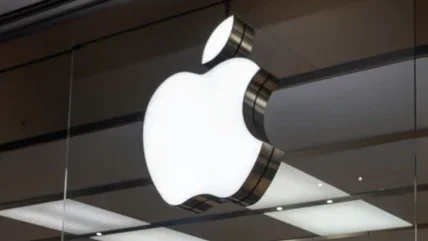
GlobalData is currently tracking industrial construction projects with a total value of $4.4tn at all stages from announcement to execution. This pipeline mostly comprises industrial buildings, manufacturing plants, mines and mineral processing, and other related facilities.
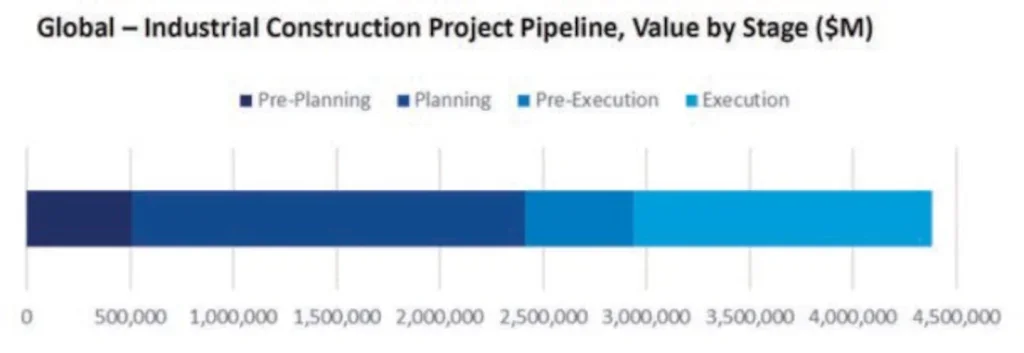
The pipeline is marginally skewed towards the early stages, with the share of projects in the pre-planning (announced and study) and planning stages accounting for 55.1%, while projects in pre-execution (design, tender and award) and execution stages accounting for the remaining 44.9% of the pipeline, by value.
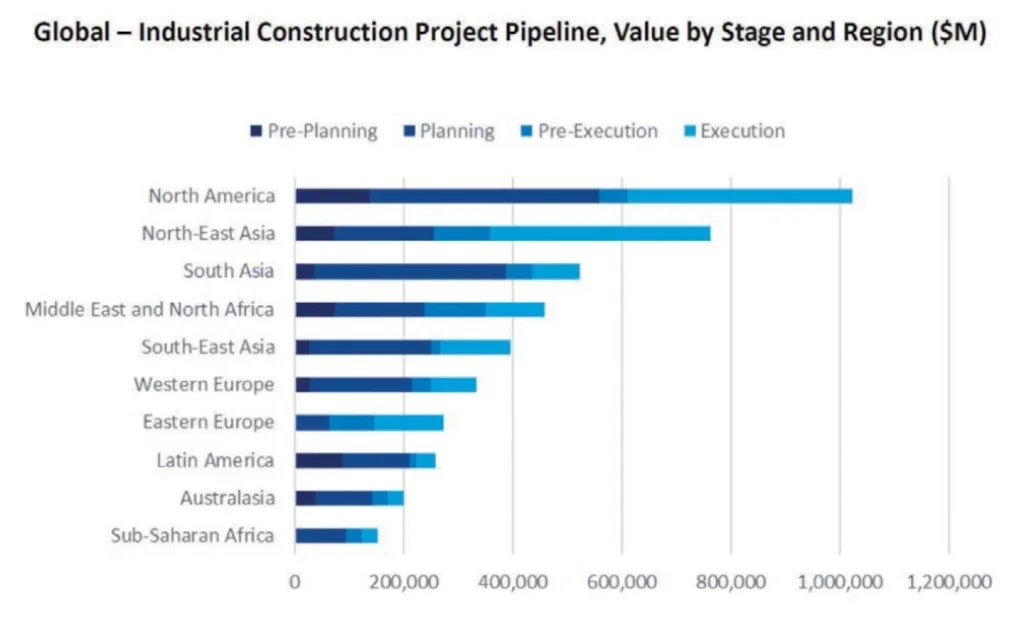
Some of the major projects on which construction is expected to start in 2025 include the $11.3bn Rempang Solar Panel Factory project in Indonesia, the $11bn Dresden European Semiconductor Manufacturing Plant project in Germany, the $10bn Hai Duong Pharmaceutical Industrial Hub project in Vietnam, and the $9bn Bantry Bay Green Energy Plant project in Ireland.
