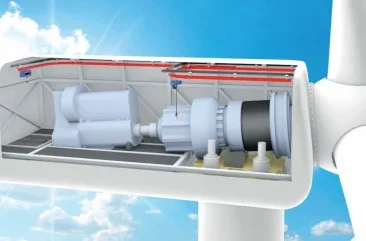
The power-generating industry used to be a simple one. There was fossil fuel, there was hydroelectric power, throw in nuclear – and that was about it. Today, the picture has been transformed. Britain’s last coal-powered generating station, at Ratcliffe-on-Soar in Nottinghamshire, ceased operations on the final day of September 2024. The year before, there had been nine. There are still 49 gas-powered power plants, which generate some 72TW between them, but that is expected to fall to 5% by 2030.
In their place have come the renewables – wind, solar, hydroelectric and bioenergy. The breakdown for 2023, according to the National Grid, was 29.4% of the UK’s total electricity came from wind power; 14.2% from nuclear; 5% from biomass; 4.9% from solar; with hydropower, including tidal, contributing 1.8% to the mix. Gas provided 32%, and the rest was imported via under-channel cable from France.
These ratios will change. Plans are in place to increase offshore wind output to 50GW by 2030, to which end the government is providing financial incentives and a £200m injection of cash. Solar capacity could grow to roughly 70GW in the same period.
The picture elsewhere in the world, though not in the US, is similar. In its renewables mix, Britain lags Scandinavian countries – which have much hydro – and France that tends to rely heavily on nuclear. However, the UK is nevertheless respectably placed, especially in its current and planned offshore wind generation. The outstanding global player, however, is China, which has the largest installed wind generation capacity in the world and the highest growth rate.
All of this means that the lifting requirements of the power-generating sector have changed hugely. Fossil fuel requires large overhead cranes to service and replace boilers, and huge overhead cranes in turbine halls. Hydro still needs those large-capacity turbine hall cranes, with the added complications of needing to be sited within the dam and water-flow structure. But renewables in general need very different types of lifting gear. The generators of wind turbines are sited at the top of tall towers – hard to reach in onshore installations, harder still in offshore ones. Yet they need servicing, spare parts and occasionally replacing. The hoist installed at the top of the tower, which raises and lowers the equipment, has become a design specialty of its own.
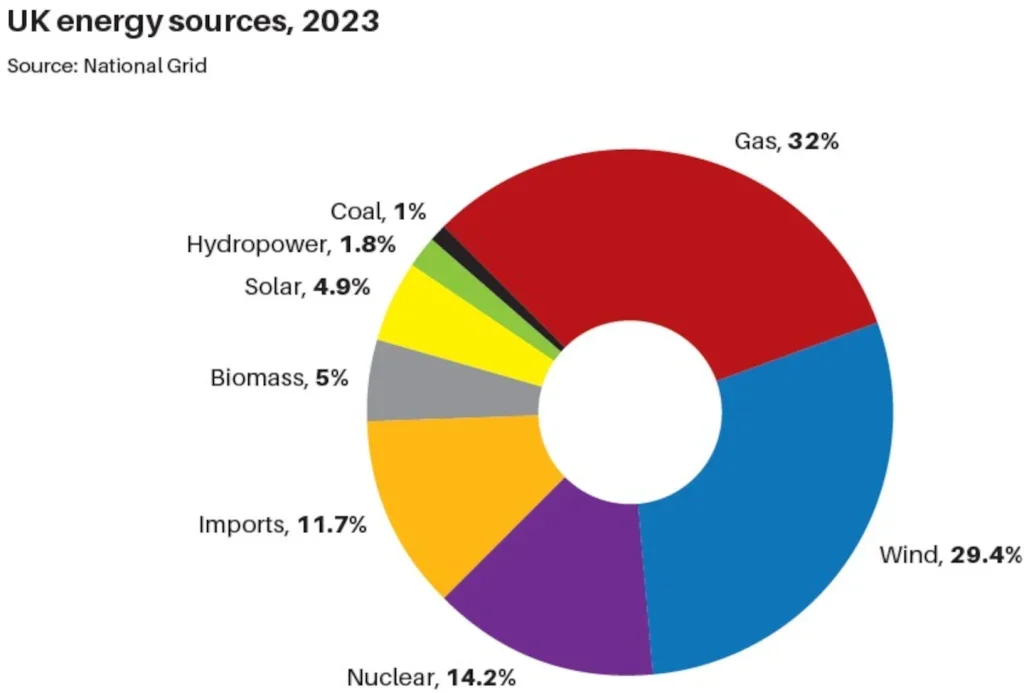
The requirements for such a wind hoist are that it should fit inside the confined space of the nacelle (as well as being compact it will need to be of low headroom); that, though used (and maintained) infrequently, it should be reliable and always available; and that it must have long lift heights. The requirement can be up to 180m for onshore towers while the latest generation of offshore towers are getting on for twice as tall.
