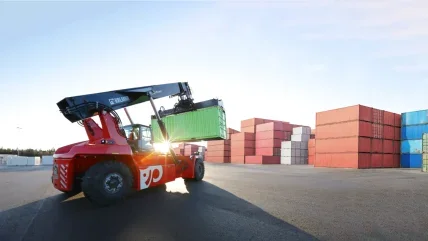
Kalmar, which is part of Finnish firm Cargotec, has announced the launch of the Electric Straddle Carrier Charge Family, the latest addition to its growing portfolio of fully electric equipment.
The company’s electrically powered offering already includes straddle carriers and smaller cargo handling equipment such as reachstackers and forklifts with varying lifting capacities.
The Charge Family comprises battery technologies, charging solutions and software to support operators of both manual and automated terminals with their transition towards decarbonised operations.
“The Charge Family is a comprehensive suite of solutions that enables terminals to transition to fully electric straddle operations quickly and smoothly,” says Arto Keskinen, senior VP, Horizontal Transportation, Kalmar.
“We have developed this offering in close cooperation with our vast customer base. The feedback from our customers has shown us that there is not only a need for alternative charging solutions but also for supporting software solutions that allow them to make efficient use of their electrified equipment and identify areas for improvement through monitoring and data analysis.
“With the launch of the Electric Straddle Carrier Charge Family, we are enabling our customers to choose the path to electrification that best fits their operational and strategic business needs.”
The family includes: the Kalmar electric straddle carrier with high-energy battery, capable of up to four hours of continuous operation with a charging time of 45–50 minutes; and the Kalmar electric straddle carrier with high-power battery (previously known as the Kalmar FastCharge straddle carrier), capable of up to 50 minutes of continuous operation with a charging time of five to six minutes using FastCharge technology.
There are two different charging options: a standard CCS charging interface compatible with any commercial charging station, or optional FastCharge technology where the onboard battery is charged via a pantograph at a FastCharge charging station.
Supportive products include the Kalmar Charge Optimiser software, which automatically assigns charging tasks to the operator to avoid queues at the charging stations and ensure “high utilisation of charging points”; the Kalmar One Fleet Optimiser software for Kalmar AutoStrads, which handles job scheduling and dispatching, including assigning charging tasks to equipment; and the Kalmar Insight Energy Module, which provides visibility over battery charging status, energy utilisation and charging KPIs.
SOLAR CELLS
Ports of Stockholm has decided to build six new rooftop solar cell systems to increase its solar electricity production by 55%.
The decision was taken in the summer to increase the company’s own production of solar electricity and the move is in line with the company’s and the City of Stockholm’s goals and strategies.
Ports of Stockholm is said to have worked for many years according to the City of Stockholm’s strategy to achieve a fossil fuel-free Stockholm by 2040. Within the sustainable energy area, Ports of Stockholm has increased its own production of renewable energy,
“Ports of Stockholm’s investment in solar electricity is fully aligned with our environmental goals. This decision means that in future almost one-tenth of the electricity we use will be generated by our own solar cell systems,” says Jens Holm, chair of the board, Ports of Stockholm.
Ports of Stockholm currently has five solar cell system installations that have a total production capacity of 995MWh per year. Now the number of solar cell systems will increase to 11, with a total production capacity of 1,545MWh per year.
The new installations are planned for rooftops at Frihamnen port, Värtahamnen port and Port of Kapellskär. Construction work is estimated to begin during Q1/Q2 in 2024 and the systems will be operational by the summer of 2024.
Ports of Stockholm works for sustainable port operations and shipping. The company previously set a goal to increase the proportion of solar electricity by 50% by 2026. According to the time plan for the new solar cell installations, this goal will be achieved already in 2024.
CABINLESS CRANE
Ireland-based Liebherr Container Cranes has launched a video highlighting the advanced automation capabilities of its new cabinless ship-to-shore container crane.
The crane has recently entered service at Patrick Terminals – Brisbane AutoStrad in Australia, where it is handling container vessels and automated landside operations.
The crane utilises Liebherr’s Remote Operator Station (ROS) for pick-and-place over the vessel and for exception handling. The ROS allows the same level of crane control as an on-board operator but from the comfort of an office-based environment.
“We are thrilled to unveil the automation capabilities of our Liebherr ship-to-shore crane at Patrick Terminals – Brisbane AutoStrad,” says Declan O’Sullivan, GM, Sales, Liebherr Container Cranes.
“This achievement signifies our dedication to working hand in hand with our clients to push the boundaries of port automation and providing cutting-edge solutions that transform operations. Through this video, we aim to showcase the power of automation in enhancing port efficiency, safety and profitability.”
This semi-automated crane is the first of its kind for Patrick Terminals, and one of the first cabinless Liebherr ship-to-shore container cranes to enter service globally, underscoring Liebherr’s commitment to driving technological progress in the port equipment industry.