SOUTHEAST ASIA
Southeast Asia’s strong manufacturing base has largely benefitted from the rebound in global consumer demand. Investor confidence in the region has been further boosted by the increase in trade barriers put in place on China by the US.
Indonesia and Vietnam collectively account for 66.6% of the Southeast Asian industrial construction pipeline, by value.
The Indonesian government is implementing new incentives to boost production, particularly in the electric vehicle (EV) sector. The government aims to become one of the world’s top three producers of EV batteries, targeting a production capacity of 140GWh per annum, by 2030.
In December 2024, Apple, the US-based technology company, announced its plan to invest $1bn in an Indonesian manufacturing plant to produce smartphone components. Furthermore, in December 2024, according to the Ministry of Planning and Investment, the government of Vietnam has attracted 174 foreign direct investment (FDI) projects in the semiconductor industry, with a total registered capital of $11.6bn.
Key developments as part of investment include an agreement signed between the government of Vietnam and Nvidia Corporation, a US-based technology company, for the construction of an Artificial Intelligence (AI) Research and Development Center, and investment of $4.1bn for the construction of two semiconductor testing and packaging factories.
GlobalData is currently tracking industrial construction projects in Southeast Asia with a total value of $395.4bn, which includes projects from announcement to execution stages. The overall pipeline in the region is relatively less developed, with projects in the preplanning and planning stage accounting for 63.6% of projects, totalling $251.3bn in value. Assuming all projects move ahead as planned, spending will rise from $60.3bn in 2025 to $80.9bn in 2026.
The largest project underway in the pipeline is the $28bn Tanah Kuning Industrial Park Integrated Ferronickel Complex project, which is in the planning stage. Tsingshan Holding Group Co Ltd (THG) is planning to build an integrated ferronickel complex in North Kalimantan, Indonesia.
The project involves the construction of a ferronickel smelter with a capacity of 1.5MTPA, a stainless steel production facility with a capacity of 2MTPA, a carbon steel production facility with a capacity of 10MTPA, a ferromanganese production facility with a capacity of 500,000 tons per annum (TPA), a ferrosilicon production facility with a capacity of 200,000TPA, an aluminium production facility with a capacity of 1MTPA, a ferrochrome production facility with 1.2MTPA, and a 5,000MW hydro-electric power plant to supply power to the complex, and the installation of machinery and equipment, safety and security systems.
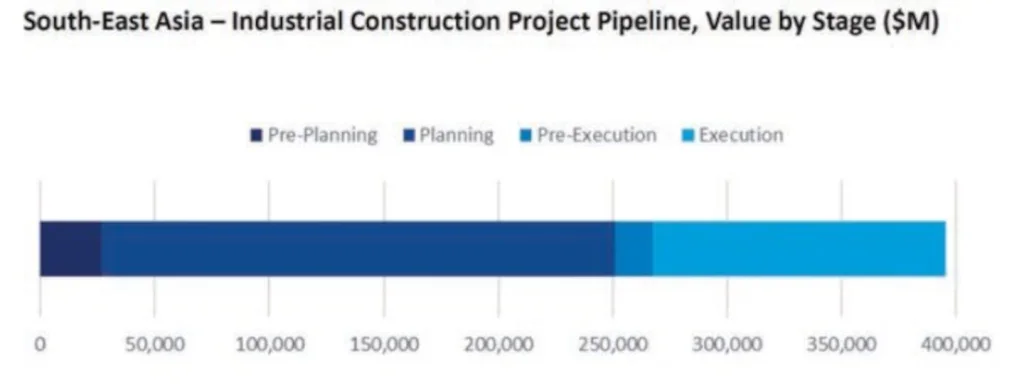
SOUTH ASIA
South Asia’s project pipeline is largely made up of projects in India, with the country making up 91.9% of the region’s pipeline value. Over the coming years, investments in the Indian manufacturing sector will be driven by the government’s aim to boost domestic manufacturing, to reduce imports from China.
In November 2024, the Indian government announced its plan to attract investments worth $40bn by 2030 for the construction of electric vehicle (EV) manufacturing units, and lithium-ion battery facilities.
