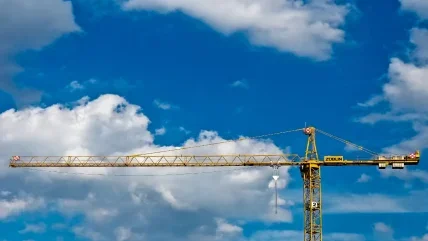
Hoist Magazine began writing about anti-sway systems almost 20 years ago, but the origins of anti-sway go back much further. Some 420 years back further, in fact, to around 1602, to a day when Galileo found himself in Pisa cathedral. Bored, we presume, by the sermon he found himself watching the heavy chandelier swinging on its chain from the roof.
A small swing, he realised, takes just as much time as a big swing. The period of the swing depends only on the length of the supporting rope, not on the amplitude. The equation that governs pendulums is taught in most introductory physics courses: And the euation shows that the time of each oscillation, T, depends only on the length of the rope and the acceleration of gravity. The weight that you hang on the end does not affect the timing at all.
Hence the invention of the pendulum clock, and, more relevantly for our purposes, the somewhat later invention of anti-sway. A load swinging on a wire is nothing more than a pendulum. So it obeys that same equation. To find the period of each swing you don’t need to know what load you have picked up – you only need to know how much wire you have paid out, and that is reasonably easy to measure.
And to cancel out the swing – to make the rope hang practically vertically as you move the load along – all you have to do is move the support – the trolley – at the same speed as the load at the end of the rope. A simple mathematical algorithm could do the sum and adjust the trolley speed accordingly.
In a simple, ideal world, that would be all. The world, however, is rarely simple and is ideal only sometimes. If your hoist is in the open air there is wind that can add an extra, unpredictable sway to your load. Even without wind your load is not actually hanging from the rope: it is the hook that is hanging from the rope, and the load is hanging from the hook, perhaps via a length of rigging – so the load can swing from the hook while the hook is swinging from the rope. In which case you don’t have a single pendulum, you have a double one – a pendulum hanging from a pendulum, and each pendulum swinging at its own speed.
An expert crane operator, with years of experience, can handle all this and move his complicated load without it swaying. How he does it is explained by Casey Cummins, senior electrical engineer, at Columbus McKinnon/Magnetek.
“Highly skilled, experienced operators counter sway by driving into the swing to dampen it,” he says. “After picking up the load, the operator starts the crane, slowly at first, to judge how the load sways. If the crane operator momentarily stops or slows the crane and waits for the load to swing forward, he can again start the crane moving at the same speed as the load at the moment that the load is directly under the trolley. The operator repeats this manoeuvre as needed until achieving the maximum desired speed.”
And stopping uses much the same technique in reverse: “Getting closer to the target position, the operator reduces speed, drifts, or even applies negative power to brake (it is known as ‘reverseplug’) and that way induces a forward sway. As the load nears the target position, the operator increases speed slightly so as to position the load point on the trolley over the target position with little sway.” These complicated load control manoeuvres, often referred to as ‘catching the load’, depend on both the skill of the operator and on the speed and acceleration of the crane.
MATHEMATICAL ALGORITHM
As we have said, a mathematical algorithm, based on our equation above, can do much the same thing. Several anti-sway systems are on the market and can be divided into two basic types. One, called ‘open-loop’, relies solely on the algorithms. The other, ‘closed-loop’, type also relies on algorithms, but uses feedback from sensors as well. It might seem that sensorbased system has the advantage: it ‘sees’ the real position of the load in the real, actual, imperfect world, not the theoretical position where the load ought to be if nothing untoward has disturbed it. In fact, though, in many applications a sensor-less system has the advantage. It is a matter of horses for courses.
Khalid Sorensen has spent most of the past two decades on anti-sway. He is the man who devised the ExpertOperator antisway system – which is sensor-less – and the CraneVision system, which has sensors. “I devised ExpertOperator while I was working for my own company, CAMotion, which got taken over by PaR, who I then worked for as their chief technology officer and who now offer the system. In 2020 I left to set up another company of my own, Finity Engineering. We offer expertise in automation, mechatronics and robotics.”
