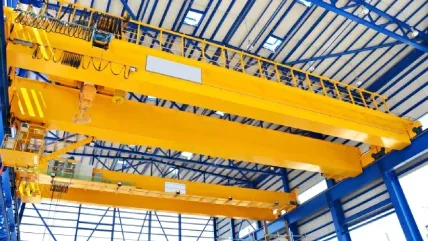
Chinese crane manufacturer Yuantai Crane has delivered three 10-ton overhead cranes to a client operating a precast concrete plant near Dhaka, Bangladesh.
The plant produces beams, wall panels, and modular segments for residential and infrastructure projects, and needed a reliable solution to lift heavy concrete elements.
It has previously used a combination of single girder hoists and mobile cranes, which slowed production and posed safety risks.
Yuantai supplied three double girder overhead travelling cranes, each with a safe working load (SWL) of 10 tons and an ISO 4301-5 duty class M5 for up to 350 cycles per day.
The new double girder overhead cranes are designed to address the issue by providing a more reliable and efficient solution.
They are expected to significantly improve operational efficiency and safety.
Yuantai Crane, in a LinkedIn post, said: “We recently supplied three 10-ton double girder overhead cranes to a precast concrete plant near Dhaka, Bangladesh, addressing their challenges in handling heavy concrete elements efficiently and safely.”
With a 25m span and travel on 43kg/m rails mounted to existing runway beams, the new double girder cranes offer reduced deflection under load and increased lateral stiffness.
The main girders are constructed from high-strength steel and validated through finite-element analysis.
End carriages feature forged steel wheels and sealed roller bearings to ensure low rolling resistance and dust resistance.
The hoist trolley is equipped with an electric wire rope hoist, delivering lift speeds of 8 m/min and trolley travel speeds of 20 m/min.
The cranes feature control and safety systems, including an ergonomic pendant control with an IP65 rating, an overload limiter with visual and audible alarms, mechanical limit switches, and variable frequency drives for smooth operation.
Emergency stop functions are available on both the pendant and an optional radio remote.
Electrical and environmental protections are in place, with motors featuring class F insulation and IP54 protection.
Control panels include overload relays and phase-failure protection. Cables are housed in steel conduits to prevent damage from mechanical and chemical exposure.
Yuantai said the installation process involved re-aligning and shimming existing runway rails and installing vibration-damping pads.
Pre-welded rail sections were bolted to runway beams, allowing installation and testing to be completed within 48 hours per bay.
A detailed installation plan minimised production disruption by scheduling work over two consecutive long weekends.
After the installation, the company conducted initial no-load runs and static proof tests at 125% SWL (12.5 tons) to verify structural integrity, along with dynamic load tests.
Operator training included safe lifting procedures, daily inspection checklists, and emergency protocols, with a final sign-off documenting acceptance by the plant manager.