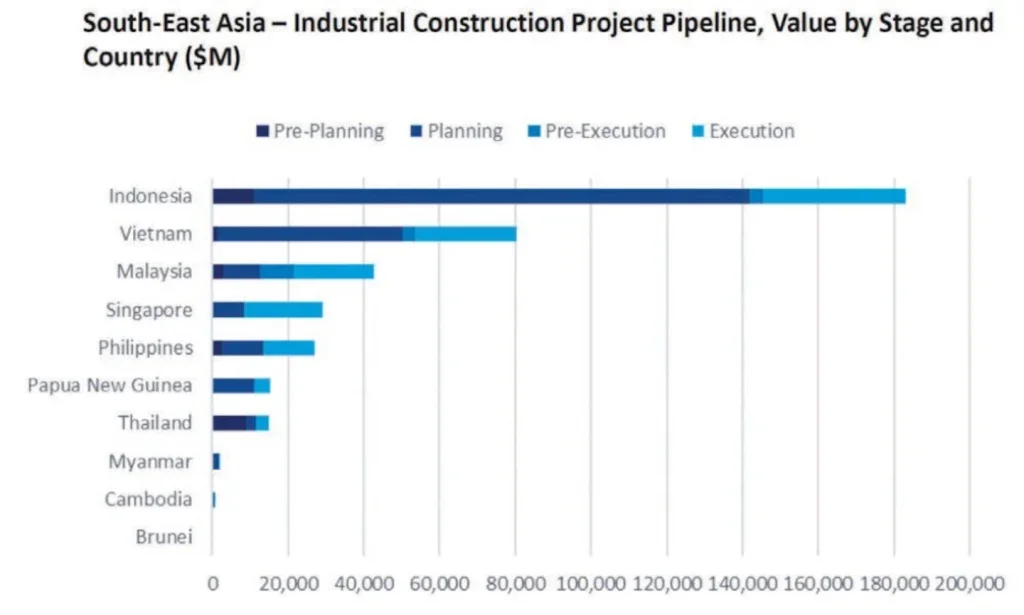
Additionally in January 2025, the Indian government also announced its ambitious target of securing $500bn in investments for semiconductor manufacturing projects by 2030.
The plan focuses on strengthening domestic manufacturing capabilities and building a robust semiconductor ecosystem, with an emphasis on fostering private sector involvement to position India as a global hub for electronics manufacturing by 2030. Previously, in September 2024, the Indian and US governments signed an agreement to unlock $1bn for clean energy technology manufacturing in India. The partnership aims to unlock multilateral finance through the International Bank for Reconstruction and Development (IBRD) for projects that supports catalysing India’s domestic clean energy supply chain buildout. In the initial phase, the two nations will collaborate on providing financing to support projects such as renewable energy, energy storage, power grid and transmission technologies, and zero emission vehicles, among others.
