost interchangeably, Jarnagin says, “which is not accurate. There are specific standards required for clean room applications.”

Columbus McKinnon supplies a wide range of hoist and rigging products to the food industry. “We have a reputation for providing engineered hoists to solve customers’ problems and cater to special applications like food handling and clean rooms,” Jarnagin says. Significant in food processing is not just that products need to be “food grade,” but ergonomics are being driven to levels not seen before in the food handling industry.
“In general,” says Jeff Baker, global category manager for ergonomic handling products with Ingersoll Rand Company, “you’re seeing these industries starting to follow the way of high-volume manufacturing, looking at tools and processes being used in motor vehicles and aerospace and saying, they can learn something from this.”
One Pennsylvania cheese factory used to move huge blocks of cheese on pallets carried by forklifts, with log jams at the doorways. Keeping the cheese wrapped in the process, the forklifts lifted the blocks onto the shredder line.
Now the process is cleaner and more efficient, Baker says, with an Ingersoll Rand lift-assist device.
EMH AL Systems aluminium cranes rail system, rail and free standing structure during installation in a cheese processing facility, with equipment normally in the room temporarily removed. Lifting tools demonstrated on wood block simulating cheese.
Using clamps to lift a 640-pound block of cheese, the system moves it along beneath an aluminium rail and places it on a conveyor belt that transports it for shredding. The employee operates the system using handlebars with controls, on the left a clamp/unclamp button and on the right an up and down button to help raise and lower the load. Thanks to a tandem balancer on the rail overhead, the employee is lifting only an effective load of just five or six pounds, while the actual load is 640 pounds.
“He never has to reach or stretch,” Baker says. “The balancers run on smooth track inside that monorail so there’s very little rolling resistance, and he can do that all day every day five days a week without getting tired,” Baker says.
The majority of overhead material handling in the food processing industry, he says, copes with weights below a couple of hundred pounds, where most companies are trying to find ways to allow an operator to pick that much up without having back injuries or other manual lifting injuries.
“Anywhere manual lifting is involved, you’re seeing companies trying to find ways to make it easier on their operators, keep people healthy, fatigue-free, productive.”
Every style of crane is used in food processing, according to Downing – overhead, jib, gantry – and the Ruger Industries’ (owned by David Round & Sons) portable hydraulic floor cranes available in stainless steel.
“It’s real nice when you go into the maintenance area in a dairy, for example, where you’re only lifting 500 to 1,000 pounds, just more than one person’s going to lift.”
Among David Round’s products most popular for food processing facilities are its stainless steel chain hoists, wire rope hoists and strap hoists, the chain hoist being most cost effective but the stainless steel strap hoist being most popular because one does not have to lubricate a chain.
“Everything is totally captured and enclosed in a stainless steel gearbox, so there’s nothing that can potentially drip into the product,” says Downing. “With a poly-nylon strap that’s acceptable in food and pharmaceutical applications, you don’t lubricate, just replace.”
EMH Inc., Valley City, Ohio, with dealer Handling Concepts of Akron, Ohio, used the David Round stainless steel strap hoist with lifting tools manufactured by AirOlift Lifting Systems, Palmerton, Pennsylvania, supported by EMH’s own AL Systems aluminium enclosed rail in such food applications as cheese factories in Ohio and Utah.
Workstation cranes
EMH introduced the AL workstation crane systems less than two years ago, says regional sales manager James Kehres. “A dealer was having issues with other rail they had, an epoxy-coated product where the coating wasn’t holding up. A lot of other people who make aluminum rail either paint it or leave it bare, and with the wash-down situations in these places it has a hard time standing up to the environment. Our aluminium rail is anodised, and used with the stainless steel parts it could weather the environment.”
EMH has large overhead cranes as well as workstation cranes. Applying its products in everything from general fabrication facilities to injection mold facilities and steel processors, EMH provides a large range of solutions, Kehres says, to customer bases in the power generation and concrete industries.
Food processing, however, is a niche to which the company is paying more attention, having recently standardised all the stainless steel components in its workstation cranes.
Overhead lifting is less a factor in the bottling portion of the industry, says Otto. “All your beverages, your sodas, your Pepsi Colas and Coca Colas, rely more on floor conveyors.”
Food packaging and distribution in general take a backseat to food processing for overhead lifting applications. Crane and hoist applications in these links of the food handling chain are most likely in maintenance activities such as removing motors out of machines or batteries out of fork lifts. These systems are considered light duty for occasional use but nonetheless are required to maintain a safe working environment, Otto says.
Still, packaging and distribution operations have their own unique lifting requirements. Gorbel’s Pivot Pro, for example, introduced in 2008, is an articulating jib crane aimed at capacities up to 150 pounds.
“The Pivot Pro was designed specifically to target food and beverage,” says Kevin Duhamel, workstation and jib crane product manager for Gorbel. “It uses vacuum tube lifters a lot because of the flexibility they have. We designed that crane to solve two problems. One, to eliminate hose hanging from the bottom of the crane, which makes it much cleaner, easier to move around. Also, it allows a user to move much more quickly than with a typical jib crane for things like palletising and de-palletising, because of the articulating arm. Essentially, you’re only moving half the arm at a time. Those distribution areas where you have boxes and bags are a great place for Pivot Pro.”
Pivot Pro’s dexterity is especially useful in custom palletising, Duhamel says, where an operator might want to put different boxes on the same pallet.
Or Gorbel’s free-standing easy arm intelligent lifting device jib, more than six feet high with spans up to 14 feet. One brewery, for example, uses it to lift micro-kegs when they are filled and ready to ship.
Still, when it comes to shipping and distribution, as one industry spokesman puts it, “A box of mozzarella is no different than a box of bearings.”
Gorbel, like other crane and hoist producers, also applies many of its products in the processing end of the food chain, with work stations the number one product applied, followed shortly by jib cranes.
“We’re very interested in the food industry,” says Duhamel, “as it seems to be still thriving. One theory is that people are eating out less and eating in more, spending money not outside the home but in the home, where most of these products are sold. And that food and beverage are not hit as badly, because people can’t do without them.”