
Can you tell us a bit about yourself and your role as an industry leader?
I am 49 years of age, and I live with my family in the city of Remscheid, Germany, that is located conveniently for Cologne, Düsseldorf and the Ruhr region. Frankfurt and Hanover can also be reached by car in around two hours, so the location is very central.
I studied business administration and mechanical engineering at the Technical University of Darmstadt. At that time, my main interests were in the automotive sector and in the optimisation of supply chains.
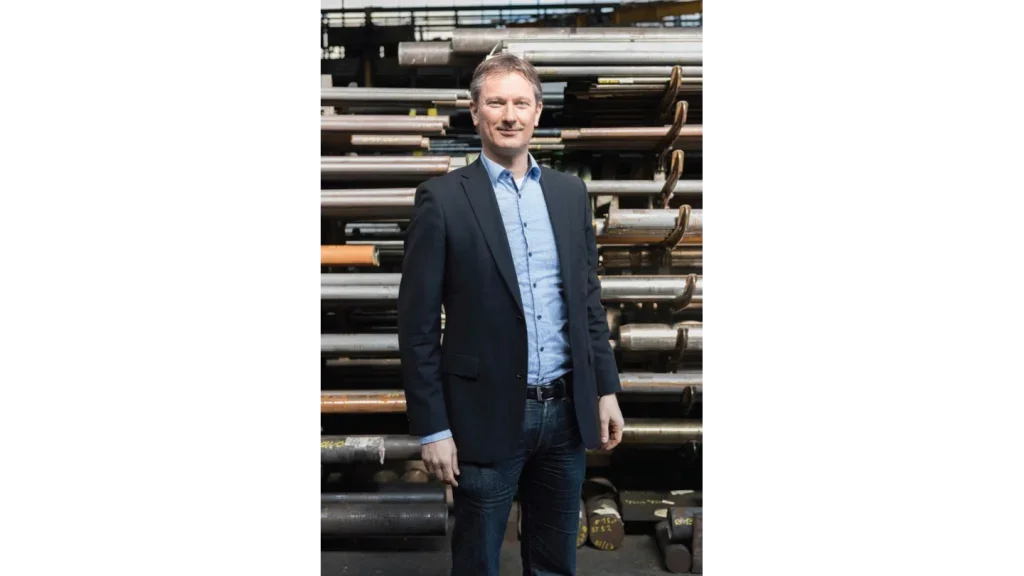
During my studies, I had the unique possibility to do an internship with the Materials Handling Industry of America (MHIA), which was renamed and today is known as MHI. I am still very thankful to John Nofsinger, the CEO at that time, who took personal care of me and introduced me to the industry.
During my time as a research assistant at Ruhr-Universität Bochum, chaired by Professor Gerhard Wagner, the “Father of the EN 13001 crane standards series”, I was involved in different projects in the materials handling industry. At that time, he taught me a lot about cranes in general and specifically about crane standardisation. I am grateful that I was allowed to support him also by attending meetings on national, European and international levels. All of this gave me the expertise to hold workshops and to train many people in the branch. Later on, I was awarded a doctorate.
Of course, standardisation also helped me when joining the family’s company. It is a challenge to enter, if you have such outstanding personalities like my grandfather and my father. But, at least in the field of crane standardisation, I could bring new knowledge into the company, so I was recognised by the employees right from the start.
I am still involved in crane standardisation today. Meanwhile, I am the chairman of the national steering group for cranes and lifting equipment that coordinates all crane standardisation activities in Germany on a national (DIN), European (EN) and international level (ISO). In the Research Association Intralogistics/Conveyor Technology and Logistics Systems IFL, I am chairman of the board; in the Crane Service Association GKS (Gütegemeinschaft Kranservice) I am a member of the board; and, amongst others in VDMA, I am member of the board in the specialist department cranes and lifting equipment and in the trade association’s materials handling and intralogistics. On a local level, I am actively involved in the chamber of commerce and I am also an honorary commercial judge.
