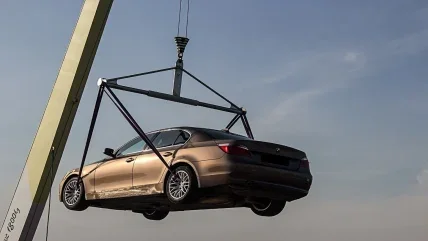
HOIST: WHAT TYPE OF CRANES DO YOU SUPPLY?
Juergen Gieske: They’re bridge cranes. There are two types of cranes we supply to the automotive industry in general. [Actually,] three types, but mostly two.
The coil crane – that’s the beginning of the process, where you get a coil of steel, like a toilet roll, if you will… that gets rolled out flat. They cut off some – that’s what’s called a blank – and it gets stamped… That blank goes into the press – boom, boom, boom, boom – comes out as a door.
And then we supply the die crane, [which handles the die] that makes the shape. We supply manual die handling cranes all the way up to fully automated.
In general, die handling cranes [are] manual, with people out there using slings and radios and walking around. Many people still do that today – we’re selling them today brand new.
Then there’s the [automated] die gripper crane. It’s massive – as big as a bedroom. We handle the die (the two halves of equipment that comes down together and presses the blank) when they are changed out. If [the car manufacturer] wants to make the right door of a particular model for the next two hours, there are maybe three to five dies in that [process]. Our cranes will move those dies into the bolster [from the warehouse] – we get into position over the die and these arms come in and they grip the connection points of the die, they lift it up, the crane moves it over to the bolsters, set it down, open the gripper. The bolster then slides into the press and they make the part. Then the bolster slides to the other side of the press, and we take those dies and we put them back into the warehouse, and those dies have to be stacked and stored in a sequential manner so they can be found later on… [and they] get moved routinely and regularly.
Those five dies it takes to make the right door… only make the right door. You don’t use them for any other part. We’ve got to know where they are and make sure that we can find them quickly and efficiently next time. So when we automate our warehouse management system… we are fully responsible for where those dies are located in a die field that could have several hundred dies [because], of course, [the car manufacturer] isn’t just making one car at a facility, they’re making many models, many different styles.
There are also the general maintenance cranes. But that’s not the sexy end of the business. Everybody’s got a maintenance crane… but the process-critical cranes are the coil crane and the die gripper/die handling crane. That’s going to shut the plant down if they’re not operating properly, if they’re not reliable, if they’re unsafe.
WHO BUYS YOUR CRANES?
We supply the manufacturers themselves, primarily the stamping plant. That’s where they make the fenders, the hoods, the doors, the trunk, whatever that might be.
That’s when that stamping takes place in-house. There are the tier one suppliers as well [companies that supply parts or systems directly to original equipment manufacturers]. So maybe an automotive facility doesn’t do in-house stamping, but subcontracts that to a tier one stamping facility – we’ll supply the stamping plant cranes for those.
HOW POPULAR ARE THE AUTOMATED SYSTEMS?
Not everybody is willing to invest in full automation for various reasons – it goes manufacturer by manufacturer. But we’re getting a lot more interest than we ever have. It’s almost contagious. We’re seeing people that say: “Hey, do you hear what they’re doing over at brand X stamping plant – they’ve got a fully automated crane.”
Suddenly, we start hearing: “Hey, we’d like to learn more about that.” It’s fomo (fear of missing out), and they want to understand the opportunity, they want to understand the cost, they want to understand what’s the upside, and that’s what we’re able to discuss with them. That’s the big trend we’re seeing right now: full automation in the press shop – the three to five dies bolster press.
WHAT WOULD YOU SAY ARE THE BENEFITS OF AUTOMATION?
When you take the human element out of die handling the number one reason to do it is safety. Any time you lift a 50-ton, 60-ton die and you do it manually with chains and slings at all four corners – now you get an operator that maybe isn’t quite… attentive enough, and they pick this 60-ton die, and it starts to swing, now that individual might be in harm’s way. And there are usually two individuals – one with the radio, one rigging it. There are two people potentially in harm’s way.
So the initiative for automating the die warehouse and supporting the press with these dies is to get people away from it.
Number two is it can speed things up. The industry is looking at faster die change-outs because in business and manufacturing inventory is the root of all evil. The more inventory you have, the more cost you’ve got sitting there doing nothing. The ideal scenario is to have the manufacturing set up so all the parts come together so that that car gets made [in one go]. But it’s impossible in this day and age – you have to make enough for some inventory. But… the less inventory, the better. So instead of making 200 right doors for whatever vehicle, [the manufacturers] want to make 20 doors because that’s 180 fewer doors they’ve got to have in inventory and there’s a cost associated with that.
Also… because there are no isle widths for people any more, I can take less real estate. I can stack much higher – instead of stacking two dies high, maybe three, we get to five dies high, so now the real estate required for this warehouse gets smaller.
WHERE ARE WE IN THE JOURNEY TOWARDS FULL AUTOMATION?
We have them in Asia, fully automated; Europe: fully automated. We’re fully automating cranes all over the world.
In North America, automating this application has only been considered in about the last five years. From an initial ‘let’s try this’ to actually implementing it has been the last five, probably four, years, so it’s very new to automate this application of die handling cranes in automotive.
In North America we have one fully automated, they’re just not using it that way.
The technology is there, but transitioning this much technology into this area of the facility takes some time. We’re at the stage where… they need to take the next step and let the crane do everything, but it can presently do it all. Because of the safety culture, they’re not quite turning on the switch to full auto. I’d say 90% of it is fully automated in the facility I’m talking about, but it could go lights out right now. ‘Lights out’ means no one’s involved, but they don’t want to do it because they’re still getting comfortable with the concept. This is within the last six months, so when I mention this technology, that’s how fresh it is.
WHAT GIVES YOU THE EDGE OVER YOUR COMPETITORS?
First of all, we have leading-edge safety technology, such as hook centring [to eliminate side pulling], target positioning [where the crane drives itself from one place to another], and protected areas… so loads don’t swing into obstructions such as buildings, machines, people, walkways.
There is also our support and service. We are where our customers are. We don’t have third-party contractors; we have direct employees that are intimate with our equipment, intimate with our technology.
We also have… Tru Connect, which links into Your Konecranes – that’s a dashboard approach, a repository of all the information associated with every crane we have under contract. Through a cellular modem, every crane communicates to a central server in the background. We gather the statistics on number of cycles, use, overloads, whatever might be taking place – and we digest that information, we process it and we’re able to give our customers feedback on how the cranes are being used, in a positive manner, so they can make sure that they’re maintaining them properly, and redirect bad operations by operators that might be overloading the crane, might be hitting E [emergency] stops unnecessarily.
[It enables] our customers to be proactive from a safety standpoint, maintenance standpoint, spend standpoint.They can track anomalies, they can do all sorts of things that are predictive as opposed to reactive.
It’s big part of automotive. In fact, our automotive customers are enjoying that more than probably any other industry we sell to.
FINALLY, WHY IS THAT?
That’s primarily because of a very strong safety culture. Safety is paramount, just like every industry, but it seems more so in the automotive industry.
I think it has to do with the evolution of the industry. When you talk about facilities and environments, where there are unions, many times that environment has… stricter mandates and requirements. The safety features I mentioned [earlier] – hook centring, protected areas, target positioning – almost a majority of our customers today in the automotive sector require it as part of their buying process.
And [the vehicle manufacturers] are multinationals – they want consistent safety policies. Safety is number one and two in their culture.