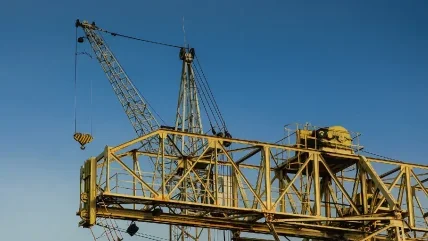
Beam clamps are a lifting device used to handle I-beams or fabricated girders. Such beams are commonly found in construction, used for framework by the metal building industry, while other loads are manufactured with I- or H-shaped cross-sections for ease of lifting or installation in a multitude of scenarios.
Beam clamps are sometimes called beam grabs, but this is an interchangeable term deriving from the product’s ability to ‘grab’. The significant differences to understand are not in the name, but in the variety of types available, which can range from 1.0 ton to 50 tons in capacity. It is not a product sector that generates much demand for custom solutions – they do arise occasionally – so it is important to understand the application and source the right standard beam clamp.
The type of beam clamp a user might need will likely depend on the enduser market in which it will be applied below-the-hook. Not without exception, but smaller units may be found in basic fabrication or to mount a hoist on a beam in a work area; larger units are typically used in bridge and building construction.
In all scenarios, it is important to know everything (weight, length, shape, etc.) about the beam/s to be lifted. It will likely be necessary, especially when larger sizes are required, to use more than one clamp on a spreader beam or even in conjunction with a bridle sling. Clamps are thusly part of a wider lifting system which, as always, must be understood from top to bottom.
Clamps with an adjustment screw are easy to adjust, while higher-capacity models without adjustment screws may need help from a crane to open them.
Our standard range, for example, starts with a 1.0-ton capacity product, which is a simple design and typically utilised in permanent installation for lifting and positioning structural beams. This type of clamp is often used in pairs in conjunction with a spreader beam for additional versatility. It allows for the capability of hanging hoists or rigging from an overhead load-bearing structure. As is the case with this product, it should be clearly marked if a clamp is only for vertical lifting, and the manufacturer will often point out where a similar alternative is better suited to longer loads.
There are beam clamps that are designed to accommodate side-loading, offering full rated capacity at any lifting angle. These clamps are often sourced when there is a need to upend and lift beams during a manufacturing or production process. They can also be used for lifting and hanging.
What we call our Model F clamp is relatively large in size – it eliminates the need for slings and chokers in vertical lifting, increasing operator and worker efficiency and safety. The unit features a specially engineered recessed base that accepts studs welded to a beam’s surface, allowing operators to get a secure lift without any additional rigging. The recesses in the grab that provide clearance for studs are a popular feature because it means contractors do not have to keep two different grab styles on hand. This model has been around since the mid-1980s, versus our girder clamps and beam flange clamps that followed approximately a decade later.
A beam flange clamp, which we offer in 1.0- to 10-ton capacity, presents a left-hand thread and right-hand thread screw spindle, allowing for rapid clamping and unclamping. A lock nut prevents inadvertent loosening of clamp. The jaw opening adjusts to a wide range of beam types and flange widths, and it is available with a large bail option for oversized hoist hooks.
The list goes on, only emphasising the need to source and apply the correct beam clamp for the application at hand. All clamps should be inspected as per manufacturer’s guidance, and stored to avoid damage, keeping them out of water, mud and other materials that might be found on a construction or other outdoor site.
Clamp Down
Two types of bad practice continue to endure in industry when it comes to beam clamps:
- There is nothing wrong with synthetic slings per se, but they are too often used to lift beams without edge protection. While protection (or packing) can sometimes solve the problem, beam clamps are generally accepted to be a better option, especially for repeated use.
- Even a beam clamp can be the wrong product if it is not the right type and capacity for the lift. Just because a clamp safely lifted one I-beam or fabricated girder, that does not mean it is suitable for the next one. The clamp, or grab, must be designed for the size of beam being lifted.