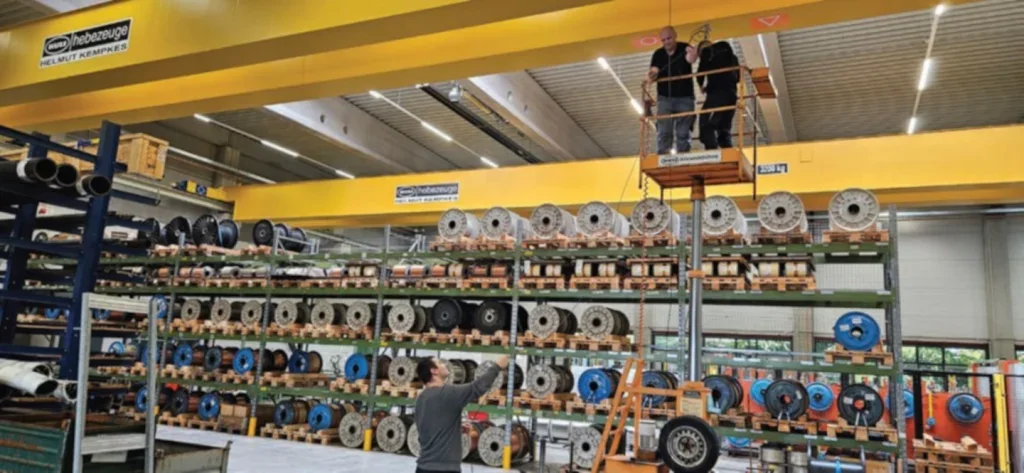
Since 2009, I am the managing director of KULI Hebezeuge, which is completely owned by our family. We have many years of experience in the development and production of customised crane solutions and crane components. In my role, I combine technical expertise with strategic vision to position our company for the future. As an industry leader, we focus on innovation, quality “Made in Germany” and close cooperation with our customers. My aim is not only to deliver robust technology, but also to design sustainable solutions for the challenges of today and tomorrow.
Can you tell us how you got into this industry and why?
Somehow, I grew up in the world of cranes and in the industry as part of our family life. I often attended trade shows or met business contacts as a child. Our company’s spectacular exhibits on the CeMAT in Hanover made a lasting impression on me.
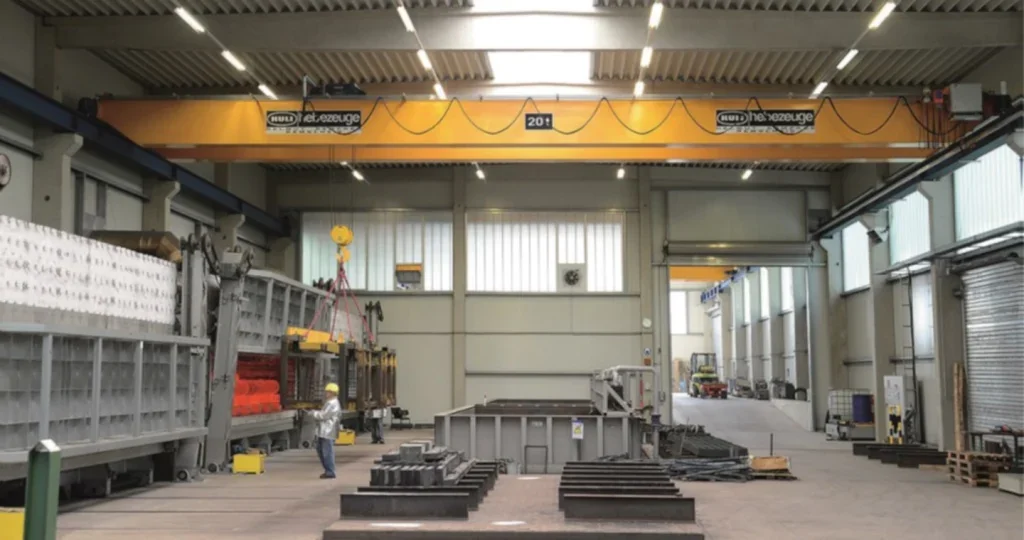
Besides running the crane business, my grandfather and my father had leading positions in the industry in various organisations. Among others, my father, Heinz Helmut Kempkes, was first deputy to the president of the German Institute for Standardisation (DIN) and president of the European Materials Handling Federation (FEM). In his position at FEM, he represented more than half of the worldwide production volume in the materials handling industry. All this was followed by his engagements in the Association of Materials Handling and Intralogistics in VDMA, when he chaired the cranes and hoists department that he formed in 2004 from two divisions.