Lifting speeds must be correspondingly high. Thus, the 1,000kg-capacity GP W electric chain hoist from Swiss manufacturers GIS is specifically designed for wind turbines and has a lift speed of up to 16m/minute, but its lift height is up to an impressive 200m. Raising a load from ground level to the nacelle at that speed, therefore, takes 12 and a half minutes. This raises another problem: a load approaching the nacelle trapdoor at that speed is highly likely to collide with it and cause a potentially extremely serious and dangerous accident. Yet, to expect the operator in the nacelle to stand at that open trapdoor and concentrate solely on the approaching load for ten tedious minutes or more without losing concentration is asking a lot – especially if he has to do it several times over in the course of the work. The GP W, therefore, switches from high to low lifting speed; the switching is automatic, actuated by a geared limit switch that comes into operation as the load approaches the top or bottom of the lift.
Liftket has been producing wind turbine hoists since the earliest days of the sector in the mid-1980s. Their ‘plug and play’ hoists are designed for voltage levels from 110–690V for 50–60Hz, which can be used worldwide. One of their standard products is designed for a lifting height of 200m with a load capacity of 800kg and a lifting speed of 20m/minute, but capacities of several tonnes are also available.
Liftket also make hoists for the offshore sector, where the environment is much more severe. Towers are higher, winds are stronger and more continuous and, critically, threatened by highly-corrosive salt spray. Specifications, therefore, need to be much higher. Special corrosion protection and paints are needed, as are specialised materials. Liftket products can also be equipped with stainless steel chain and hooks to avoid corrosion, with some components made of aluminium rather than the plastic of the onshore versions.
Demag have their DC-Wind chain hoist, with capacities of up to 1,500kg and lift heights to 180m. Kito’s single-phase ED electric wind hoist is lightweight and robust as well as weatherproof and corrosion resistant. Load capacities are from 60–480kg or higher on request; Kito claim to be the only manufacturer to offer ‘electroless’ nickel-plated load chains. Electroless refers to a process of depositing the nickel by a chemical process rather than by electrolysis. The layer deposited is known for its hardness and for its uniformity. The advantages here are higher corrosion resistance – there is, for example, reduced hydrogen embrittlement, which is a known hazard of metals in marine environments – and lower wear compared with traditional load chains.
Solar power also need not long detain us – it may well contribute very useful amounts of energy, but its lifting needs are fairly minimal and can be served by conventional nonspecialised equipment. However, solar, wind and tidal energy all suffer from a disadvantage – their output is intermittent. Calm, windless days produce no wind power, cloudy days produce little solar, and that’s not to mention nights, which occupy on average 12 hours out of every 24, produce none at all.
Renewables, therefore, have brought into prominence another need – energy storage. The power produced at peak times must be taken from the grid and stored, to be released back into the grid at times of peak demand.
