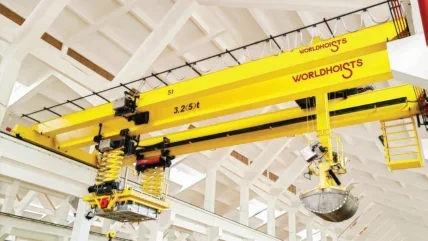
WORLDHOISTS’ brewing cranes combine the advantages of compact structure and lightweight design with exceptional durability to withstand harsh distillery environments (extreme heat, high humidity and heavy dust) while handling heavy-duty and high-frequency operations.
A major baijiu producer in Hunan province, South China – the region’s largest traditional liquor producer – operates continuous 24/7 brewing cycles to meet high-volume output demands. This requires the overhead cranes to feature exceptional operational safety, intelligent automation, digital integration, hygienic design and standardised processes.
WORLDHOISTS’ fleet of 14 automated overhead cranes serves as the critical material handling solution, delivering stable and efficient execution of cellar loading/unloading and distillers’ grains transfer operations.
For this project, WORLDHOISTS selected an automated electric double-girder bridge crane configuration with three synchronised lifting mechanisms:
- Main hook system: A grab bucket attached to a rigid and impact-resistant telescopic mast.
- Auxiliary trolley: A scissor lift mechanism providing automatic load sway prevention, self-aligning grab operation and automated load flipping capability.
- Third mechanism: The configuration is completed with an electric hoist.
All three mechanisms communicate via signal transmission and operate simultaneously within rated capacity limits.
Operation modes
A remote-control device and host computer are configured in the automated brewing area to execute automatic operation commands through instruction input.
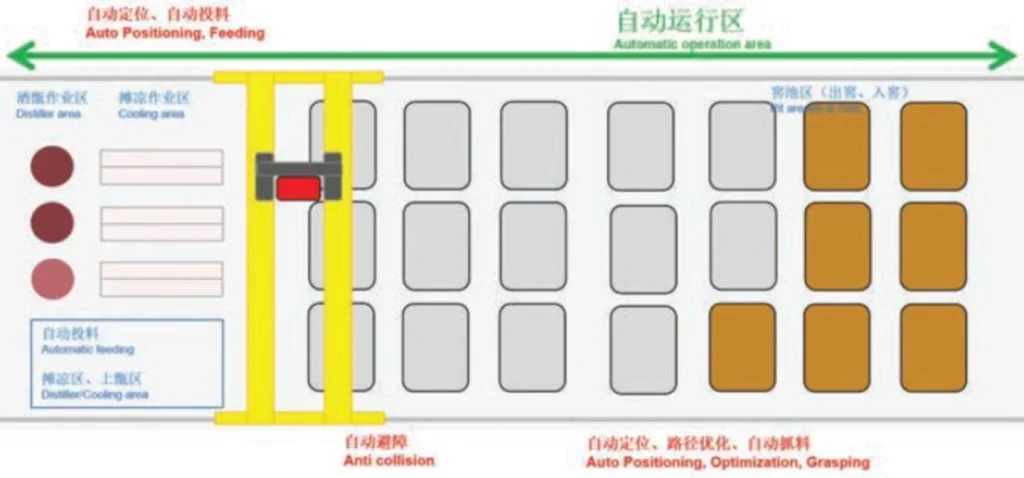
When unloading from the cellar is required, the operator in the automated brewing area selects the target cellar (for example, Cell B3) on the remote control and confirms startup. The crane will then proceed as follows when no other operations are in progress.
During the preparation phase, this automatically raises the grab bucket and material hopper to safety height and activates the bridge/trolley travelling mechanisms based on cellar position, moving towards the target.
In the unloading process, when positioned above the target cellar area the automated control programme lowers the grab bucket. Radar equipment on the hoisting mechanism detects grabbing depth and the grab bucket collects the distiller’s grains.
After successful collection, the grab bucket automatically raises to preset height, moves the trolley to position above the hopper and releases grains into the hopper.
For the completion protocol, the system returns to the cellar position and descends to a predetermined height and sounds a completion alert (single load cycle finished).