“The introduction of the new semiautomated Liebherr ship-to-shore crane with a remote-control operator’s station marks a significant milestone in the Patrick Terminals crane fleet,” says Michael Jovicic, CEO, Patrick Terminals.
“We are proud to have collaborated with Liebherr Container Cranes on this ground-breaking project, delivering a crane that aligns with our unwavering commitment to safety and efficiency. This innovative addition enhances our operations and underscores our dedication to embracing technology.”
Patrick Terminals – Brisbane Autostrad has two Liebherr ship-to-shore container cranes. The first unit was supplied in 2015 and has recently undergone a lift height and outreach extension using Liebherr’s Transform technology. The new crane, meanwhile, features an outreach of 54m, a back reach of 48m, a lift height over rail of 40m and a span of 25.3m.
Watch the video on YouTube here: https://tinyurl.com/5yy7chsp.
MORE FROM LIEBHERR
Cadeler, an offshore wind industry company, has acquired a Liebherr Ram Luffing Offshore Crane, the RL 2600, as part of the modernisation of its O-class Wind Osprey vessels to support the next generation of wind turbines.
The Wind Osprey is one of Cadeler’s two windfarm installation vessels, which, in addition to offshore wind farm installation carry out maintenance and decommissioning tasks.
With its focus on logistical support – moving tools and smaller attachments – the Liebherr deck crane will provide support to the vessel’s larger main crane. It features a small tail radius and no machinery housing, which allows it to operate in confined space conditions. The 7.0m3 cabin is said to be ergonomic and ensures low-fatigue work for the operator. The Liebherr RL 2600 will replace an older, cylinder luffing deck crane.
The RL series cranes are primarily used for maintenance and supply work on both fixed and floating offshore installations, particularly in the wind power industry and the oil and gas sector.
The Wind Osprey’s main crane will also be upgraded. It will feature a lifting capacity of 1,600t at a radius of 40m, and a main hook able to reach 160m above the main deck.
“Besides upgrading the lifting capacity of our windfarm installation vessel main cranes to effectively handle larger and heavier wind turbines, we are also upgrading our equipment with innovative features and seeking strategic alliances with companies that will be with us in the long run. Liebherr fulfils our criteria for innovation, reliability and service, and we are looking forward to working with them closely on our flagship projects,” says Jacob Heinricy Jensen, COO, Cadeler.
“Our new partnership with Cadeler marks a remarkable opportunity for us to work with a leading provider in the wind energy industry,” says Stefan Schneider, global application manager General Purpose Offshore Cranes, Liebherr.
“This is a synergistic foundation for us in which we provide reliable products for Cadeler, while learning from our collaboration to further innovate our technologies to accommodate future industry growth. We look forward to a long and fruitful collaboration.”
Cadeler has installed over 500 offshore wind turbines and equally as many foundations and is aiming to become the key supplier in the industry’s ongoing development.
ANTWERP HARBOUR
Belgian logistics and transportation company Zuidnatie has ordered its first Generation 6 Konecranes Gottwald mobile harbour crane for operations in Antwerp, as it continues to build more capacity while lowering emissions and improving energy efficiency.
The crane was delivered in Q3 and will be assembled on site for commissioning and handover in Q4 2023.
As its business grows and the market demands more eco-efficiency throughout the supply chain, Zuidnatie said it ordered the crane as an easily adaptable, highperformance hybrid solution for one of Europe’s largest ports for handling both general cargo and containers.
“We’ve been using Konecranes Gottwald mobile harbour cranes in logistics for over 25 years. As their mobile harbour cranes are also assembled at our site for delivery to other Konecranes customers, we’ve had the chance to see the new crane up close and gain deeper insight into its technology. This convinced us that the Generation 6 would be the right solution for our own operations,” says Stephanie Feys, CEO, Zuidnatie.
“This new crane will be the 13th Konecranes Gottwald mobile harbour crane for Zuidnatie. The order underlines the strength of our long and special business partnership and confirms Zuidnatie’s confidence in Konecranes,” adds Alexandros Stogianidis, regional sales director Benelux, Port Solutions, Konecranes.
The order is for one ESP.6 crane, with a working radius of up to 49m and a maximum capacity of 125t to serve container ships up to Panamax class.
It will be used to handle breakbulk such as containers and general cargo. Strong lifting capacity curves, improved handling rates and a high classification ensure a long service life. It uses Konecranes hybrid drive, which consists of a modern diesel engine paired with an ultracapacitor that can be recharged by energy recovered from lowering and braking motions.
This gives the power needed for peak performance, while saving fuel on lighter loads. Prepared for an external power supply, the crane offers the potential for even higher eco-efficiency when connected to the harbour mains.