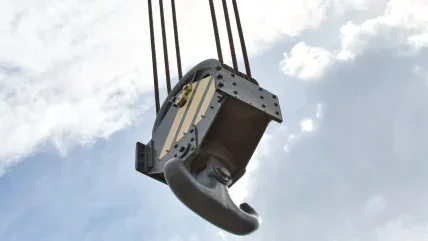
All slings are classed as accessories, so in accordance with Lifting Operations and Lifting Equipment Regulations (Loler) they are inspected every six months by a competent person, who decides what tests are necessary to supplement the thorough examination.
As with all lifting equipment, the one basic thing we must do is be able to visually look at it. The wire rope sling will need to be physically there to carry out a full thorough examination. A thorough examination, for example, cannot be carried out at the end of a phone or even via Facetime or Zoom. Visibility is essential – if you do not see the wire rope sling, you can’t make a judgement or pass it fit for continued service on a presumption or by word of mouth that it is safe.
When we are looking at any form of slings with regards to single leg slings, multi-leg slings, every single sling and every single part of that sling needs to be inspected. When inspecting steel wire rope, we are looking for a multitude of things that must be thoroughly examined – the list of defects is not exhaustive. Importantly, we are looking for defects such as broken wires and strands. One aspect that requires some thought during inspection is when it comes to kinks.
A kink in wire rope is a permanent deformation or reshaping of the rope. It is caused by applying a bending force beyond a wire rope’s tolerable level of flexibility. Kinks lead to an imbalance of lay length, which will cause excessive wear and in severe cases the rope will be so distorted that it will have only retained a small proportion of its strength. Kinking is a permanent deformation of strands in a wire rope caused by unintended bending, twisting or misuse.
Slight bends in a rope, where wires or strands that are still in their original position, with no broken wires, core protrusion or flattening of the rope would not be considered serious damage. Depending on the condition of the whole wire rope sling it could be found that the sling may pass.
When it comes down to kinks there is no set hard discard criteria – it is down to the judgement of the competent person. One thing to look for is wires or strands that are pushed out of their original positions in the rope. For example, as you start bending steel wire rope around tight radiuses, the core may start to become exposed, something that might be observed around ‘hard eyes’, and it can open up the strands exposing the core.
A more extreme kink, such as putting a sling around a load with sharp corners, will put the wires on the outside under tension while the wires on the inside will be put under compression and this will result in a flattening of the rope, which adversely affects the strength as it will have also damaged the core. Also, within the area of the kink/ permanent deformation as well as flattening on the rope you are likely to see a lot of broken wires.
Of course, kinks can be minimised from the outset by adhering to best practice during handling and storage of wire ropes. As pointed out by the Lifting Equipment Engineers Association’s Code of Practice for Safe Use of Lifting Equipment (Copsule), which can be accessed or downloaded at leeaint.com as a guide to best practice, care should be taken to prevent kinks or twists when handling ropes, particularly when uncoiling the rope – it should be ‘reeled’ off and not pulled from the coil sideways. Improper handling of wire ropes can quickly result in kinking, usually commencing with the formation of a loop. If this loop is drawn tight the rope will be irreparably damaged.
As mentioned, looking for kinks during an inspection is just one small element of an inspection of wire rope, albeit one that requires the judgement of a competent person. To avoid the risk of failure of lifting equipment and the potential for accidents, best practice should be followed throughout the inspection process with consideration of every part of a wire rope.