As part of the crane’s capacity management, total loading cycles can be preset according to hopper capacity. When reaching preset cycles, it sounds full-load alert; it raises the grab bucket and hopper to safety height; returns automatically to the brewing area; and positions/empties hopper into the transfer equipment.

When loading the cellar is required, it will necessitate the following:
- Initiation phase: The brewing equipment fills the charging hopper and the operator confirms startup command.
- Automated positioning: The crane automatically elevates grab bucket and hopper to safety height. It activates bridge/ trolley mechanisms based on target cellar coordinates and transports to the specified cellar position.
- Position verification: Upon reaching target cellar, an audible alert signals crane arrival. The ‘loading’ indicator light activates and the cellar operator verifies hopper alignment.
- Precise discharge: There is then a controlled release of the distillers’ grains, simultaneous hopper movement and discharge. Progressive unloading ensures even material distribution.
Position coding system
All fermentation cellars are assigned alphanumeric identifiers (for example, A1, A2, A3 through A7; B1, B2, B3 through B7, and so on) with corresponding numbered plates physically mounted at each cellar location for clear visual identification. The automated brewing zone and cellar zone are precisely demarcated to establish unambiguous positional references throughout the facility.
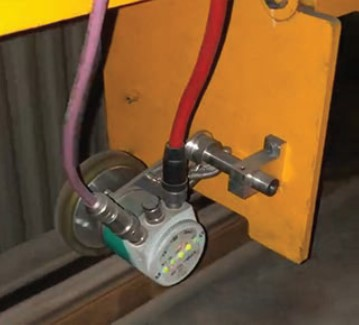
Intelligent positioning system
The crane’s bridge travel and hoisting mechanisms utilise absolute encoders for precise positioning. The bridge encoder is installed on the idler wheel, which maintains constant contact with the rail to prevent measurement errors caused by slippage. The hoisting encoder is mounted on either the hoist motor or the drum.
For the trolley, a linear scale positioning system is employed to ensure accurate alignment between the lifting apparatus and brewing equipment.
To eliminate cumulative errors in the absolute encoders during prolonged operation, reference zero points are installed every 30–50m along the bridge travel rails. A master reference point is positioned at the centre of the main girder.
Each time the trolley passes this point, its position data is automatically recalibrated to the absolute reference value.
The hoisting mechanism performs automatic position calibration after every 20 operating cycles by returning to a dedicated calibration point.
Through the implemented intelligent positioning system, the crane achieves the following operational tolerances:
- Bridge travel: ±10mm positioning accuracy.
- Hoisting mechanism: ±10mm vertical positioning.
- Trolley mechanism: ±5mm lateral positioning.
Obstacle avoidance
The crane’s laser detection system is set to monitor obstacles at a height of 6m. During automated operation, if an obstacle exceeding this height is detected within 15m, the crane immediately triggers an alarm and begins deceleration. Should the obstacle remain present as the crane approaches within 3m, the system automatically initiates a complete stop.
This fully automated brewing crane system delivers significant operational advantages, including annual labour cost savings exceeding one million yuan per production line and a three to five fold efficiency improvement in material handling through its intelligent kangaroo-style hopper system. The integrated AI computing platform enables automatic work order processing, optimised path planning and real-time collision avoidance. Advanced control capabilities include autonomous positioning, selfcorrection, auto-centering, inching, micro speed and ESR. The system also features built-in fault diagnostics, real-time performance monitoring via dedicated APP and remote data transmission functionality.
Market recognition and achievements
WORLDHOISTS has earned widespread market recognition for its outstanding performance and intelligent features. To date, the company’s independently developed multi-functional intelligent brewing cranes have been successfully delivered to several renowned distilleries, including: Wuliangye Co., Jiugui Liquor Co., Swellfun Co., Shede Spirits Co. and Jiannanchun Group Co.
These deployments have enabled fully automated brewing operations with zero manual intervention, revolutionising traditional production methods.
