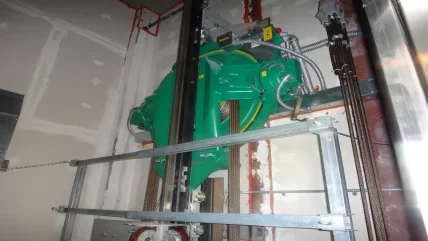
Hazardous conditions may exist in a wide range of industries where hoists may be used, not only due to products but also materials such as volatile solvents or naturally occurring emissions. Common examples of hazardous materials, depending on concentration in air or oxygen, include hydrocarbon gases and vapours, dusts of coal, wood and some metals, flour and grain dusts, combustible fibres and powdered plastics. Refurbishment and maintenance activities are worthy of special note in that operators need to be aware of what vessels have contained in case of flammable residues. Thus ship repair (as well as shipbuilding), tank maintenance and industrial demolition may need explosion-proof equipment.
Consequently any equipment used in areas affected by such hazards, whether frequently or intermittently, must be suitable for use, principally by avoiding the generation of sparks or flame which might ignite explosive mixtures or by preventing contact between the two.
There are two main groups of hoists that may be suited to hazardous atmospheres based on the motive power: air-powered (pneumatic) or explosion-proof electric. For practical purposes hydraulic hoists will also require explosion-proof electric drives for the power pack and must use non-flammable hydraulic fluids.
Compressed air has long been a means of supplying power to mechanical equipment used in hazardous atmospheres. Provided there are suitable precautions taken to avoid sparks generated by the discharge of static electric charges (such as using suitable materials and earthing), there is no direct source of possible ignition.
In normal use, the making or breaking of powered electric contacts (in motors, switches and relays) can easily generate sparks, which can ignite a hazardous atmosphere. Although reduction of circuit voltage can render contacts non-hazardous, this is usually impractical for most drive (as opposed to signal) requirements. Therefore the equipment that can generate hazardous sparks has to be housed in an explosion-proof or flameproof enclosure. By means of its construction the enclosure ensures that no flame escapes from the enclosure into the wider hazardous atmosphere, even if the hazardous substance, such as a flammable gas, can enter the enclosure. Thus, as examples, the enclosure has to be strong enough to contain any explosion without losing its explosion-proof properties, and any joints used in its construction must have a construction that prevents the passage of flame to the general atmosphere in all circumstances.
The difference
The two types of equipment – electric and air – are almost exact counterpoints. Many air hoists have a simple vane motor design, but they rely on a possibly complex network of compressed air. Explosion-proof hoists have a complex architecture, but rely only on a simple mains cable for power.
“Whenever possible an air hoist is the most cost-effective lifting solution for an explosion-proof environment,” says Lift-Tech product manager Greg Miskowiec. “Being air-powered it contains no electrical motors, electric components or circuitry, so it is substantially explosion-proof.”
But the installation can be critical. “Delivered air pressure is key to the performance of an air hoist,” Miskowiec points out, “in allowing it to obtain the top hoisting speed and lift for its rated load capacity.”
In other words, there seems to be little point in installing a full compressed air system for a couple of hoists, but in many industries containing hazardous atmospheres a compressed air network will already be available. If smaller, maybe portable, compressors are being considered it should be examined where these can be sited safely, since the compressor drive might also present an ignition source.
Pneumatics are often used on compressor stations, in gas or oil exploration for example, where it is not worth getting power to the job site and it is cheaper to have independent compressor stations that are powering all the equipment, says Axel Brandt, Detroit Hoist operations manager.
Air hoists are more likely to suffer from poor power supply than electrical hoists since compressed air supplies are often subject to lower maintenance standards. Leaks or over-long supply routes can result in unacceptable pressure loss resulting in insufficient pressure at the hoists for optimum performance. A more dedicated, fairly local, compressor is one answer but there again may be location problems for explosion-proof zones. Air hoists may also be made to be tolerant of lower pressures. Most JDN air hoists are available for operation at 4 bar as well as the usual 6 bar, making pressure loss acceptable in most circumstances.