Sorensen can explain the two types of anti-sway technology. But first, he says, we should take a step back and explain the two types of load swing. “There are actually two classifications of load swing,” he says. “There is load swing which is induced by an operator driving the trolley around. Operator-induced swing can happen whether you’re indoors or outdoors.
“But then there is a completely different classification of load swing that is induced by external disturbances. It might be the wind if you are working outdoors. Or maybe it’s just a rigger who goes up to the bottom block and gives it a shove. Or a more practical example of an external disturbance is if you are picking up say a 10t die at an automotive die stamping plant. The die is sitting on the ground, you attach the rigging, but for some reason the trolley is not perfectly plumb with the load. Maybe it’s off to the side by a couple of metres. Then as the hoisting action begins and the line gets taut, that load comes up off the ground and it is swinging because of that off-vertical pull. That too would be considered an external disturbance swing.”
So how do you deal with an external swing – one that is caused by wind, or by a rigger pushing, or by the lift being slightly off-plumb? “In that case you have to use a sensor-based system. There is just no way around it.
“Typically, technology to get rid of that kind of sway is based on machine vision. We attach a sophisticated camera to the trolley, and it looks down so that it can see the hook and the surrounding workspace, and it can detect all kinds of unsafe hoisting conditions. It can detect side-loading of the crane, or snag incidents. It can tell whether or not there’s an externally induced sway that’s happening and it can feed that back into the algorithm.
“An algorithm is simply a set of instructions. There are algorithms that are specific for handling snag situations or sideload situations or for handling sway resulting from an external disturbance.
“The input from the algorithms is fed back into the trolley controls; they tweak the operator’s own commands and adjust them to become the commands that a really expert human crane operator would be giving.”
ON AND OFF
You might imagine that if you have an anti-sway system on your crane you would want to keep it switched on. Not so, says Sorensen: “Typically, depending on the application, you don’t want to have these algorithms running all the time. For example, if you want to eliminate sway caused by wind, what we have found to be the most pragmatic and the safest is where an operator has a button that he can press. While it’s being pressed the crane actively gets rid of wind sway. When there is no wind, the button stays unpressed.”
But there have been in the past, and to some extent still are, many cases where the operator has turned off the anti-sway because it slowed down the operation too much for his liking.
“That brings us back into the other category, the operator-induced anti-sway. When I got into this business, almost 15 years now, anti-sway was a bad word. You didn’t want to say it around crane operators; they absolutely hated it. In most plants that I visited where there was an existing anti-sway system operators would bypass it and shut it off because, first of all, it didn’t work very well. It really wasn’t getting rid of that much sway. It made it difficult to fineposition the load and it really slowed the operators down.
“So we had a real challenge coming to market with our new type of technology. It was anti-sway, but we didn’t want to call it anti-sway because it was so fundamentally different than what was out there before. And it’s still different than what’s out there now: to my knowledge even to this day, the anti-sway technology that I developed – ExpertOperator – is the only one that is purely sensor-less. Some others are advertised as being sensor-less but when you delve into them there are still encoders, something that is telling it what the hoist height is. Our system is completely different. It doesn’t use any information about the length of the rope. Or the rigging, or the weight of the payload or anything like that.”
As we have said above, the basic piece of information that governs sway is the length of your paid-out rope. Without that, how on earth can his system work?
Sorensen explains: “Suppose you had a crane and you knew everything about it. You knew that you had 5m of hoist length and you had a 1.0t load that was a certain shape and you knew how fast the frame was able to travel; if you knew all those parameters it is pretty straightforward to do the math and figure out how you can move that crane from point A to point B without very much swaying. It’s kind of a second-year engineering problem. And there’s not just one solution you could come up with. There’s actually an infinite set of solutions that would work to move the crane from point A to point B without swinging. You could move it very, very slowly all the way, or you could move it slow then faster then slower, and so on. Call that group of solutions Group A. It is all the solutions for doing Configuration A.