Heinz Helmut Kempkes was also a member of the Presidium of the German Federation of Industrial Research Associations (AIF) and one of the leaders to found the Research Association Intralogistics/Conveyor Technology and Logistics Systems (IFL) at our company premises in Remscheid, to name just a few. Therefore, the largest financial daily newsletter in Germany, Handelsblatt, named him “lord of cranes and crabs”. For his outstanding commitment, in 2013 he was awarded the Cross of Merit on Ribbon of the Order of Merit of the Federal Republic of Germany.

I very much appreciate that my father never put pressure on me to take over the family business. But, of course, if you grow up in this business, it feels like both being an honour and an obligation to take over responsibility in the company and, furthermore, to support the industry as a whole on a voluntary basis.
Although my job is mostly in administrative tasks, from time to time I still find the chance to work on a crane with my own hands. And I think it is very important to do such basic tasks, as your own impression of the products cannot be replaced by any other means.
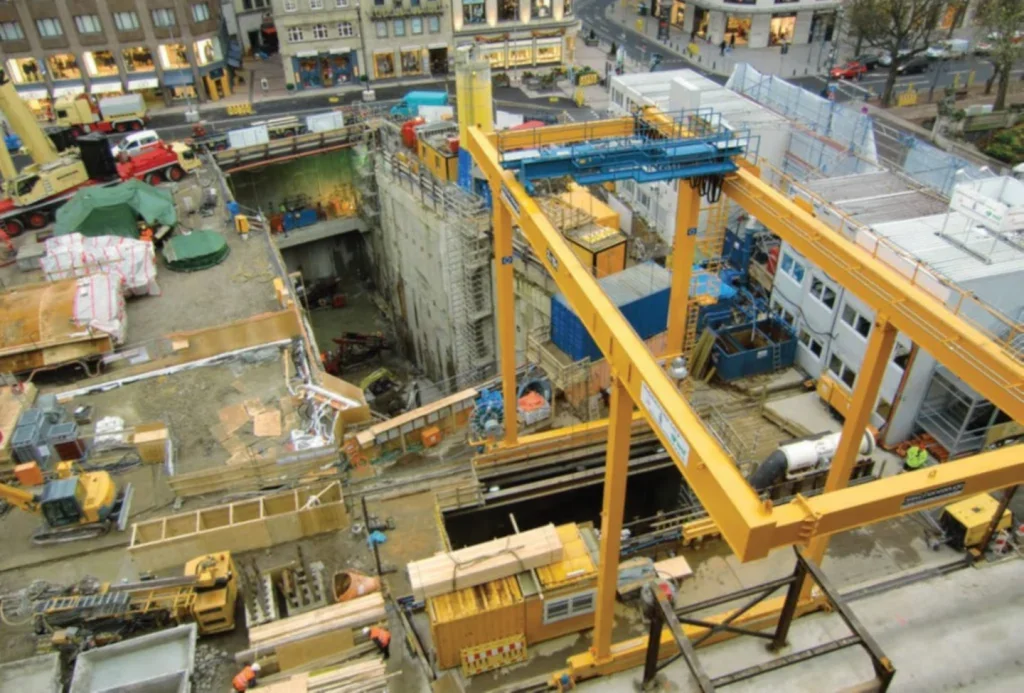
What makes your company stand out?