The degree of explosion –protection has an obvious effect on cost. “The cost to explosion-proof a hoist can vary dramatically,” says Greg Miskowiec, “depending on the hoist motor power and the class, group and division of (hazardous) environment to be worked in. For a typical 5t hoist the cost addition to make the hoist suitable for a Division 1 environment can double the price of the hoist, while a Division 2 environment make-up adds only 10-20% to the costs of the hoist. Again, this is why it’s more costs advantageous to use an air-powered hoist in hazardous environments.”
Performance
The application of hoists will determine the required performance. Will the hoist be expected to perform one task or be flexible enough to perform several? Will virtually continuous operation be required (necessitating high efficiency), with a high number of starts and stops (necessitating low thermal build up), or will use be intermittent? Is a simple hoisting or supporting duty required or will there be multi-direction operation on a crane?
Manfred Mueller, marketing manager of air hoist manufacturer JDNeuhaus says that air hoists have no limit on total operational time or on the number of starts and stops per unit time, due to self-cooling action. Air hoists can therefore be particularly suited to ‘hot work’ industries such as foundries, steelmaking and cement making. In comparison, lower rated electric motors may be subject to limitations due to overheating, without special cooling facilities.
Otmar Buhmann, Stahl CraneSystems marketing manager, says that electric hoists’ travel and hoisting speeds do not depend on the suspended load, unlike air hoists, and there are no delays at switch on. Air hoists may take a moment to build up air hoist pressure, he says.
Francesco Giovanetti of Italkrane claims that its explosion-proof electric hoists are superior in terms of performance, flexibility and ease of use, and maintenance including resistance to adverse atmospheric conditions.
He points out that its electric explosion-proof hoists can be controlled using an inverter facilitating ‘soft’ starts and multi-speed operation. Stahl CraneSystems also have a standard 2-speed design.
If multiple explosion-proof hoist installations are required, such as on travelling cranes, the manufacturers of electric hoists claim an advantage with simpler control systems for three or more directions. The control equipment will be similar to that for standard hoists (lightweight, pendant controls with optional warning lights and key switch) whereas pneumatic controls would tend to be more complicated.
Failsafe?
An important consideration with all hoists is failsafe mechanisms although this is likely to be even more important in potentially hazardous atmospheres if sparks could be generated by inappropriate operation. Common regulations specify that devices must be incorporated to prevent operation during overload, whether accidental or ‘deliberate’.
Mueller also points out that the air motor halts without any consequent damage, and with no overheating due to high torque on stalling or jamming. No other special protection facilities are required.
Stahl CraneSystems’ Buhmann reports that the company’s electric explosion-proof hoist motors are protected by PTC thermistors, and the brakes by temperature controls. There is electrical overload protection and a sprung brake is applied in the event of power loss. On Stahl CraneSystems hoists a lowering device to recover the load after trip-out or emergency braking is optional.
Hoists supplied by Lift-Tech are provided with either mechanical load brakes within the hoist’s drive train and/or spring-set motor brakes that can be either electrically or air released. In the event of excess loads the hoist can be limited or stopped through the use of load cells, over-capacity limit switches or a slip-clutch in the hoist drive train.
Maintenance
If electrical power is a preferred choice then factors such as the likely higher purchase cost of explosion-proof equipment, and regular maintenance by qualified personnel must be considered.
Service requirements tend to be simpler with air hoists even if more traditional models can be temperamental. Disconnection of an air hoist for maintenance consists of disconnecting the supply hose and removing from the mounting. JDN air hoists are manufactured to a modular design, which is claimed to make maintenance easier with ready access to all parts, and a minimal number needing attention.
Removal of an explosion-proof hoist will require isolation of the electric supply, specialist knowledge for disconnection of the supply cable, and a specially qualified electrician to work on whatever is required. All hoists are, of course, subject to regulatory testing for safety and general operation.
Otmar Buhmann reports that the Stahl ‘de’ concept of explosion-proof hoist design combines a flameproof housing (a ‘d’ panel) for the hoist motor with an adjacent special junction box (‘e’ junction box). This is claimed to reduce installation and maintenance time. On the other hand, it is debatable whether it is easier to disconnect cables or hoses.
Related Files
Second edition (2005) of the EU’s directive on explosive atmospheres