GlobalData is currently tracking industrial construction projects in South Asia with a total value of $523.4bn, which includes projects from announcement to execution stages. Of the total, India’s industrial project pipeline accounts for $481bn.
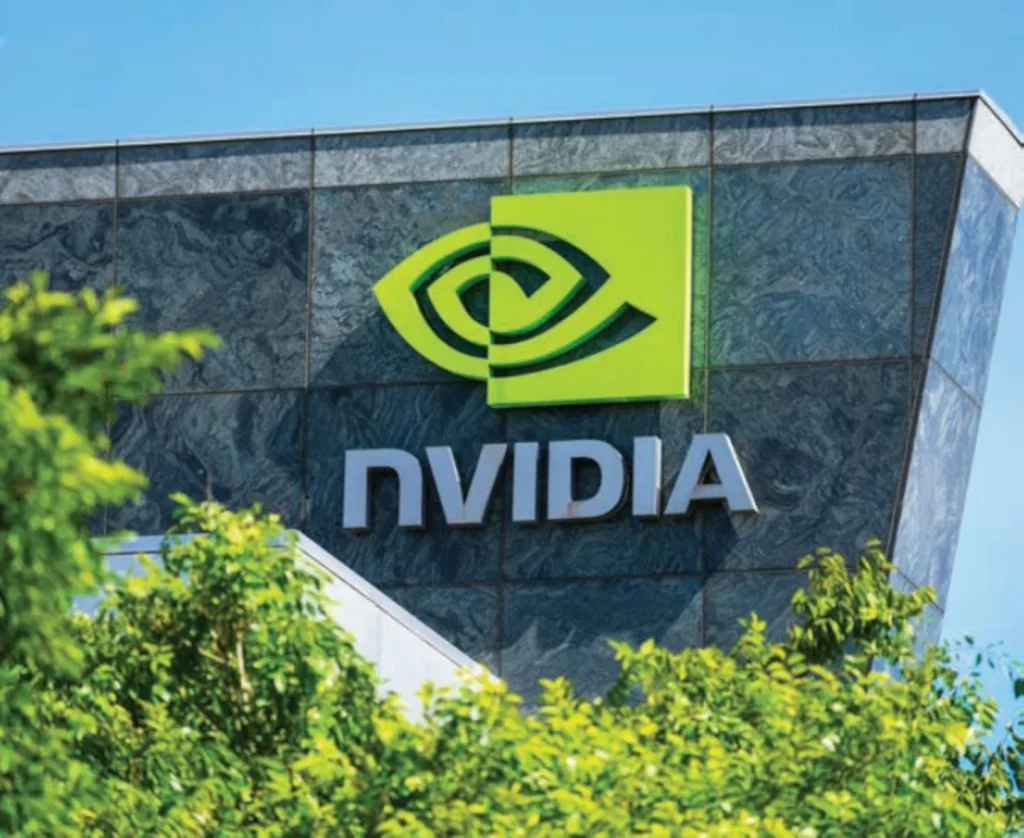
The overall pipeline in the region is skewed towards the early stage, with projects in the pre-planning and planning stages accounting for 74.1% of projects by value, totalling $387.6bn in value. Assuming all projects move ahead as planned, spending may rise from $44bn in 2025 to $130.4bn in 2026.
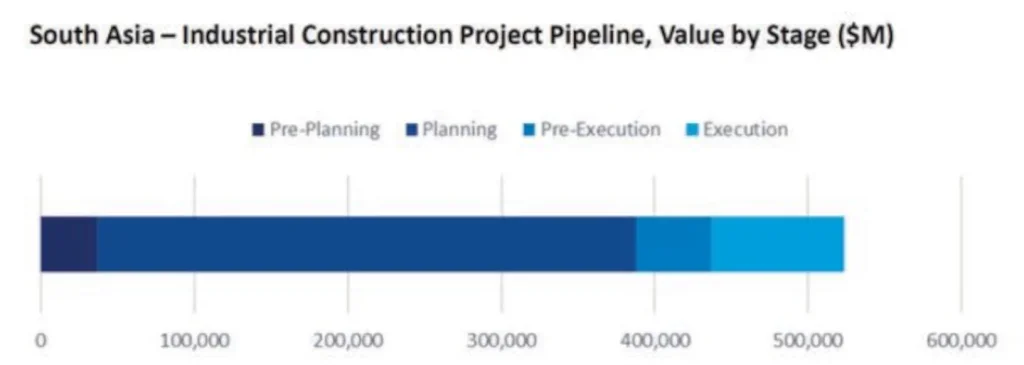
The largest project in the pipeline is the $24.4bn Odisha Semiconductor Manufacturing Facility in Odisha, India, which is currently in the planning stage and will complete in H2 2027. The project will be developed in phases, with an investment of $3.6bn in the first phase.
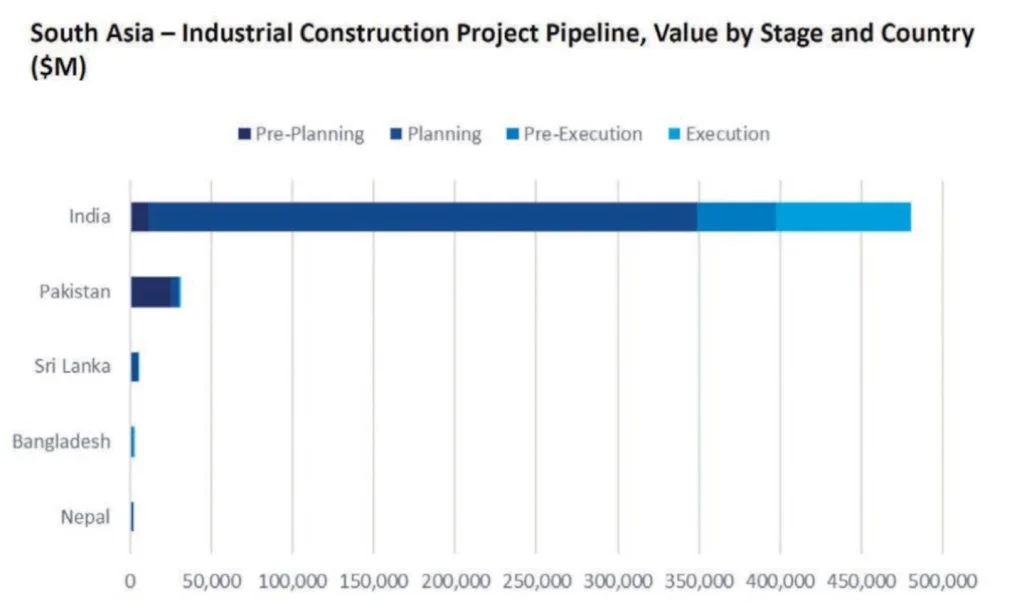
YOKE ISSUES DIGITAL PRODUCT PASSPORTS
YOKE Industrial Corp’s range of lifting and rigging products are now equipped with digital product passports (DPP), as industry conforms to the European Union’s Ecodesign for Sustainable Products Regulation (ESPR).
