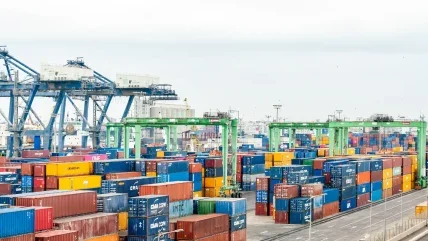
Ports everywhere are under strain. The ever-larger container ships being built need ever deeperdraught ports and ever larger cranes to unload them. Expansions are being undertaken, but with supply chains around the world also under massive pressure, congestion shore-side, in the stacking yards, is endemic – and getting stacked containers onto the right truck at the right time and in the right order is a major logistical problem, or, to be more accurate, a potential logistical nightmare. If the container you need is at the bottom of a stack of six, how exactly do you extricate it – or do you tell the truck driver who wants to deliver it onwards just to wait a few more hours or days till the ones above it have cleared?
This is the fundamental problem of container terminal operation, and to solve it, ports worldwide have not only been enlarging their cranes and deepening their approaches, they have also been introducing automation, remote control and autonomous, self-driving vehicles and the like and trying to exploit every efficiency gain that digital technology can give them. Siemens, for instance, has been in the forefront of developing AI for container port operations: in our explainer ‘Alois Recktenwald explains AI’, the company’s AI expert, Alois Recktenwald, explains the approaches, where they are best suited, and the areas where what we may now call traditional digital solutions remain preferable.
Scandinavia can provide an illustration of all the above. When Hutchison Ports Stockholm established its new container terminal to the south of the Swedish capital at Norvik it chose a site with a natural deep-water draught. The company installed two of the world’s biggest quay cranes and equipped them with automation and remote operation. ABB supplied the technology. In the container world loading and discharge processes are pretty much identical worldwide regardless of terminal size, but smaller terminals like Norvik generally require more operational flexibility given the many different sizes of vessels they accommodate. The quay cranes here serve vessels ranging from small barges up to ships 22 containers wide.
As container ships have become bigger so have the ship-to-shore (STS) cranes. Economies of scale bring benefits, but a drawback is that the human eye is limited and on cranes this big the physical distance between the cabin and the ship’s hold is too great for the operator to clearly see his target.
Hence the large number of cameras on the cranes. “The biggest difference is the cameras, and the angles of view that they give. They zoom in on the container and we can see big angles all around the ship, and the screens show us everything we need to see around the quay crane. It helps me as a driver to do the work more efficiently as well as more safely,” says Linus Gellborn, a crane operator at Norvik. He does not operate from a cab on the crane, but from a central room, looking at screens; he not only has a better view but has more comfort as well.
The cab on the gantry crane is becoming a thing of the past. For further evidence consider the Eurogate Container Terminal in Wilhelmshaven, Germany. In February this year the port ordered two Liebherr dual trolley shipto- shore container cranes. These will be the first double trolley container cranes at the terminal and can handle the world’s largest container vessels. Wilhelmshaven is, in fact, Germany’s only deep-water port able to allow ultra-large container vessel access at all tides, and it is gearing up for significant growth and modernising into a fully automated terminal. These cranes are therefore significant for the German economy.
Each has a lift height of 54.5m and a forward reach of 73m. The span between legs is 30.48m and they have an operational back reach, with the secondary trolley, of 26m. One thing they do not have is anywhere for a human being to sit: they are not being equipped with an operator’s cab.
Instead, Liebherr’s Remote Operator Stations (ROS) system is installed. Operators work at a distance, in a spacious office complex, via video screens, and much of the handling is automatic.
The cranes are designed for tandem operation. The primary trolley delivers containers automatically to the pinning platform. There the containers rest on frames while the twist locks are removed. This is done by hand – it is the only manual part of the process. Once the pinning personnel leave the platform, they activate the secondary trolley, which automatically delivers the container to the landside automated guided vehicles (AGVs).
Rubber-tyred gantry cranes (RTGs) are also part of the automation process. As an example, in Portugal, PSA Sines, the local subsidiary of PSA International, has ordered six electric-powered automated rubber-tyred gantry (aRTG) cranes from Konecranes. It is the port’s first venture into aRTG systems. They will be fully automated, and will have the capability to stack up to five containers, instead of only three with the current straddle carriers. Truck handling and exceptions will be managed via an ROS. Man-machine interaction will be minimised.
The aim is to improve efficiency, predictability and safety as well as support the terminal’s expansion plans. When its new phase is complete the terminal will almost double its annual handling capacity from 2.3 to 4.1 million twentyfoot equivalent unit (TEU) containers. The cranes will be delivered in Q1 2024.
Eco-friendliness is another major current theme in port and container handling. Central to it is the flight from diesel. Thus port crane specialist Macgregor, part of Cargotec, in December introduced its fully electrically driven heavy-duty transloading crane, the TCE. The crane finally closes the gap in MacGregor’s electric crane portfolio: the company can now offer electric port cranes up to 50t safe working load (SWL).