What defines us is the combination of over 100 years of tradition and consistent innovation in crane design. As a well-known market leader, we combine deep technical expertise with a strong commitment to quality, safety and reliability. Our customers value our tailor-made solutions, longlasting products and personal service. We are proud to shape the future of crane technology while staying true to the values that have defined our company for generations.
The history and development of the company itself is impressive. The predecessor company Tillmanns began back in 1856 in Remscheid. In 1913, this company merged with a crane building company from Düsseldorf and was renamed Schenck & Liebe-Harkort AG. In 1922, they started the KULI brand for their electric lifting tackles. This was the beginning of the famous KULI wire rope hoists – the core product for our success.
My grandfather, Helmut Kempkes, started his business in 1947 in the city of Duisburg. At that time, Duisburg was a booming city with lots of opportunities to do business with the growing German heavy industry. As the beginning was with manual lifting equipment, in 1955 his company built its first complete crane. In 1957, he had the fortunate chance to buy the KULI factory in Remscheid and to fulfil his wish to build his own crane components. In the following years, he merged the two production sites in Remscheid and also moved his family.
The integration of the KULI wire rope hoists in his own production has only been the starting point to build up a unique depth of production. This is a successful model that we continue to develop today. Today we are building motors, gear boxes, steel structures, control panels and further components inhouse. To this end, we have a well-equipped mechanical workshop with the ability to manufacture all the core-parts like gears by ourselves.
All over the years we have been involved in leading developments. The company began exporting cranes to India as early as in the 1950s and, in 1962, we equipped the first crane with a remote control. This was the year also when the public radio Deutschlandfunk started in Germany.
Since the beginning, we have pursued the philosophy to build strong and robust hoists and cranes. So we are meanwhile manufacturing compact hoists with up to 63t capacity at four falls of rope or special hoists with up to 200t capacity. As far as we know, we hold the world record for designing and producing the strongest monorail hoist for a curved beam in the world with a capacity of 192t.
Working since 2014 on a game-changing system for reducing energy consumption, in 2018 we made the first installation in an automatic crane whose control system was awarded with an innovation price. This was the starting point for our ‘smartER’ control system with energy recuperation and remote access.
When celebrating 100 years of KULI in 2022, we looked back on numerous projects of bridge and gantry cranes as well as of crane components we delivered to more than 120 countries in the world, from the desert to the Antarctic, and from the jungle to the different fields of industry.
What do you like about the industry?
I really like the combination of building large steel structures within tiny mechanical engineering tolerances and making them functional with clever control technology. The basics are similar to what I enjoyed playing with as a child. But, of course, our products are larger and technology is nowadays far more sophisticated.
Furthermore, the people in the industry somehow are like a family. In Germany, we say that once you have found a fascination for cranes, you will never change the branch again.
Despite all the enthusiasm for technical solutions, customer benefits must always take centre stage. Sometimes there can be simpler, suitable options alongside complex and highlevel solutions, which some people refer to as German overengineering.
But that is the fascinating thing – to find the best solution in so many different applications based on the broad possibilities we have.
Why should people want to join and work in this industry?
The crane industry offers meaningful work with real impact – building the backbone of modern infrastructure. At our company, with over 100 years of tradition, employees become part of a team that values craftsmanship, innovation and long-term thinking. It is an industry where you can grow, learn from experienced professionals and see the results of your work in action. We foster a culture of respect, equal opportunity and open dialogue. Joining this field means contributing to something lasting – and being recognised for it.
We spend a significant amount of life time at work – regardless of how many hours a week we work. That’s why it is important to have a fulfilling job. In our company, the work is very varied due to the vertical range of manufacture and numerous opportunities to realise projects. There is something new to learn every day. At the same time, there are different requirements and mentalities in the numerous industries and countries that we have to adapt to. The best prerequisite for working in our company is an enthusiasm for technology. We regularly provide apprenticeships to people to fascinate them to work on cranes in various positions.