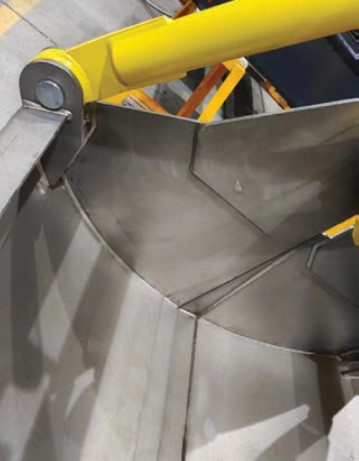
WORLDHOISTS’ intelligent brewing cranes achieve comprehensive performance optimisation through advanced data systems. The complete automated cycle – including positioning, grabbing, transferring, cellar loading, spreading, compacting, stratified unloading, transferring and precise placement – is completed within ≤20 minutes.
The system ensures ±5mm repeatable positioning accuracy across all mechanisms through integrated measurement technologies including linear scales, encoder tapes and idler wheel encoders. Radar monitoring devices enable precise level detection during unloading operations.
Speed parameters (adjustable by process requirements) for bridge travel are 0–120m/ min, 0–40m/min for trolley movement and 0–20m/min for hoisting speed.
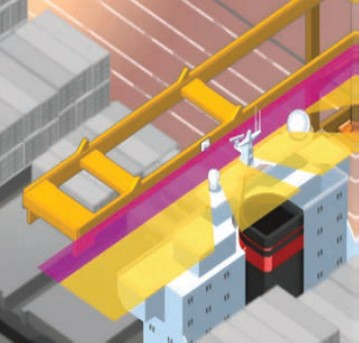
These configurable speed ranges allow precise matching with varying production efficiency demands throughout the brewing process.
Special configurations for brewing cranes
The baijiu brewing crane features dedicated configurations, including an open-mesh operator cab and stainless-steel grab bucket. It incorporates a mechanical anti-sway system with synchronised main/auxiliary hook communication, along with hoisting mechanism sway prevention and shock protection. The integrated safety system provides fault detection and diagnostics, safety alarms, emergency stop function and comprehensive electrical protections. These specialised safety measures ensure stable and secure crane operation in brewing environments.
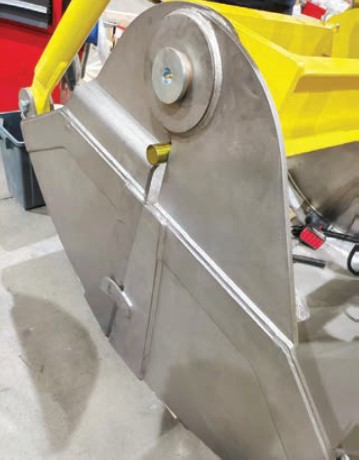
Environmental protection and sustainable development
WORLDHOISTS prioritises green manufacturing and sustainable development by utilising eco-friendly materials and production processes to reduce energy consumption and emissions. Through product life cycle management and green manufacturing initiatives, the company minimises resource usage and environmental pollution, achieving effective environmental protection.
WORLDHOISTS holds a Class A Special Equipment Manufacturing License issued by the Chinese government, along with crane installation and maintenance service licenses. The company is certified to ISO 9001, ISO 14001, ISO 45001, CE and ATEX standards, and owns crane calculation software copyrights. All crane products fully comply with ISO, GB, FEM, DIN, CMAA, BS and JIS international standards.
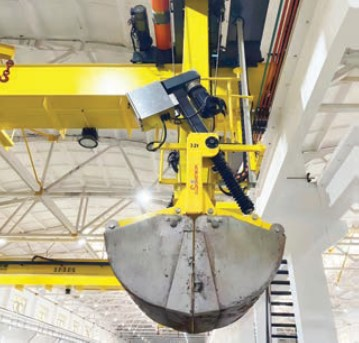
In summary, WORLDHOISTS demonstrates its specialised, refined, innovative and unique capabilities in the intelligent baijiu brewing sector through technological innovation, intelligent control systems, market recognition and eco-friendly sustainable development. The company provides comprehensive technical solutions and strong support for the baijiu brewing industry.