Transloading cranes like these are usually used for heavy-duty work in areas with draught restrictions or limited infrastructure and typically run 24/7 to provide the most efficient handling of bulk material. By electrifying the drive, and using it in combination with an energy storage system to get the maximum benefit from power that is regenerated during the lowering of loads, the crane is said to consume approximately 60% less energy than a hydraulic equivalent. CO2 emissions will be reduced by more than 5,500t within a typical lifecycle of a crane. Macgregor say that the electric drive also increases the turnover capacity performance by more than 10% because of the higher speeds. With no need to change oil, filters and hoses there are also potential savings in capital expenditure and maintenance costs.
Two such cranes were part of an order placed with Macgregor in December for a total of ten floating crane barges to be built by PT Karya Teknik Utama at its shipyard in Indonesia. The cranes are designed for 1,800,000 load cycles. The two TCE electric transloading cranes will be the first to be produced and delivered to the customer. Delivery is scheduled from the second quarter of 2023 to the third quarter of 2024.
Alois Recktenwald explains AI
Alois Recktenwald is cranes expert (solutions) at Siemens, and is its leading expert on artificial intelligence. He spoke to Hoist magazine about the hype and the realities of AI in container terminals.
Is artificial intelligence being used in dockyards now?
Not yet. In my view it will it still take years to get there. And we have to distinguish what we [want] to achieve with AI.
AI essentially ‘learns’ by observing and copying. If a good mathematical algorithm exists for doing a task, then you don’t need AI – you can just use ordinary software to programme your computer. And if that works well, why use AI?
So I think you really have to look at where you are applying AI, and what you are applying it to. If a task involves a problem that is not clear for a human to recognise directly, there AI can give an advantage. It can be faster and better to use in such situations. So if for a human it is too difficult, and for a programmer the relations are not linear and there is no classical mathematical algorithm available, in that case AI comes into its own.
When we apply AI in the crane environment we are really looking at the areas where we have a certain complexity; there, AI could optimise the systems, [give] them better performance. AI does not stand alone; it is more an additional accelerator to make the quality and the automation better.
For AI to operate a crane, it needs to ‘see’ what it is doing. For visual recognition – to identify, say, the corners of the container that it needs to lift, or an obstacle that is in the way – they need vision sensors such as cameras to sense outlines and lasers to tell distance. Are such sensors now adequate for the job?
Yes, they are adequate – as long as there are no people around. There is a limitation on the safety-certified sensors that you would need. Generally, we would need to be certain of safely detecting people in area where autonomous machines are working – and at present you will not find much in the area of outdoor safety-certified sensors for that purpose. There is no safety-certified camera or vision system available. If tomorrow such a sensor came along it would be a game-changer, and whoever invented it would be in
big business.
Some automation is clearly already there in the dockyard environment. And where people are not in interaction with the cranes, then a high degree of automation is possible. For example, in container terminals the container stacks are usually automated. You need no artificial intelligence for that, just normal programming: you have information about which containers are to be collected first, how much they weigh, when will they be picked up, and so on. So you can stack them in a sensible order in a sensible way and you can work out that sensible way either in a human brain or with a computer programme. It is not too difficult and you do not need AI.
But you can introduce information about the traffic on the roads: a jam on a road to the north will delay some collections but drivers from the south will arrive on time. That would interfere with your usual management layout: there is now information which it is not easy for you to integrate because it is not clear what will happen. Weather conditions could be also part of it: there is snow on one road and not on another. And transport companies may be unreliable: there may be one company which says all the time that it will come on Monday but always turns up on the Tuesday.
And this is where AI can optimise your operation. It can learn all the time from observing the traffic, the weather, the individual logistical companies who bring your containers; and it can order your stacking to take account of all those mathematically impossible to compute unknowables. So this is the real beauty and use of AI: it is dealing with all the imponderables, the human frailties, the unexpected. It does not live in the pure, idealised, mathematical world. It deals with the complications of the real world instead.
Liebherr-Transform lift projects
A perhaps unexpected modification to STS cranes is the province of Liebherr’s upgrade, modification and overhaul service Liebherr-Transform. It has used a new patented jacking system to increase the height of a ship-to-shore container crane at Patrick Terminals in Brisbane, and is doing the same leg-lengthening task on four STS cranes at GCT terminal New York.
One of the key features of the jacking system is that it uses the end carriage of the crane as a solid base for jacking the crane structure, which eliminates the need for additional equipment. Using the crane’s own structure as the basis for jacking means that the loadings are low and are carried through the existing crane.
Preparation takes a couple of weeks and the system allows the crane to be jacked in its existing position or to be moved back from the rails for jacking if required. The actual crane raise and the insertion of the extensions can be completed in hours, which makes it suited to terminals prone to high winds. The whole process can be completed from as little as four weeks per crane.
Liebherr has two STS cranes at Brisbane Autostrad: a new STS currently being commissioned and an older one supplied in 2015. The 2015 crane has a supplied lift height of 37.5m, but with larger vessels calling at the port, a lift height extension was needed – the crane there was raised by 11.5m.
In New York, GCT New York LP operates four Liebherr STS container cranes that were supplied in 2004. The cranes have a lift height of 36.57m and an outreach of 50m. The Liebherr-Transform project will extend the lift height by 8.6m and the outreach by 5m. When complete, the cranes will be able to work the largest vessels currently calling at the port.