“Now suppose that you have a different configuration of a crane. Maybe instead of 5m of rope length it is 10m, and you have some additional rigging hanging off the bottom block, and you’re picking up a large horizontal I-beam that will itself add sway. Once again, as long as you know everything about it, all those details, you can do the math and come up with a family of solutions that works on that particular rigging configuration. Call that Group B.
“Then you do a Group C, for another configuration, then groups D, E, F, all the way through the alphabet for all the configurations you can think of. Now here comes the nice bit: there will be some overlap between the groups. There will be solutions in Group A that are also in Group B, and some of those will even be in Group C, and so on. It is like a Venn diagram: there will be a subset of solutions that work for every configuration of load and rigging that that crane can have. And what ExpertOperator does is just choose the fastest one.” So, bingo: you have an anti-sway procedure that works for all configurations of your crane without needing to know even how much rope you have paid out.
Note that it only works for that first classification, of operator-induced sway. If your crane is outside, subject to wind and weather, you would need to add a sensorbased system. “You have to add a camera,” says Sorensen. “Or if you’re wanting to detect when the operator has a side load or snags the hook on something, then you need a camera for that.” That scenario, for example, might deploy CraneVision.”
COST AND CONSISTENCY
A sensor-based system, as we have said, gives real information about the real position of the crane. Why then would anyone want a sensor-less system?
One reason, Sorensen says, is cost: without sensors to pay for and to calibrate on-site they are quick and simple to install in a new crane, or to retrofit to an existing one. Another, less obvious, reason is consistency.
“Crane operators are a picky bunch,” says Sorensen. “They get used to a crane the way it is, and one thing they really like is for the crane to behave the same way every single time they use it. If it takes five seconds to decelerate from top speed, they want it always to take five seconds to decelerate from top speed no matter what the load is or the lift height may be. They don’t want it to take three seconds with the load held high and six seconds when it is low. But that is what anti-sway with sensors delivers: it actually changes the way that it decelerates and accelerates depending on what that sensor is telling it. And that is one of the reasons why crane operators would turn off the anti-sways that were based on sensors – it is because it caused inconsistency.
“A sensor-less system, on the other hand, doesn’t know whether the lift is high or low, and it doesn’t care: it delivers the same pattern of movement for both. That makes the operator feel more comfortable with his crane and more at home with it.”
The advantage of anti-sway – whether open-loop or closed – are many. It takes less skill on the part of the operator – and skilled crane operators are hard to find.
“We have done the test many hundreds of times,” says Sorensen, “where we have taken an experienced operator and have them do certain manipulation tasks, and then a brand new operator and have them do the same tasks but with the anti-sway technology. And it is tremendous how quickly the new person can exceed the performance of the experienced operator.”
“The trend in industry is to remove the operator from the crane cab in order to free him up to perform other functions,” says Cummins of Columbus McKinnon/Magnetek, “and to have less experienced workers at each workstation hitch who independently move their loads. And a sway-control system can improve productivity by allowing the crane operator to concentrate on load engagement/disengagement rather than focusing on minimising load swing. It can also improve the accuracy of load placement and reduce material damage caused by incidental contact of swinging loads.”
And, nowadays, anti-sway really does work, and really does speed production: “A properly designed and adjusted swaycontrol system can reduce load sway by 85% to 95%”, says Cummins. “That reduces the risk of damage and personal injury. A crane with sway control allows an operator to use full-speed commands for all movements, resulting in shorter cycle times. Field tests have demonstrated that sway control improves productivity by 25% to 50% and reduces operator fatigue and the need for extensive operator training.”
Later this year, Columbus McKinnon will unveil its next generation of Magnetek crane controls, called Impulse G+/VG+ Series 5 variable frequency drives (VFD). All Series 5 drives will come with built-in sway control as standard. “So sway control will be easy to access and use for anyone who purchases a Series 5 VFD” says Cummins.
Two decades ago, anti-sway may have been clunky and not very efficient. Today, it actually works. Given all the advantages, of safety, speed and productivity, and the small cost of an anti-sway system in comparison to the cost of a crane, it is perhaps surprising that there are still overhead cranes without them. But the retrofitting of older cranes is still a flourishing business. If your own system is still swaying, perhaps it is time to put a stop to it.