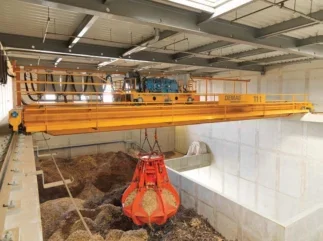
The plant generates some 13 million KWh of electricity from renewable resources every year. Only natural woodchips from forestry and landscaping work are used. The heat generated at the same time – some 60,000 MWh – is delivered to a neighbouring district heating plant, which supplies more than 8,000 households. Combined heating and power generation provides the best possible use of the energy contained in wood solid fuel, with a utilisation factor of 85%. The installation cuts annual carbon dioxide output by an impressive 23,000t.
Automated crane technology plays a key role in the process. The fully automated double-overhead travelling crane that delivers the woodchip to the furnace girder is fully controlled by Demag’s warehouse management computer. The crane has an 11t capacity a span of 16.4m, as well as a lifting height of 24.5m.
Long and cross-travel speeds are 50 and 40m/minute with lifting speed of 50m/minute. The specially designed multi-jaw grab has a capacity of 8m3 and can deliver 140m3 of material an hour. It reliably picks up loads ranging from finely shredded wood to small branches and compacted material. Sway from the crane’s long and cross-travel motions is eliminated by the Demag active load-sway damping system – potential collisions by the grab against the walls are therefore avoided.
The wood-fired cogeneration power station was planned to achieve optimum utilisation of the space. For this reason, the solution with the automatic crane was given preference over stores served by wheel-loaders, for example. That alternative would have caused more exhaust fumes and higher noise emissions and would also have required more staff to operate.
The motor-driven multi-jaw grab is specially designed for handling wood in its natural state. It reliably picks up loads ranging from finely shredded wood to small branches and compacted material – at least 140m3 of material has to be handled per hour.
Some 32,000t of woodchips are supplied by truck to the station every year. Access to the 300m3 tipping pit is controlled by means of an integrated magnetic card scanning system. As soon as a truck has passed through the weighing station, the barrier is opened and the area above the tipping position is blocked for any crane operation – this prevents damage to the grab caused by falling material. As soon as the truck has deposited its load, the crane receives the command to start clearing the tipping pit. Staff at the installation check the quality of the incoming material in advance and assign it to one of three previously defined fuel grades, each of which has its own storage zone. The automatic crane then deposits the fuel into the appropriate zone. At a later stage it transfers it to a 700m3 silo, from where it is fed into the furnace. When the fill level in the silo falls below a minimum level, the control system of the crane automatically refills it from the three storage zones in the correct proportions to achieve optimum burn.
As well as its actual transport duties, the process crane is also responsible for blending the materials. This needs to be done, for example, if quality assurance reveals that wood cuttings from landscaping work are too wet and need to be blended with high-quality wood from forest sources. As soon as the required blending ratio has been set via the user interface of the Demag warehouse management computer, the crane automatically approaches the three corresponding zones, picks up the material and blends it in the silo.
Further strategies were included in the control system by the crane supplier. For example, when the grab buries itself in the material to pick up a load, the grab jaws are not initially fully closed. The crane takes the strain and a small amount of material trickles out. The grab can then be closed with the optimum fill level.