The results of this work are solutions for lifting loads in a safer and more environmentally friendly way than without them – or otherwise the transport would not even be possible. Whatever you think of in everyday life – everything has to be transported. Without our industry, the world we live in today would simply not be possible.
It is also a great feeling for the entire KULI team when, for example, locally a crane can move smoothly on a poor old crane runway thanks to contactless electronic track guidance. Or globally, to deliver a crane that supports climate protection by running in an installation that filters CO2 from the air.
What are your expectations for the industry going forward? Any trends or challenges that you foresee?
It is fascinating where the industry has come from and how similar today’s goals are. In materials handling, the aim was always to maximise efficiency. In ancient times when building up the pyramids, it was the question of workforce. Even with the further development of cranes, muscle power was guiding. Historically, a boost in the development of cranes was only driven forward by electrification. In fact, the predecessor of our company electrified the first cranes in Germany more than 120 years ago. Today, we are minimising the consumption of electricity as well as the environmental impact.
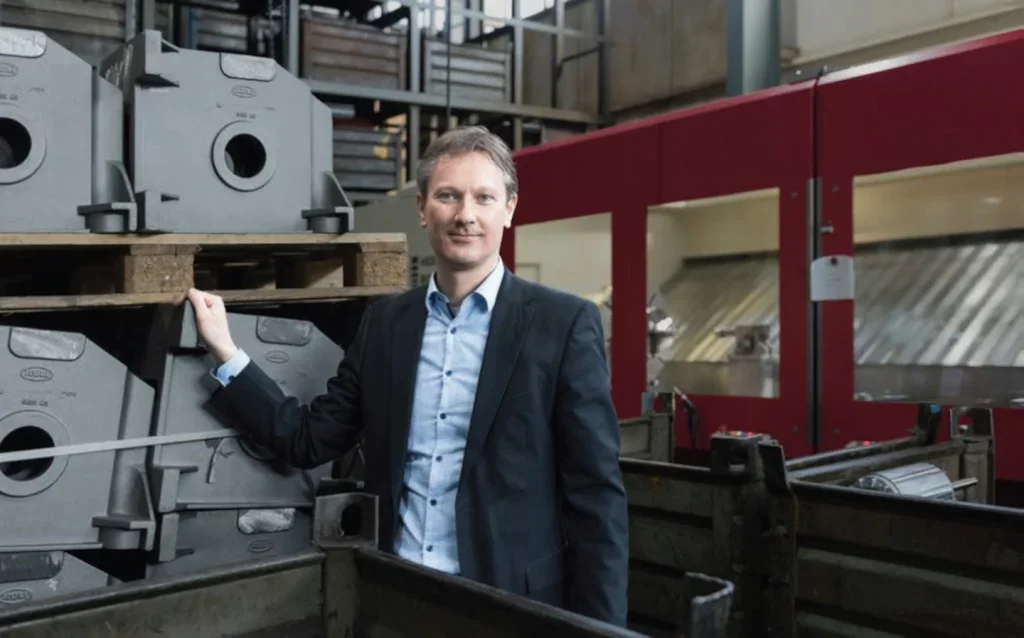
Another trend in the industry is to increase the productivity and to reduce costs by customised and service friendly solutions. Today, we have a sophisticated modular system, a unique vertical range of manufacture and a high proportion of engineers in our workforce to implement customised solutions that perfectly fit for the individual applications and offer lowest possible costs of ownership.
Also safety and comfort have become increasingly more important for all people working with cranes. In addition, technical functions and assistance systems are being used more and more frequently as they become more affordable. With digitalisation and more sophisticated control systems, future possibilities seem to be nearly endless.