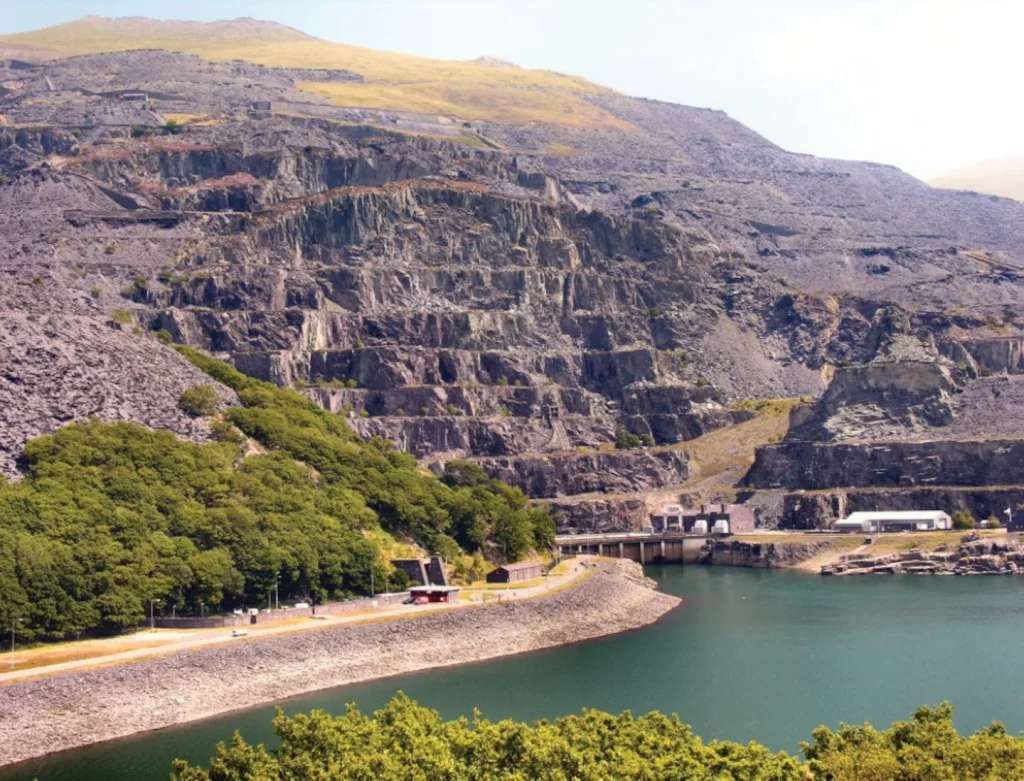
The problem certainly existed during the fossil fuel era. An efficient method of tackling it has been stored hydro. Excess energy is used to pump water to top of a hill – the better option being a mountain. When demand outstrips supply, it is released to fall down the hill, passing through a turbine that turns a generator as it goes. Stored hydro is efficient, if costly, but has the disadvantage that it needs suitable geology – for instance, a mountain, which gets rained upon but is located reasonably near to the population that needs its energy. In the UK, the Dinorwig pumped hydro station has been operating since 1984 and can store 9.1GWh of electricity.
There are alternatives though, and chemical batteries are one of them. Large lithium batteries of up to 3,000MWh capacity have been built in California. But lithium is in huge demand for more portable batteries – most obviously for electric cars – and the energy stored in them leaks out over time.
Another method has recently been put into commercial operation, which depends entirely on the properties of electric hoists. It has been known since Victorian times that an electric motor is a consumer of electricity when it is working to turn something, and a generator of electricity when something is working to turn it. Regenerative braking has been used in cranes and hoists for many years. When the crane lifts a load, it consumes electricity, and when it lowers the load, the work is done by gravity – the ropes, therefore, turn the crane’s motor causing it to generate electricity that can be fed back into the grid. Electric cars use regenerative braking in the same way – their batteries get recharged when they brake.
Hence the gravity battery – by using peak electricity to power a hoist to lift a large weight, the weight is happily kept at that height for a while. Then, when demand for electricity spikes, the weight is slowly allowed to fall. The unwinding rope turns the hoist, which turns into a generator that feeds electricity back into the grid. Behold, you have stored electricity, which has been done very efficiently with minimal loss. All you need is a hoist, a heavy weight and a vertical distance through which the weight can move up and down.
That vertical distance is crucial – the bigger it is, the better. Disused redundant mineshafts have been investigated for the purpose, but Swiss company Energy Vault has produced the world’s first commercial-scale Gravity Energy Storage System (GESS) using above-ground lattice structures with hoists at the top of them.
The 25MW/100MWh EVx Gravity Energy Storage System (GESS) is in Rudong, Jiangsu Province, outside Shanghai in China and is currently being commissioned. It is directly adjacent to a wind farm and the national grid. The system is projected to achieve a roundtrip efficiency exceeding 80% and to have a projected operational lifespan of 35 years. Peak power output is 25MW while the total energy stored is 100MWh, which can be released over a four-hour period – the length of time it takes the weights to fall. A second project, at Zhanguye City, is under construction. This will be slightly smaller at 175m, storing 68MWh of electricity that can be released at a peak rate of 17MW. The hoists of these projects need few unusual features as off-the-shelf models suffice.
It is heartening to know that run-of-the-mill electric hoists might play a crucial part in saving the world.