A DPP is a data management tool that records a product’s lifecycle information, including material composition, energy performance, maintenance guidelines and recycling methods. A DPP, therefore, promotes compliance and transparency, while improving resource efficiency and supporting circular economy goals.
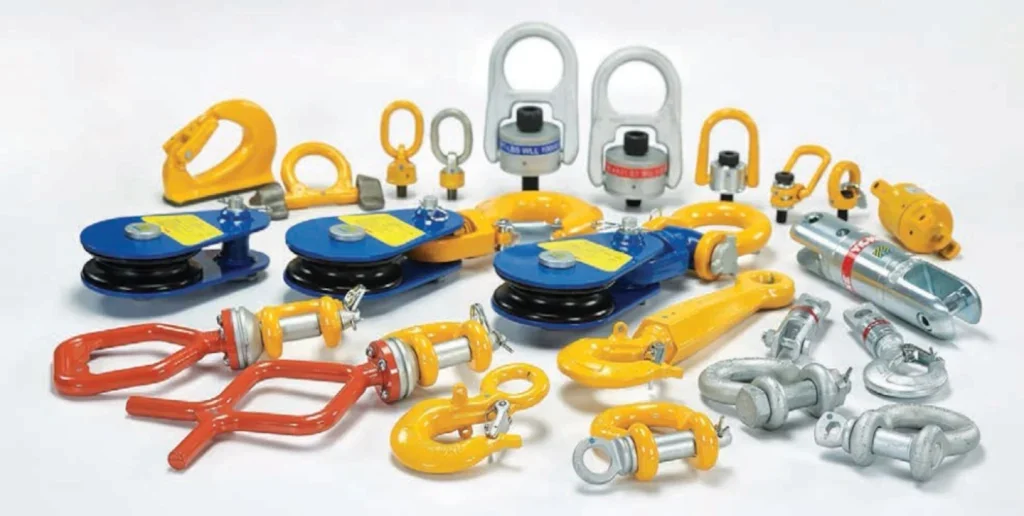
YOKE’s catalogue includes Grade 80 and Grade 100 lifting chain fittings, swivel hoist hooks, shackles, angular contact swivels, wire rope clips and lifting points. It integrates radio frequency identification (RFID) chips within every item, allowing end users to utilise a DPP throughout the product lifecycle.
It is less than two years until everyone is expected to be working to the EU Machinery Regulation and the Machinery Directive 2006/42/ EC is repealed. One of the most significant changes is the inclusion of original certification and manuals to be supplied digitally with products.
In the meantime, the ESPR aims to significantly improve the sustainability of products placed on the EU market by enhancing their circularity, energy performance, recyclability and durability. Effective last year, it replaced the Ecodesign Directive 2009/125/EC and established a framework for setting eco-design requirements on specific product groups. It expands the Ecodesign Directive to cover virtually all physical products, and reinforces the range of eco-design requirements that can be set.
YOKE said it has campaigned for RFID and software as a service (SaaS) to be more widely utilised by the lifting industry for many years, and remains dedicated to simplifying and digitalising the processes around compliance and traceability for equipment management.
Steven Hong, president at YOKE, said: “Not only is technology enabling industry to conform to guidance, but it is also moving us away from traditional hard labels, which present many issues, such as difficulty in updating, poor accuracy, and being affected by wear or fading, making it hard to keep up with fast-changing market needs.