Looking ahead, I see both great opportunities and significant challenges for our industry. Sustainability, digitalisation and automation will continue to shape crane design. Customers will increasingly demand energy-efficient, smart and flexible solutions. At the same time, we face global supply chain uncertainties and a growing shortage of skilled workers. Our aim is to combine proven technology with forward-looking innovation – and remaining adaptable while holding on to our core values of quality, safety and reliability.
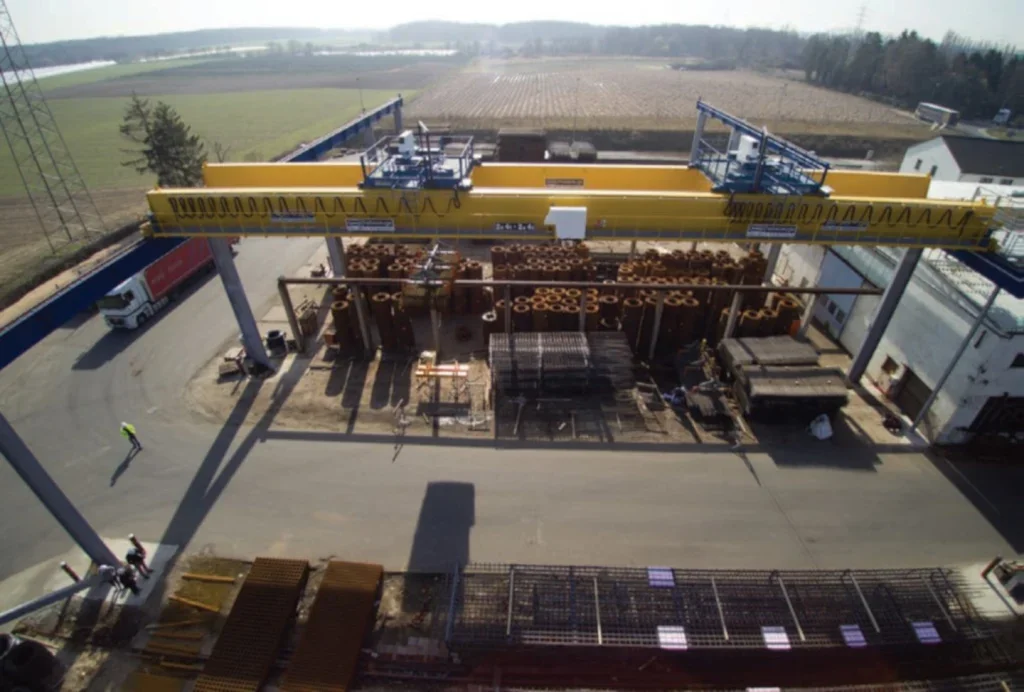
Are there any projects or initiatives that your company is working on that you’re excited about?
Yes, we are currently working on several exciting projects that reflect both our tradition and our commitment to innovation. One key initiative is the development of energy-efficient crane systems that integrate smart control technologies – helping our customers to reduce emissions and to improve operational efficiency. Particularly noteworthy is our control system with energy recovery for frequencycontrolled cranes, which has won an innovation award. When we started, there was only minor interest in this technology. Either it was supposed to be too complicated or too expensive, or in high duty applications there have been concerns regarding the reliability. It was only with further development that we could set up a system that was easy and cheap to use.
When lifting loads, the motor consumes electric energy while the motor works as a generator when lowering loads or breaking. In conventional crane control systems with frequency inverters, this energy is dissipated into heat via braking resistors. With our innovative control systems, we can feed electrical energy back into the grid. When energy prices suddenly rose due to the shortage of Russian gas, our solution was already in use several times and became a sought-after piece of equipment for our cranes. This is a good example of a technology that helps to minimise the environmental impact as well as to reduce costs.
We are also investing in predictive maintenance services, low-wear systems and remote diagnostics and are preparing for further developments in the digital sector, including in connection with AI. These efforts are part of our broader strategy to combine more than 100 years of engineering excellence with the demands of a modern, sustainable industry.