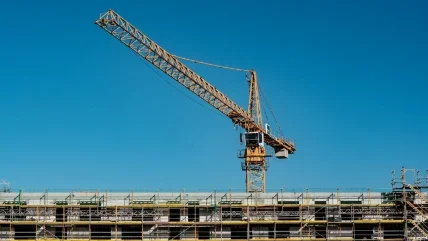
During my many years in the overhead crane and hoist industry it just amazed me how many people did not understand the difference between holding and controlled braking. Engineers, who design the systems, don’t always work with them. The plant maintenance person is assigned the responsibility of maintaining cranes and hopefully understanding how they work. I have stood back and listened to many different explanations, of just what is required and the difference between the two types.
What usually happens is that the explanation given to the typical maintenance or production person is too deep, and they may not understand. This article is an attempt to explain the topic in a down to earth, simple way. Only certain systems are covered, and others are touched on. We will only discuss AC motor control systems, and leave DC systems for another topic.
What is it and why do you need it? OSHA states that it ‘shall be used’. The OSHA definition cites ASME B30-2 CH 2-1.12. An extract from the latest version of the ASME code is shown, right.
Why do we need controlled braking? Well you can blame a little of it on Sir Isaac Newton and the law of universal gravitation which states: “Every piece of matter attracts every other piece with a force proportional to the product of their masses and inversely proportional to the square of the distance between them.”
I said that this was going to be a “no-brainer” explanation and I throw in the above statement. Sorry! Can we put this into a common sense language? You bet, and simply stated – GRAVITY. If you release the holding brake, because of gravity, the load will fall, unless you have controlled braking. Controlled braking controls the load at a safe lowering speed, after the holding brake is released.
Types of controlled braking
Some types of mechanical load brake are Weston, band and to use a worm gear. Electrical types include dynamic (AC and DC) and regenerative (AC and DC), both of which are explained later.
Countertorque is a way of applying power to a hoist in the hoisting direction. The motor torque (current), however, is not strong enough to hoist the load. The load is heavier than the motor torque can overcome, and the load will lower. The rotating magnetic field in the motor stator winding is turning clockwise (hoisting or counter-torqueing), but the motor is actually being pulled by the heavy load on the hook anticlockwise, i.e. lowering. Motor hoisting torque is regulated to control the lowering speed. The less hoisting motor torque there is, the faster the load will be “controlled lowered.” At a certain safe speed point, the control is switched to reverse the rotating magnetic stator field. Now the rotating magnetic field is going anticlockwise and the rotor is going anticlockwise, but faster than the motor field, and the system is now providing regenerative braking.
DC injection is a way of providing braking torque by polarising opposite magnetic poles. Opposite magnetic poles attract and the stronger the field, the stronger the controlled braking. The rotor must be in motion to provide current for braking energy.
Manufacturers of eddy current, or electrical load brakes, include Stromag, P&H with its Magnetorque, and Eaton Dynamatic.
Mechanical load brakes
Recent types run in an oil bath within the hoist gear case. Some older styles can be outside and can be a drum band type. The general principle of operation is that when hoist lowering is selected, the holding brake will be released (electrically released, spring applied) and the load wants to fall. A latching mechanism, usually a pawl type, engages and a ratchet friction disc is held stationary. The weight of the load closes and sets the load brake friction disc, and the motor will power down in the third quadrant torque phase and drive through the load brake. The mechanical load brake and the motor torque control the lowering speed.
Electrical controlled braking
To better understand some types of electrical controlled braking, we have to understand a little motor theory (terms) and different types of motors. Types of motor include the AC squirrel cage induction, wound rotor induction, DC series wound and shunt motors.
Terms relating to induction motor theory include:
• synchronous speed (rotating magnetic field) is 120 times the frequency divided by the number of poles
• full load hoisting speed is no-load rotor speed (synchronous speed) minus full load rotor speed. The difference is defined as “slip”
• slip can be positive or negative
• slip can be synonymous with internal and external motor resistance (important!)
• negative slip is the percentage of revolutions per minute (rpm) the rotor lags the rotating field when hoisting
• positive slip is the percentage of rpms that the rotor overhauls the rotating field when lowering a load
• generally, full speed hoisting is the synchronous speed minus slip
• full speed lowering is the synchronous speed plus slip (plus another variable, but not for this simple discussion)
• overhauling is the load pulling the motor rotor shaft faster than the motor rotating magnetic field. In a 60Hz machine, with a four-pole motor, the field is rotating at 1,800rpm, and the overhauling load is pulling the rotor at something above 1,800rpm.
Regarding AC regenerative and dynamic braking:
• a motor receives electrical energy, and produces mechanical energy
• a generator receives mechanical energy and produces electrical energy
• a generator requires a “prime mover” as its mechanical energy source.
Some prime movers are petrol or diesel engines, steam turbines, hydro dams, or an over-hauling hoist load. An over-hauling hoist load turns the motor into a generator. The energy generated returns power to the supply line or other type of electrical absorption load. The power losses put an electrical load, or drag, on the crane motor, which is now a generator, and control the lowering speed to a safe value. This is similar to a situation where a portable generator is running with a 50% load, and someone adds 50% load, the generator will slow down because of the added electrical load. The extra load causes the generator to “brake.”