“In contrast, technology provides more accurate data, better transparency, can be updated anytime, and remote tracking, without being impacted by the environment. This change not only improves data management efficiency but also reduces resource waste, supporting the goals of a modern circular economy and sustainable development.”
LEEA LATEST
William Ng, the Lifting Equipment Engineers Association’s regional manager, Southeast Asia, fills us in on LEEA’s latest regional event, held in Kuala Lumpur.
Can you provide an overview and a summary of the event?
The regional event was held on the 27 February in Kuala Lumpur with about 70-plus attendees from 30 companies. We had three guest speakers: Stuart Glennie from Kito Crosby, Ben Burgess from William Hackett, and Frank from In-Source Option.
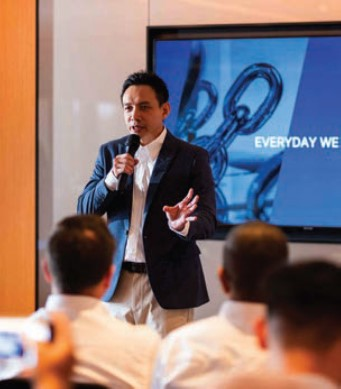
The Malaysia Department of Occupational Safety and Health has representatives attending as guests of honour. LEEA regional managers from UK, Middle East, and Australia and New Zealand were there to provide an update on the activities of their region. Matt Barber, presented the improvement projects that are happening in LEEA and promoted the Global Lifting Awareness Day (GLAD). The event closed with networking at the end.
Are there plans to hold another member event next year?
Southeast Asia (SEA) regional events will happen at least two to three times per year, and next year we’ll definitely be planning to hold the events. The target is to hold regional events with other [topics]. On 19 May we will have a regional event with the same format as the one we had in Kuala Lumpur.
From your perspective, how is the Southeast Asia market performing at the moment?
Within the SEA region, we still have a lot of potential for growth. Especially when we are targeting partnering with the end user and government sectors to do more on achieving our LEEA mission. The region demand for LEEA Accredited Training Courses is also growing, which gives us the opportunity partner with more training centres to meet the demand.
What new members have you onboarded recently in the region?
We have a mixture of new members from inspection companies, such as TUV Nord Malaysia, PT PJ-Tek Mandiri, PT. Baraca Teknis Spesialis, and also from training companies such as SEATAG Australasian Services Pte. Ltd, and Slings suppliers such as Mega Sling & Services Sdn Bhd.
VINALIFT INSTALLS 12.5-TON OVERHEAD CRANE AT PETROCHEMICAL COMPLEX
Vietnamese lifting equipment provider Vinalift has designed, manufactured and installed a 12.5-ton overhead crane at the Southern Petrochemical Complex Project in Vung Tau City, Vietnam.
The double girder overhead crane, installed in a designated safe area, adheres to quality and occupational safety standards.
It facilitates the loading, unloading, and transportation of materials and equipment at the petrochemical complex.
The crane features a single hook with 360° free rotation, a lifting height of 8.25m with a maximum of 10m, and a crane span of 10.8m.
It operates along a runway length of approximately 50m, powered by a 380V, three-phase, 50Hz supply with a control voltage of 48V.
Operators can control the crane via remote control or push pendant control.
Designed to FEM 1.001 standards, the crane falls under FEM 2m/ISO M5 duty class and functions within an operating temperature range of 0°C to +40°C.
The structure is constructed from SS400 steel, with a maximum wheel load of 105kN.
The crane offers a lifting speed of 4.0/0.6m per minute, a trolley travel speed of 20/5.0m per minute, and a crane travel speed of 30/5.0m per minute.
It features a lifting motor of 9.0/1.4kW, a trolley travel motor of 1.25/0.32 kW, and a crane travel motor of 1.25/0.32kW, all equipped with a DC brake system.
Also, the crane comes with enhanced safety features such as an overload protection device, a lifting limit switch, and cross and long travel limit switches. It also features a distance sensor for collision prevention and a travelling alarm system.
In a separate development, Vinalift has announced that its two 45-ton port handling cranes are stably operating at Long Son International Port in Vung Tau, Vietnam.
The cranes, with a load capacity of 45 tons, offer high precision and flexible operation, meeting the needs of loading and unloading containers as well as bulk cargo.
The cranes are significantly improving cargo handling productivity at the port, said Vinalift.