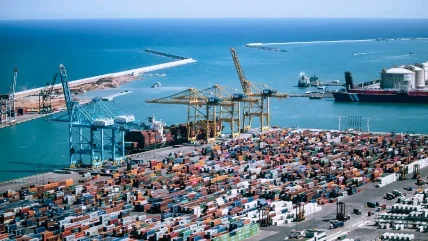
Port operator DP World Yarimca recently announced it is the first port in Turkey to integrate remote-controlled electrified cranes in its operations. The move is part of the terminal’s Zero Tolerance safety project, which has yielded a significant reduction in workplace accidents, with lost time incidents at Yarimca reduced by 50% since 2018.
This follows the company’s 2022 announcement that it reduced risk of injury by 40% across its European portfolio by investing €80m ($87.5m) in key safety practices and equipment upgrades.
Capable of handling the world’s longest vessels simultaneously at its two berths, DP World Yarimca’s Zero Tolerance project, which was launched in 2018, aims to raise awareness of health and safety measures and increase adherence to the port’s health, safety, security and environment (HSSE) regulations.
The eight remote-controlled electrified quay cranes and eight remotecontrolled electrified gantry cranes were commissioned as part of a world-first pilot project to increase safety at the terminal.
“Introducing new technologies and digitalising our operations has been shown to increase efficiency drastically in a sector where business is often done with outdated tools,” says Kris Adams, CEO, DP World Yarimca.
“Our Zero Tolerance project has been a testament to the combined power of protocol and technology, and we are proud of how this has improved safety in our terminal.”
The quay cranes are equipped with collision sensors and provide an additional layer of protection for terminal employees.
Integrating remote-controlled cranes has also reduced the number of pedestrians in the terminal area, which in turn has eased terminal traffic and protected vehicle drivers inside the port, according to DP World.
Another outcome of this project is that all terminal operators wishing to enter the port are required to enrol in an HSSE training programme and are given a certificate upon completion.
Taking this approach helps DP World identify and address concerns and reduce the risk of injury on-site. Violating the rules of the system results in penalty scores – or even refusal to enter the port.
Enoma Woghiren, head, HSSE, DP World Europe, says: “Safe terminals mean more efficient cargo handling, increased employee wellbeing, and increased cargo visibility. Our operations in Yarimca are an example to our business and the industry of how we can successfully implement new equipment and policies to keep our people safe.”
KUENZ
In other news, the commissioning of a semi-automated and remote-controlled crane for CFL multimodal’s terminal in Bettembourg-Dudelange, Luxembourg, has significantly increased the site’s handling capacity while providing more quality and safety in operations. For Kuenz, the mastermind behind the new crane and CFL multimodal’s long-standing partner, the crane is not only about security and trust but about responsibility towards society and the environment.
CFL multimodal is a major intermodal player in consolidating multimodal transport flows across Europe and beyond, while its terminal in Bettembourg- Dudelange has four 700m-long tracks allowing it to handle multiple daily trains and, up until the new crane’s arrival, approximately 150,000 intermodal transport units (ITUs) a year.
Austria-based Kuenz is known for developing cranes functioning with remote operation systems offering zero-emission operations. The Remote Operation Stations (ROS) that Kuenz deploys are key for the new and existing cranes that CFL multimodal’s terminal operates and its technological head start compared to other sites.
It is not the first time the two companies have worked together. Kuenz’s new semi-automated crane is the third one commissioned in Bettembourg. The first two were commissioned in 2015 and work with the same principles.
“We offer a variety of intermodal logistics solutions for the transhipment of goods that help the environmentally friendly rail transport develop its potential throughout Europe. The investment into the latest Kuenz technologies for gantry cranes, a future capacity of 235,000 ITUs, and the operation of two rail motorway platforms for handling 300,000 ITUs per year enables us to respond to the increased market demand for sustainable transport solutions,” says Daniel Feyder, director, CFL terminals.
“At the same time, we will provide our customers with more reliability, resilience and visibility along their supply chains by opening up new alternatives to already congested roads. Our intermodal terminal has reached the threshold of almost one million handlings to date – and since its inception in 2017 – enabling the crossborder transport to seven countries, saving around 110,000 tons of CO2 annually.”
Vincent Pelletier, area sales manager, Kuenz, says the company has “implemented automation in the intermodal world and has the most references in the industry. Many cranes around the world have been running very successfully for many years in intermodal terminals in Europe and the US, with quality performance resulting in orders for more than 20 remote-operated intermodal RMG [rail-mounted gantry] cranes for higher safety, productivity and flexibility”.
Regarding Luxembourg, Raphael Rüf, project manager Kuenz, says the company is “a proud part of Luxembourg’s infrastructure network and holds a key position in the expansion of the intermodal network in Europe”.
The fact that Bettembourg is one of the most complete terminals in Europe with immense growth owes much to the two Kuenz RMG cranes being there since 2015. However, the recently commissioned third RMG crane will make an even more significant difference.
Highlights include the crane being semiautomated, while it can be operated from an ROS. Remote operations improve the terminal’s productivity at lower costs while improving safety via a dedicated concept and an efficient camera system. On top of that, they make the crane operator’s job more attractive and help tackle the shortage of skilled workers.
Kuenz’s RMG crane will also feature a non-spanned double girder, a rail span of 41.67m, and two single cantilevers of 13m each that will be equipped with a piggyback spreader. A terminal operating system/crane management system interface will allow reliable data flow and tracing.
SIEMENS
Siemens has taken the next step in advanced automation by “developing an efficient system to support remote landing operations”. Its Final Landing System (FLS) assists the operator to use a cranes’ full capacity, at the same time achieving safe and accurate operations.
FLS supports remote operator guidance when positioning in auto mode. “Using the latest camera or laser technologies, together with assistance via automatic functions, the operator has high control for pick-up and set-down operations,” says Siemens.
“FLS assists the operator to land the spreader with high precision by means of multiple accurate container recognition functions. For different scenarios, the system contributes for a superior cranes’ performance and accurate stacking,” the company continues.
“The landing is guided and actively controlled in six degrees of freedom allowing movements in three-dimensional space to stack accurately based on specified ground gradient. The sensors provide velocity and height measurements defining all objects positions.”
FLS integrates all the data for gantry, trolley, trim, list, skew and hoist allowing the operator to find the best angle to stack accurately. “In that way, FLS contributes to shorten the cycle time of automatic container handling, resulting in superior crane performance,” says Siemens.
Finally, FLS can use cameras to recognise the top corners of the container underneath at which the empty spreader lands on. The cameras used for remote operations can also be used for FLS, avoiding extra investments.