There are some generally accepted rules and statements for AC regeneration:
• a motor will turn into a generator if overhauled and…
• there must be a power supply to the motor
• the motor must be pulled or driven above its rated synchronous speed to turn into a generator
• an overhauling load will pull the motor over its synchronous speed
In the case of dynamic braking versus regenerative braking, in very simple terms, the motor still must be driven over its rated synchronous speed, and on AC machines there must still be a power supply to the motor.
Rather than the power being returned to the supply line, the power is discharged, or dumped across dynamic
braking resistors, connected in the hoist power grid. It should be noted that there are some control schemes on the market that give a form of dynamic braking without having a power supply to the motor. This is known as a self-excited system. DC control systems, for example the P&H Safetorque design, provide this scheme.
Eddy current brakes
An eddy current brake is a rotating piece of machinery mechanically coupled to the high-speed motor drive train. The brake produces retarding torque which opposes load torque to control lowering speeds by “controlled braking”.
Generally, the torque is generated with fixed magnetic north and south poles which are excited by a DC power supply scheme. Retarding torque is only produced with motion and DC excitation. Eddy current brakes only retard load lowering speeds, they will not stop a lowering load.
They are generally used with wound rotor control schemes and are not usually used with squirrel cage motors. This type of brake can also be used to pre-load wound rotor motors, to produce a light load speed torque curve, because wound rotor motors are torque motors, with rising speeds at lighter loads.
Clarifying misconceptions
“Single speed and two speed squirrel cage motors require mechanical load brakes to meet the OSHA controlled braking requirement.” This is false! Single speed and two speed squirrel cage induction motors have regeneration braking when the load over-hauls and the rotor exceeds its rated synchronous speed. Regenerative braking meets the OSHA controlled braking requirement. It is a “no-brainer!” The speed will be synchronous speed plus rated slip and it does not require a special control scheme. NB: It must be understood, however, that mechanical load brakes do offer an extra margin of safety, i.e. used with an adjustable frequency drive (AFD), if the drive fails, and the holding brake does not set, the mechanical load brake may support the load. Because the AFD failed, it will not develop torque to drive through the mechanical load brake. When you use a mechanical load brake, however, other design factors must be considered, such as duty cycle, but that is another discussion.
“Controlled braking will hold a load when the holding brake is released.” False and maybe! Be careful! Some mechanical Weston type load brakes, a type of controlled braking, will hold the load if the holding brake is lifted. Some will not! A mechanical load brake is not considered a holding brake, although some will hold the load. “Load float,” on adjustable frequency or speed regulated drives is not controlled braking, it is a first quadrant power torque mode.
Wound rotor motor cautions
• They always require a controlled braking control scheme
• external slip resistance affects torque
• speed is controlled by torque
• with all external resistance in the motor secondary, and loss of controlled braking, the load may fall uncontrolled at very high speeds.
Braking with AFD drives
There are points to remember with hoist controlled braking with AFD drives without mechanical load brakes. Remember that when an AC induction motor is pulled, or over-hauled, over its rated synchronous speed, we have a generator. The braking will be regenerative or dynamic. Remember that synchronous speed is 120 x f/number of poles, where f = frequency. If the frequency is 60Hz, with four poles, the synchronous speed will be 1,800rpm. A four-pole machine, with a frequency applied at 60Hz, with a full load slip of 5%, with full load on the hoist, will lower at 1,800rpm plus approximately 5% speed. The motor, now a generator, will lower the load in a controlled rate at approximately 1,880rpm.
What will happen when we reduce the applied frequency? When we reduce the speed request, we lower the frequency. Assume a speed reduction request of 25%. The frequency will now be 45Hz. The synchronous speed will be 120 x 45/4 poles, or 1,200rpm. If we snap a picture, the motor is going at 1,880rpm and the synchronous speed (rotating magnetic field) is now 1,200rpm. Taking a snap shot in time, since the load is still overhauling the motor above its “new rated sync speed!”, we are regenerating. Since the difference is approximately 25%, higher retarding torque (regenerative output current), will develop to reduce the speed down to within 5% over the new 45Hz synchronous speed.
Bridge and trolley drives
When reduced speed is requested, these motions slow down using the regeneration, dynamic braking principle. Assume a 25% speed reduction request has been made, the frequency will now be 45Hz. Synchronous speed will be 120 x 45/ 4 poles, or 1,200rpm. If we again stop time, and snap a picture, the motor is powering at approximately 1,780rpm (pushing, not over-hauling), the synchronous speed (rotating magnetic field) is now 1,200rpm. Since the load (kinetic energy of the bridge) is now the prime mover, overhauling the motor above its “new rated sync speed!,” we are regenerating or dynamic braking the crane bridge.
Nick Flacco has been involved with the crane industry for more than 35 years, working in service, sales and training. He is western sales manager for new equipment at Morris Material Handling Inc. in the USA.